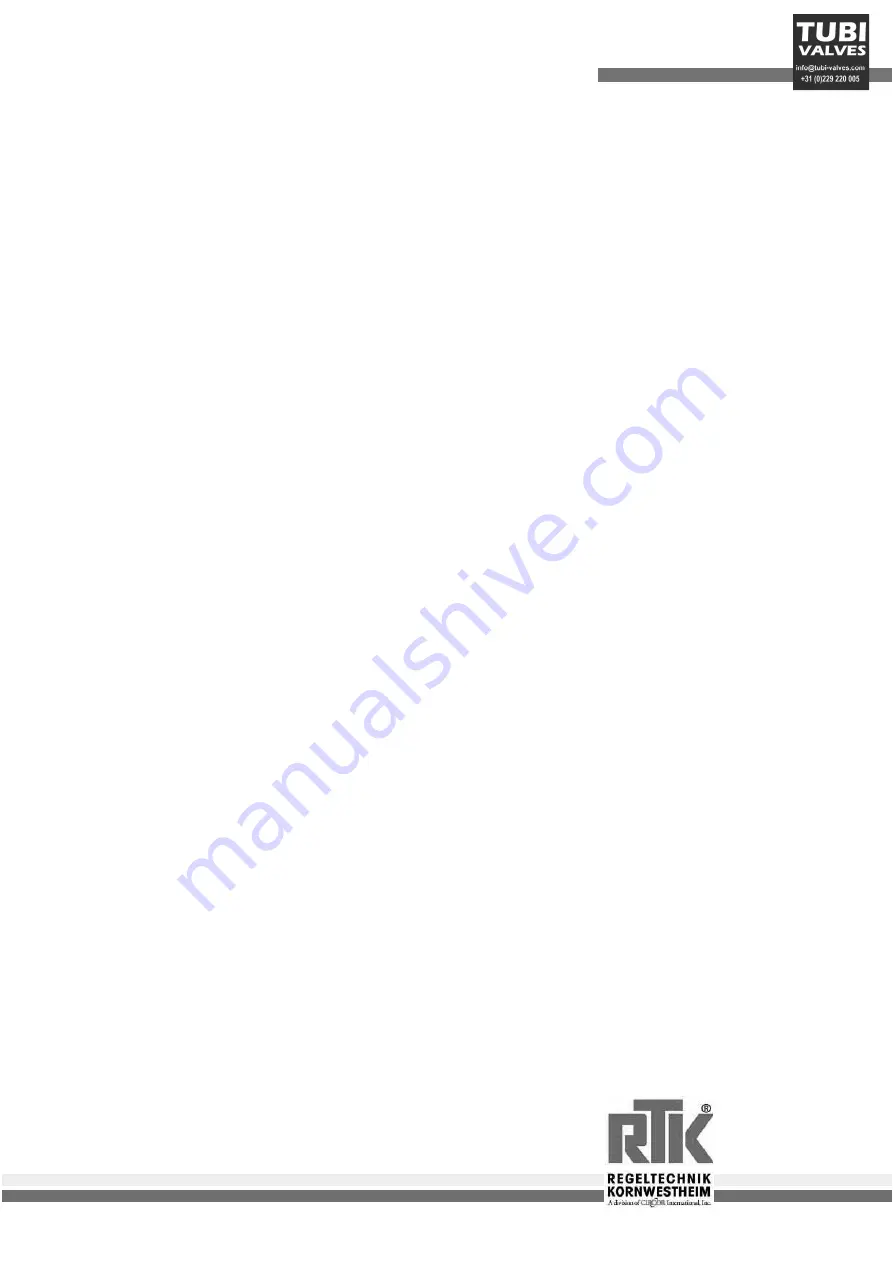
3050-8010
Einbau- und Betriebsanleitung
Installation and Operating instructions
Instructions de montage et de service
Regeltechnik Kornwestheim
GmbH
Max-Planck Straße 3
D-70806 Kornwestheim
T49 7154 / 13 14 - 0
T49 7154 / 13 14 - 31
Internet www.rtk.de
E-Mail [email protected]
- 41 -
8
Empirical optimization
In the absence of system data optimization can be performed empirically with manual trials.
In the trials for empirical optimization the following points are to be considered:
•
It must be ensured that the controller output and the controlled variable never reach prohibited levels!!!
•
The conditions for the trials should always be identical in order to obtain comparable results.
•
The trial procedure must be aimed at the goal of optimization: response to set value changes or interference behavior.
•
The controller's operating point must be the same at the trials.
The control parameters are to be set as follows for initial operation:
•
Xp as large as possible: on the highest adjustable value,
•
Tv relatively large: at most the time needed for the controlled system until the reaction clearly begins.
•
Tn large: at most the time the controlled system needs until the reaction is complete.
The time needed for empirical optimization is considerable. To obtain a useful result in a relatively
short time, the following procedure is useful:
Ü
Tn=Tv=0 and Xp as high as possible (P-control). The Xp is reduced from trial to trial,
as long as the control is sufficiently stable. If it becomes too unstable, the Xp must be somewhat enlarged and
continue with
*
.
*
Measure remaining system deviation: If it is slight enough optimization has been
successfully
concluded
( P). If it is too large it is better to regulate the system with PD (set Tv relatively high and
continue with
Ö
).
Ö
Reduce
Xp from trial to trial until the control is sufficiently stable. If it becomes too
unstable, continue with
ä
.
ä
Reduce Tv and see whether the control can be sufficiently stabilized again.
If so, continue with
Ö
, if not enlarge Xp a little and continue with
#
.
#
Determine whether in procedures
Ö
and
ä
the
Xp
was considerably reduced. If so, continue
with
<
, if not, the system is better controlled with PI (set Tv at 0 and continue with
>
).
<
Measure remaining deviation. If it is slight enough, optimization has been
successfully
concluded
(
PD
). If it is too large it is better to regulate the route with PD (leave Xp and Tv unchanged and
continue with
>
).
>
Tn is set high and reduced from trial to trial, as long as the control is sufficiently stable.
If it becomes too unstable, enlarge Xp a little, and optimization has been
successfully concluded
(PID or PI).
Empirical optimization is considerably improved with a recording instrument (or the trend function of the engineering tools) for the
g
controlled variable (actual value X) is considerably improved in time used and quality, and the assessment of the
trial results is greatly simplified.
g
This procedure can be generalized only with reservations and does not result in significantly improved
behavior on all controlled systems.
Changes to the operating point (Y0), breakover point gap (Xsh)
g
lead to results which may be better or worse. With three-step controlllersTm
must be set for the actual running time of the connected positioning motor.