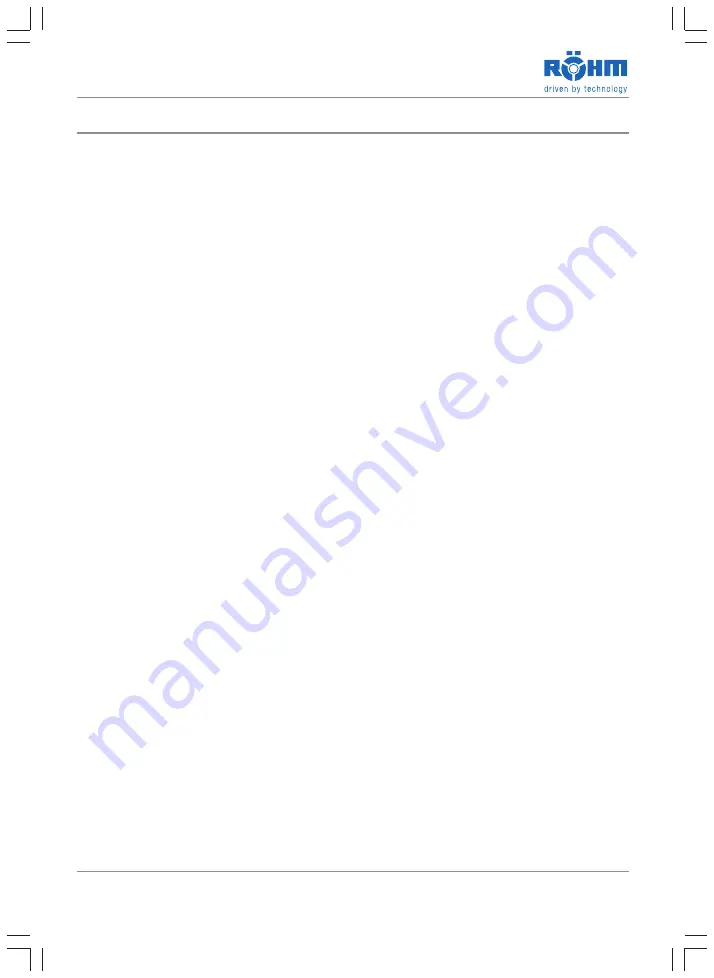
1 | About this Operating Manual
6 / 43
KZS-P_KZS-PG
1.3
Warranty and Liability
All information and instructions in this operating manual are given in good
faith on the basis of our experience and knowledge to date. The products of
RÖHM GmbH are subject to constant further development. The manufacturer
therefore reserves the right to make any modifications and improvements
deemed useful. However, there is no obligation to extend these modifications
and extensions to any previously delivered centric clamps. The centric clamp
is constructed exclusively for the purpose specified under “Intended Use”. Any
use beyond this is deemed to be inappropriate. RÖHM GmbH is not liable for
damage resulting from such use. The risk is borne solely by the owner.
Product liability for consequential damage of any type is excluded for damage
and operational interruptions resulting from operating errors, failure to ob-
serve this operating manual or incorrect maintenance by unauthorised person-
nel.
RÖHM GmbH expressly points out that replacement and wear parts supplied
by the manufacturer must be authorised by RÖHM GmbH. The company
RÖHM GmbH does not accept liability for unauthorised replacement and wear
parts. This applies to both product liability for consequential damage of all
types and to liability for damage to property.
All unauthorised conversions, modifications to the centric clamp and/or
changes in conditions are not permitted for safety reasons and exclude all li-
ability of RÖHM GmbH for any damage which may result. If modifications to
the centric clamp are necessary or the area of use differs from the intended
use, this must be agreed with the express permission of RÖHM GmbH.
The statutory and contractually agreed terms and conditions apply.
The following damage or defects are excluded from the warranty:
▪ caused by the operator due to non-compliance with the written instruc-
tions of the manufacturer with regard to
◦ commissioning (e.g. incorrect construction and assembly work),
◦ operation and
◦ maintenance of the equipment (insofar as this maintenance has not been
contractually taken over by the manufacturer);
▪ caused by technical operating conditions unknown to the manufacturer
(e.g. chemical or electrolytic influences) and/or machine specifications;
▪ caused by natural wear;
▪ caused by force majeure;
▪ caused by incorrect operation of all types or by incorrect use or operation
of the centric clamp. This also includes loading beyond the specified load
limits (e.g. speed, pressure, force etc.).
Содержание KZS-P
Страница 2: ......