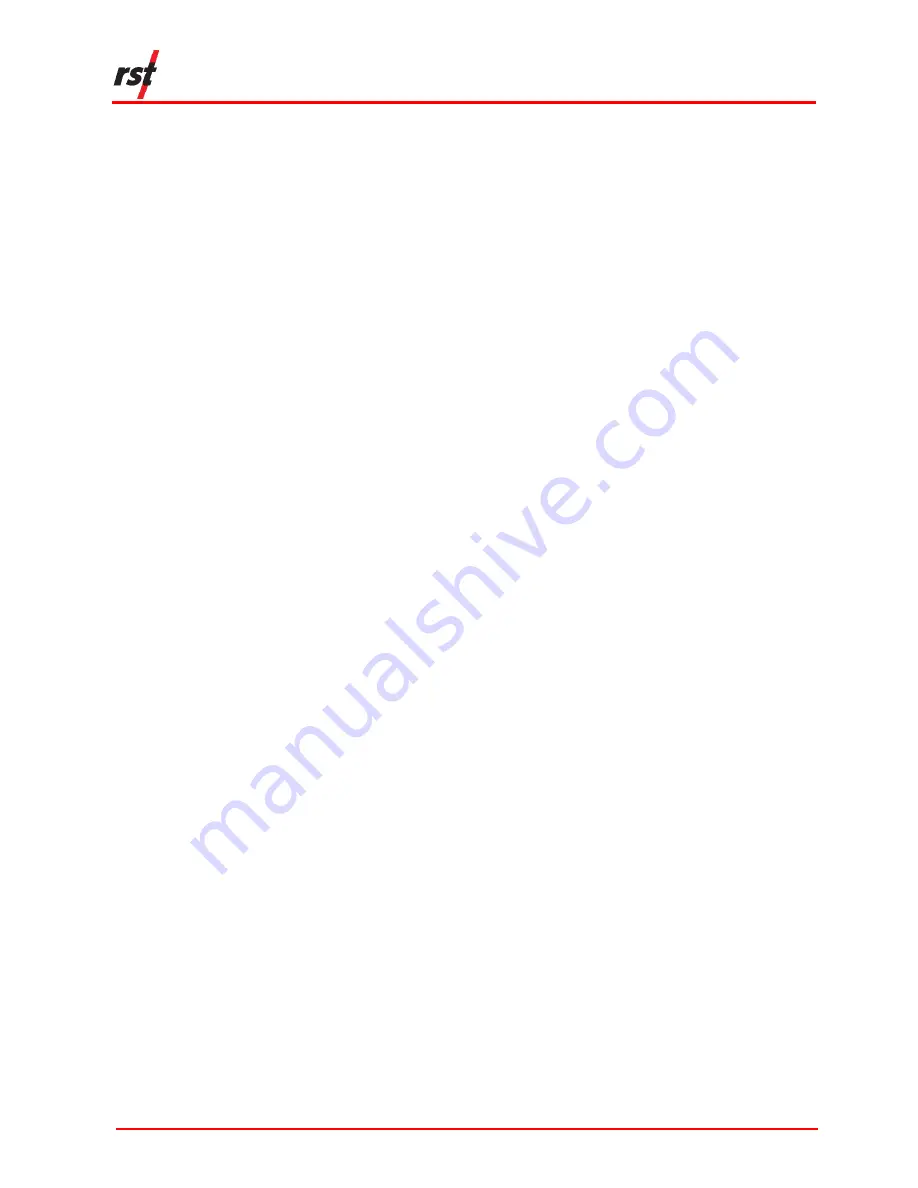
VW2100 Vibrating Wire Piezometer
RST Instruments Ltd.
Page 23
5.7
C
ABLE
I
DENTIFICATION
The vibrating wire cables are identified with a serial number tag that is attached to
the cable jacket at the readout end. If the cable must be cut, this VW serial number
tag must be removed and reattached at the new cable end. As an added
identification feature, the large cable rolls used in the manufacture of all RST
vibrating wire sensors have meterage numbers marked on the cable at every meter.
The start and end point of the numbering sequence is unique to each sensor and is
recorded on the instrument calibration sheet for later reference. Inspection of the
cable meterage numbers can therefore be easily used to verify the ID of an installed
vibrating wire sensor.
If the vibrating wire cable is cut and needs to be repaired, or the cable must be
lengthened with a cable splice, RST recommends the use of an RST ELSPLICE4
Electrical Cable Splice Kit for Vibrating Wire Cable. Any cable splice that will be
exposed to any moisture should be protected in this manner to eliminate the potential
of water egress, short circuiting, and conductor corrosion.
5.8
C
ABLE
R
OUTING
5.8.1
Transition from Vertical Borehole to Horizontal Trench
The vibrating wire cable should be routed along a curved path as it goes from a
vertical to a horizontal position. At the collar of the borehole, prepare a large radius
circular transition path within a cushion of screened sand/5% bentonite mix, hand
compacted to the surrounding fill density. Embed the cable along this transition
pathway and bury it in place to ensure the cable will not be stretched or kinked by
uneven loading.
5.8.2
Horizontal Cable Runs
Two methods are currently used to protect horizontal cable runs from damage. The
first method is embedment within selected materials on the surface of the fill. The
second method is embedment in an excavated trench in the fill. The second method
is the most commonly used because once the trench is backfilled and compacted,
the surface can be used for access. The trench method is discussed below. Refer to
Clements (1982) in Appendix F for a description of this method.
All surface cable installations require continuous surveillance and protection from
traffic and earth moving equipment which must move around on the fill surface.
Note that the trench dimensions should be 300 mm wider than the width required for
the cable layout and a minimum 600 mm deep. A 100-150 mm bedding layer of 1
mm minus sand is then placed along the trench bottom. Bentonite can be added to
the sand to form an impervious section or plug if required.
1
Cover cable completely with a 150 mm lift of 10 mm minus select material.
2
Completely backfill the trench with selected material. Compact it with light hand
operated equipment.