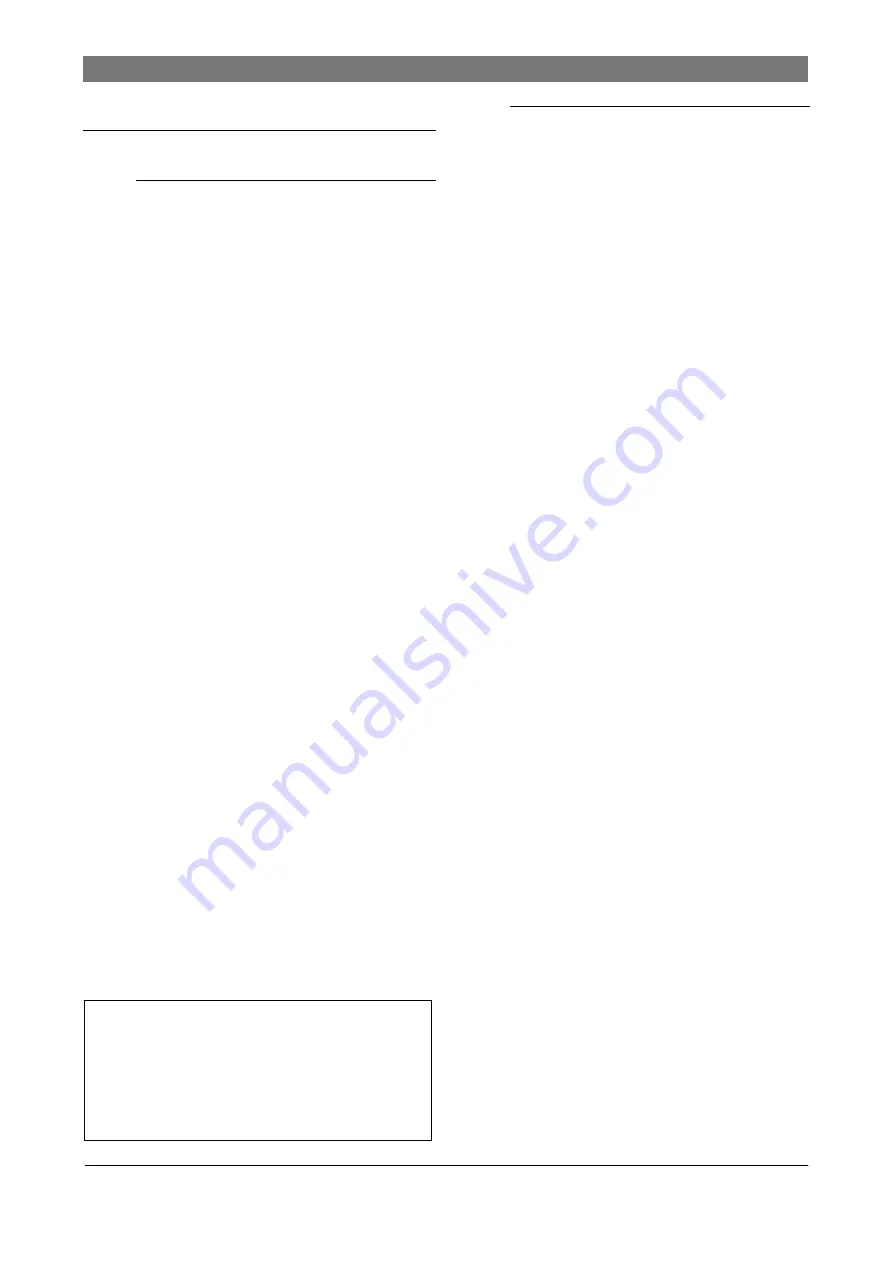
1.
Introduction
2
1.
Introduction
1.1 About this operating manual
The post lift conforms to state of the art technology
and complies with the applicable occupational
health & safety and accident prevention regulations.
Notwithstanding, improper use or use other than
that which is intended may result in a risk of fatal or
physical injury to the user or third parties and may
also result in damage to property.
It is therefore imperative that the relevant people
carefully read and understand this operating
manual.
Read the instructions carefully to prevent incorrect
use, potential hazards and damage. The post lift
should always be operated according to regulations.
Please note the following:
The operating manual must be kept close to the
lift and be easily accessible for all users.
Make sure that you have read and
understood Chapter 4, Safety Instructions
and also the operating instructions on the
machine.
We assume no liability for damage and
operational breakdowns which may occur as a
result of non-compliance with the instructions
contained within this operating manual.
Installation and commissioning of the lifts is
described in detail in Chapters 11 to 13.
Installation may only be carried out by
authorised installation specialists (trained by the
manufacturer) and qualified electricians.
If you should run into difficulties please contact a
specialist, our customer service.
Illustrations may differ from the supplied version
of the machine. Functions or processes to be
carried out remain the same.
1.2 Important information for the
machine operator
The operating manual contains important
information for safe operation and for the functional
reliability of the lift.
The signed form “Installation record“ must be
sent to the manufacturer to verify the installation
of the lift.
The “Inspection logbook“ contains forms for
verifying the initial, regular, and unscheduled
safety inspections. Use the forms to record the
inspections and add the completed forms to the
inspection logbook.
Design modifications must be entered in the
“Machine master data sheet“.
The machine operator is responsible for ensuring
that the lift is always operated in a safe manner and
the following requirements are met or regularly
carried out.
The operators must be qualified through specialist
training and experience.
The operator must be familiar with the
applicable occupational health & safety and
accident prevention regulations and be
instructed and trained to operate the lift.
The operator must have read and understood
the safety regulations chapter and verified this
with his signature.
If several people work on the post lift, a foreman
must be appointed.
The post lift may only be operated in technically
sound condition with regard to safety.
Maintenance and servicing must be performed
regularly according to the defined schedule.
Safety inspections must be conducted regularly,
and at least once annually in accordance with
chapter 9.
The inspection logbook must be kept up-to-date.
This operating manual as well as the annexed
instructions must always be kept with the lift.
This also applies if the lift is sold or re-installed
at a new location.
For safety reasons, unauthorised modifications
or alterations to the lift are not permitted. In case
of an unauthorised modification, the operating
permit is cancelled, and the Declaration of
Conformity becomes null and void.
Disclaimer:
We assume no responsibility for printing errors,
mistakes and technical changes.
The brands and trade marks mentioned in this
document refer to their owners or the products
thereof.
Содержание SGL35M
Страница 2: ......
Страница 15: ...5 Operation 13 3 Drive the vehicle away from the lift 5 9 Switch off the system 1 Set the main switch to 0...
Страница 39: ...Diagrams spare parts lists 37 Electrical Circuit Diagram single phase...
Страница 40: ...Diagrams spare parts lists 38 Electrical Circuit Diagram 3 phase...
Страница 42: ...40...
Страница 44: ...Diagrams spare parts lists 42 8 9 2 3 5 4 15 1 14 17 7 18 6 16 11 12 10 26 13 11...
Страница 45: ...Figure 2 43...
Страница 46: ...Diagrams spare parts lists Figure 3 Figure 4 44...
Страница 47: ...Figure 5 Figure 7 Figure 6 45 54 57 56 55...
Страница 48: ...Diagrams spare parts lists 46 Figure 8...
Страница 49: ...Figure 9 47...
Страница 50: ...Diagrams spare parts lists 48...