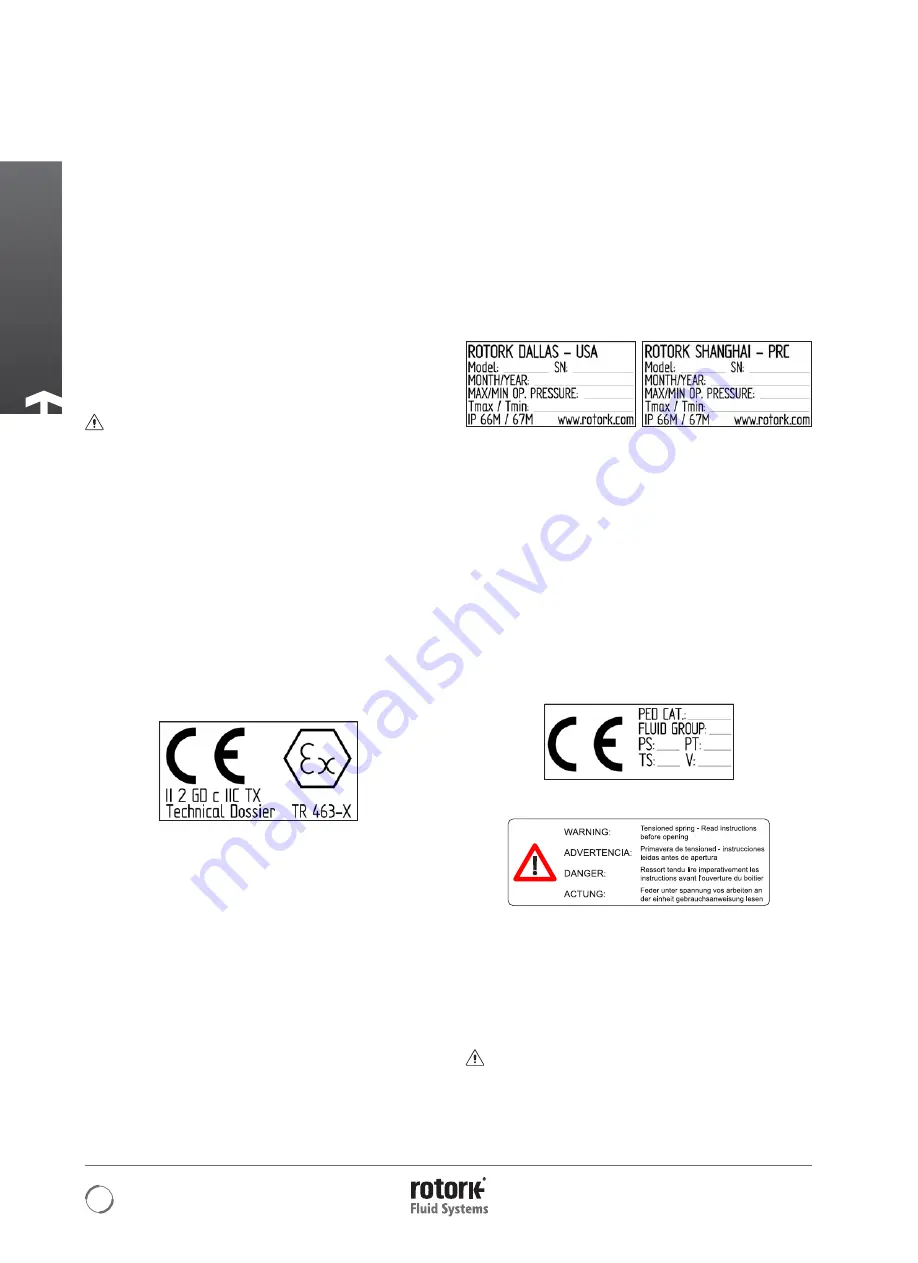
12
4
CHECKS TO BE CARRIED OUT UPON DELIVERY
4.1
Damages during transport
Check the packaging and the actuator for damages during
transport.
Remove the packaging, taking care that some of its
components (straps, nails, wood splinters, etc.) do not cause
injuries to the operator.
Once the packaging has been entirely removed, visually
inspect the actuator for damage.
If accessories are included in the provision, ensure that they
are compliant to those listed in the order and in the shipping
documents.
If the actuator is seriously damaged, do not try to
repair it or start it up. Please contact Rotork.
4.2
CE marking and nameplates
The actuator body is cast-embossed with the manufacturer’s
name and the model’s name. Each actuator is delivered with
a standard label.
For actuators delivered within the European Union, the CE
mark the product conformity with the essential applicable
health and safety requirements of the European Directives.
Supplementary nameplates are applied externally on the
centre body cover and displays the following data:
• CE conformity marking
• ATEX protection
• Name of technical file deposited with a certifying body
Figure 2: CE ATEX nameplate
Note:
The TX surface temperature class is not supplied
since the actuator has no internal heat source. Maximum
actuator temperature is near the environmental or exercise
fluid temperature, whichever is greater. Normal operating
temperature is approximately -20 °C to +80 °C. The precise
temperature range is specified within the project-specific
technical documentation. Special applications out of previous
range are available upon request.
The ATEX nameplate does not indicate the maximum
environmental and/or exercise fluid temperature; this
information is reported within the project-specific technical
documentation.
Contents of the standard nameplate:
• Name and address of the manufacturer
• Model type
• Serial number
• Month/year of manufacture
• Maximum/minimum operating pressure (bar)
• Maximum/minimum operative temperature (°C)
• IP protection class
Figure 3: KT-XX-DA/SR standard nameplate for units made in
USA and China
If CE (PED) marking is required, the following data is specified
on a third plate:
•
CE conformity marking
•
PED 97/23/CE category
• Fluid
•
Design pressure PS (bar)
•
Testing pressure PT (bar)
•
Design temperature TS (°C)
•
Volume (litres)
•
Certifying body number if applicable
Figure 4: KT-XX-DA/SR actuator PED nameplate
Figure 5: Spring housing warning nameplate
Please check if the data stamped on the plate coincide
with those specified on the Confirmation of Order, Test
Certificates and the Delivery Note.
Ensure that the product specification as noted on the
nameplate(s) is suitable for the application.
It is not allowed to remove or modify the
nameplate(s). The nameplate must be kept legible
at all times: it must be regularly cleaned. In case the
nameplate is damaged and illegible, a duplicate is to be
requested.
Checks To Be Carried Out Upon Delivery