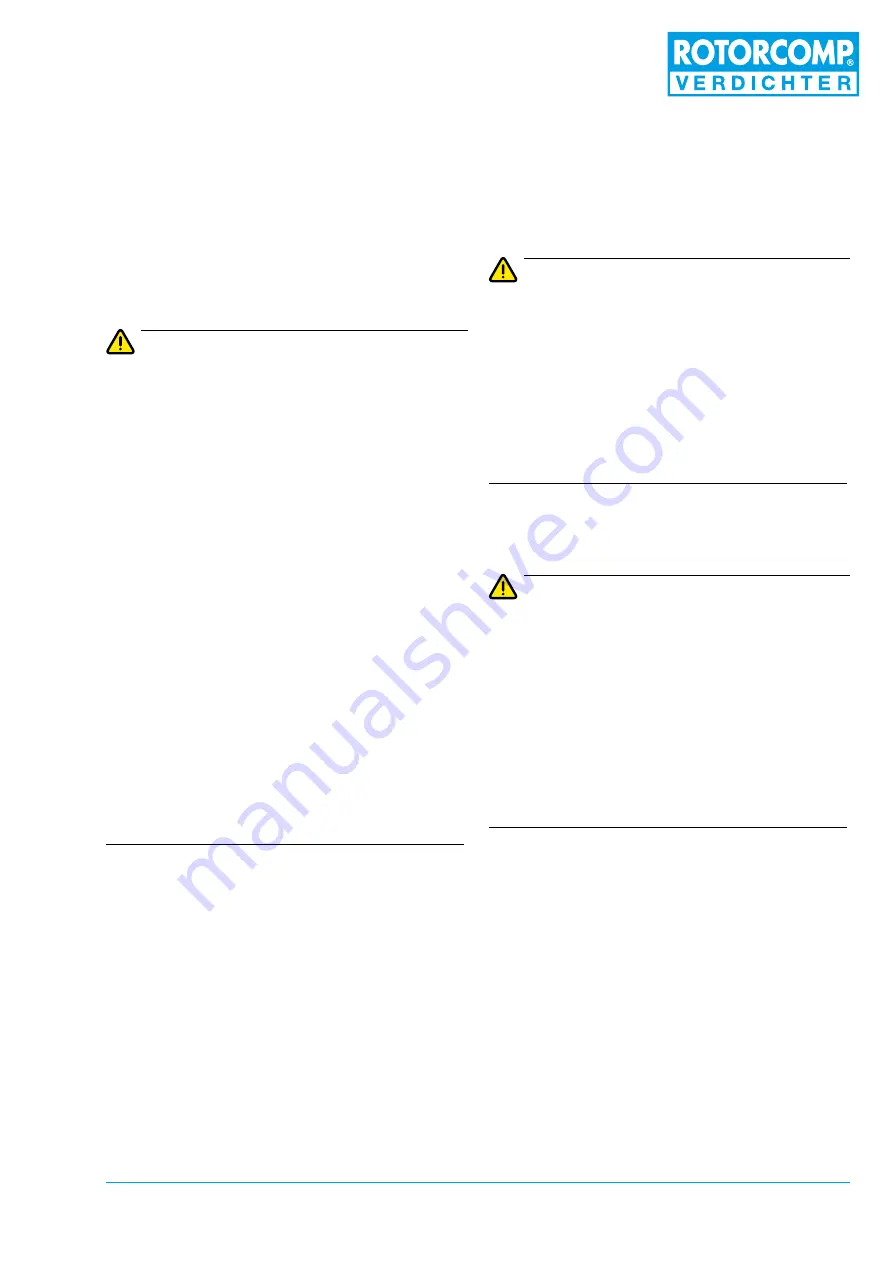
6.1
[en] 02/2014
Installation and operating manual - NK 31
6.1 Preparation for commissioning
The components of the screw compressor are
carefully checked and tested at the factory.
These tests ensure that the required perfor-
mance and checking data are complied with.
Nevertheless, the screw compressor system
should be observed during the initial operating
hours.
Attention
With regard to commissioning, the applicable
regulations of the specific country must be ob
-
served.
In Germany these include the Operating Safety
Ordinance.
The following points must be observed prior to
commissioning:
– Direction of rotation: be sure to observe (see
chapter
6.2
“Checking direction of rotation”).
– The max. final pressure specified on the name
-
plate may not be exceeded.
– Do not switch off screw compressor systems
running under load at the Emergency-Stop or
main switch.
– Check the oil level (see chapter
7.2
“Oil level”).
– Before each first commissioning and when re
-
commissioning after a longer shut-down of the
screw compressor compact module, always
carry out the activities described in chapter
6.4
“Recommissioning screw compressor system”.
– With a belt drive: Check the belt tension and
belt routing (see chapter
7
“Maintenance”).
– Check the position of the shut-off valve.
– Check all screw fitting and fastening screws for
firm seating.
6 Commissioning
6.2 Checking direction of rotation
Direction of rotation:
Standard model rotating to the left (counterclock-
wise) looking at the shaft.
Attention
The direction of rotation of the screw compres
-
sor must be checked during first commissioning
and each time changes are made to the electrical
supply line of the electric motor drive. For this
purpose, switch on the drive motor briefly and
then switch off again immediately.
An incorrect direction of rotation for more than
2 seconds will result in destruction in the screw
compressor. Reconnect the phases of the con-
nection cable if necessary.
6.3 Test run
Attention
The system is discharged extremely quickly
down to the opening pressure “minimum pres
-
sure valve” in the Stop mode, “with shut-off valve
opened”!
This can result in the oil in the separating tank
foaming up.
The possible consequences include:
– Oil escaping with the discharge air
– Oil flooding the fine separator cartridges
– Compressed air containing oil when restarting
the line
Therefore, the following points must be observed
during the test run:
– Only switch off the system with the shut-off
valve closed!
– If possible, connect the system to a com-
pressed-air reservoir!