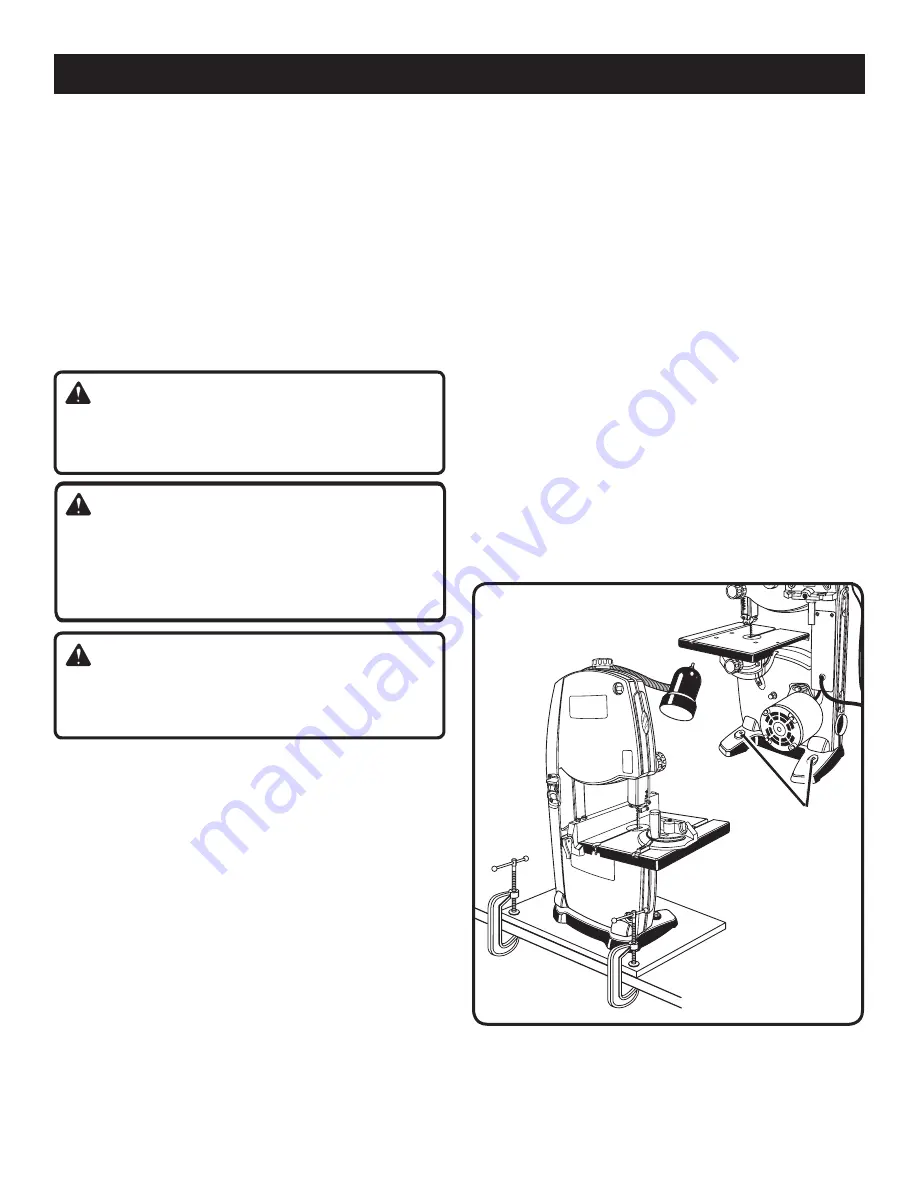
12
ASSEMBLY
HOLES IN
SAW BASE
Fig. 5
UNPACKING
This product requires ass
embly.
Carefully remove the tool and any accessories from the
box. Place it on a level work surface.
NOTE:
This tool is heavy. To avoid back injury, lift with
your legs, not your back, and get help when needed.
Inspect the tool carefully to make sure no breakage or
damage occurred during shipping.
Do not discard the packing material until you have care-
fully inspected and satisfactorily operated the tool.
If any parts are damaged or missing, please call 1-800-
525-2579 for assistance.
WARNING:
If any parts are damaged or missing, do not operate this
tool until the missing parts are replaced. Failure to do so
could result in possible serious personal injury.
WARNING:
Do not attempt to modify this tool or create accesso-
ries not recommended for use with this tool. Any such
alteration or modification is misuse and could result in a
hazardous condition leading to possible serious personal
injury.
WARNING:
Do not connect to power supply until assembly is
complete. Failure to comply could result in accidental
starting and possible serious personal injury.
MOUNTING BAND SAW TO WORKBENCH
If the band saw is to be used in a permanent location, we
recommend that you secure it to a workbench or other
stable surface. When mounting the saw to a workbench,
holes should be drilled through the supporting surface of
the workbench.
Each hole in the saw base should be bolted securely
using bolts, lock washers, and hex nuts (not included).
Place band saw on the workbench. Using the saw base
as a pattern, locate and mark the holes where the band
saw is to be mounted.
Drill holes through the workbench.
Place band saw on the workbench aligning holes in the
saw base with the holes drilled in the workbench.
Insert bolts (not included) and tighten securely with lock
washers and hex nuts (not included).
NOTE:
All bolts should be inserted from the top. Install
the lock washers and hex nuts from the underside of the
bench.
Supporting surface where band saw is mounted should be
examined carefully after mounting to insure that no move-
ment during use can result. If any tipping or walking is noted,
secure workbench or support surface before beginning
cutting operation.
CLAMPING BAND SAW TO WORKBENCH
See Figure 5.
If the band saw is to be used as a portable tool, it is recom-
mended that you fasten it permanently to a mounting board
that can easily be clamped to a workbench or other supporting
surface. The mounting board should be of sufficient size to
avoid tipping of saw while in use. Any good grade plywood
or chipboard with a 3/4 in. thickness is recommended.
Mount saw to board using holes in saw base as a template
for hole pattern. Locate and mark the holes where the
band saw is to be mounted.
Follow the last three steps in the section
Mounting Band
Saw to Workbench,
shown above.
If lag bolts are used, make sure they are long enough to
Содержание BS902
Страница 25: ...25 NOTES ...