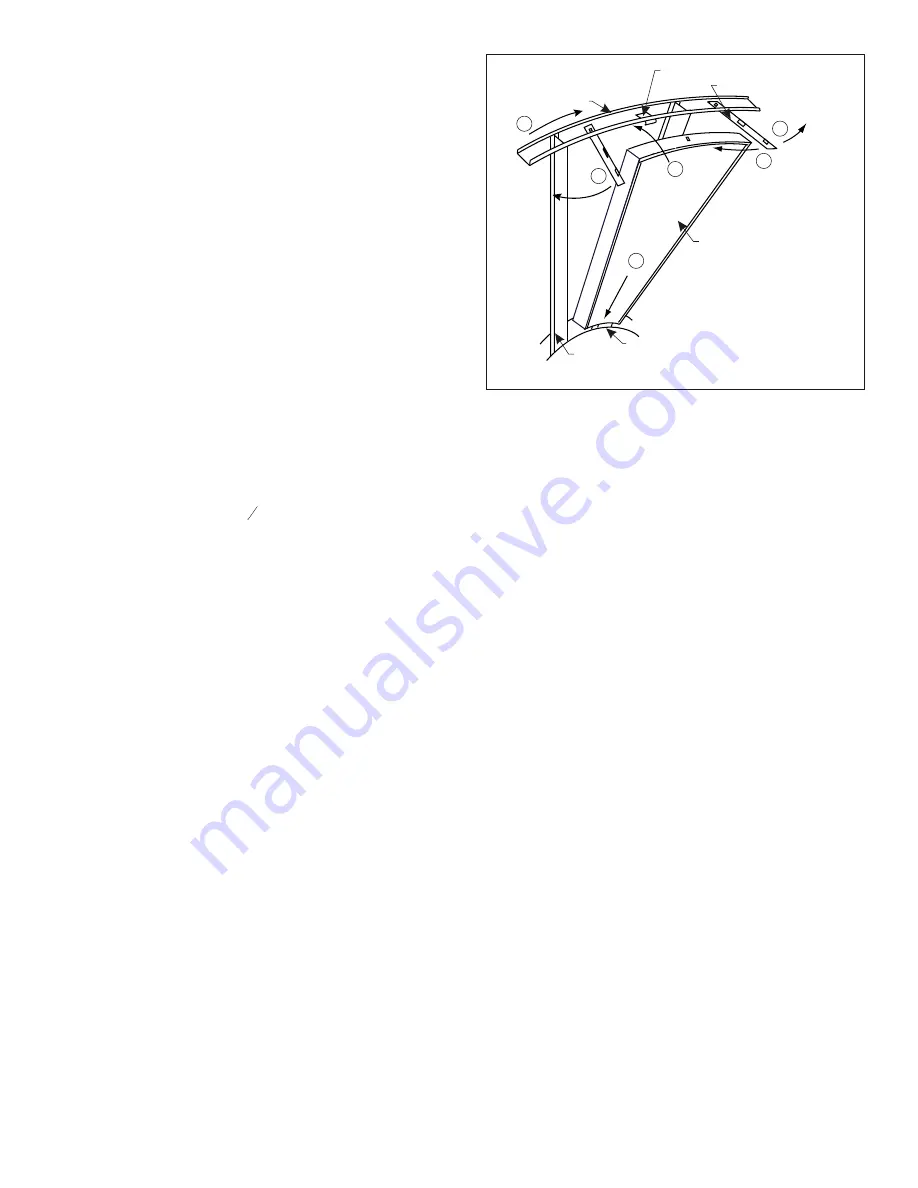
X - MAIN TE NANCE
Motor Maintenance
All motors use prelubricated sealed bearings; no further
lubrication is necessary.
Mechanical Inspection
Make visual inspection of dampers, linkage assemblies
and ERV rotating bearings during routine maintenance.
Filters should be checked periodically and cleaned when
necessary. Filter is located in fresh air hoods.
DO NOT
replace permanent filters with throwaway type filters.
Belt Alignment
Proper alignment is essential to maintain long V-Belt life.
Belt alignment should be checked every time belt
maintenance is performed, each time the belt is replaced,
and whenever sheaves are removed or installed.
Belt Installation
Always move the drive unit forward so the belt can be
easily slipped into the groove without forcing them. Never
force the belt into a sheave with a screw driver or wedge.
You will damage the fabric and break the cords. It is
recommended that the pulley center distances be offset by
¾" for proper length. This will allow the motor assembly to
slide forward to remove belt and backward for belt tension.
Belt Tension
Measure the span length (center distance between pulleys
when belt is snug). Mark center of span, then apply a force
(6 to 9 Lbs on new belts) perpendicular to the span large
enough to deflect the belt
1
64
"
for every inch in span length.
Energy Recovery Wheel Maintenance
Eight pie-shaped ERW segments, are seated on stops
between the segment retainer which pivots on the wheel
rim and secured to the hub and rim of wheel. Annual
inspection of the self cleaning wheel is recommended.
With power disconnected, remove ERV access panels
(rear) and unplug [J150 and P150]
(Refer to wiring
diagrams in this instruction manual).
Remove segment
and wash with water and/or mild detergent.
To install wheel segments follow steps A through E .
See
Figure 5.
Reverse procedure for segment removal.
A. Unlock two segment retainers (one on each side of the
selected segment opening.
B. With the embedded stiffener facing the motor side,
insert the nose of the segment between the hub plates.
C. Holding segment by the two outer corners, press the
segment towards the center of the wheel and inwards
against the spoke flanges. If hand pressure does not
fully seat the segment, insert the flat tip of a screw
driver between the wheel rim and outer corners of the
segment and apply downward force while guiding the
segment into place.
D. Close and latch each segment retainer under segment
retaining catch.
E. Slowly ro
tate the wheel 180
o
. In
stall the sec
ond
seg ment op po site the first for coun ter bal ance. Ro tate
the two in stalled seg ment 90
o
to bal ance the wheel
while the third seg ment is in stalled. Ro tate the wheel
180
o
again to in stall the fourth seg ment. Re peat this
se quence with the re main ing four segments.
PAGE 5
B
C
A
D
E
D
HUB
SEGMENT
SPOKE
SEGMENT RETAINER CATCH
WHEEL RIM
SEGMENT RETAINER
Figure 5
XI - WAR RANTY
RSI Manu fac tured Parts
In the event that defects in workmanship or materials
originate in any part manufactured by RSI, FOB point of
manufactured, we guarantee to repair or replace that part,
within three (3) months of the shipment date.
Other Sup plied Parts
Additionally, RSI guarantees to replace standard
components purchased new from a RSI vendor, (motors,
controls, etc.) that may be found defective, within twelve
(12) months of the installation date. The components
warranty, however, excludes service call charges and
labor cost for replacing or adjusting the defective part.
Limi ta tion of War ran ties
Misapplication, destruction, negligence or alteration
constitute the warranty and/or the components warranty of
RSI products and/or parts, null and void. This warranty is
provided in lieu of all other written, stated or implied
warranties.
Содержание RRS Rooftop Systems P28 Series
Страница 9: ...PAGE 9...
Страница 10: ...PAGE 10 PLATFORM SUPPORT RAIL TOP FILLER PANEL SIDE FILLER PANEL...