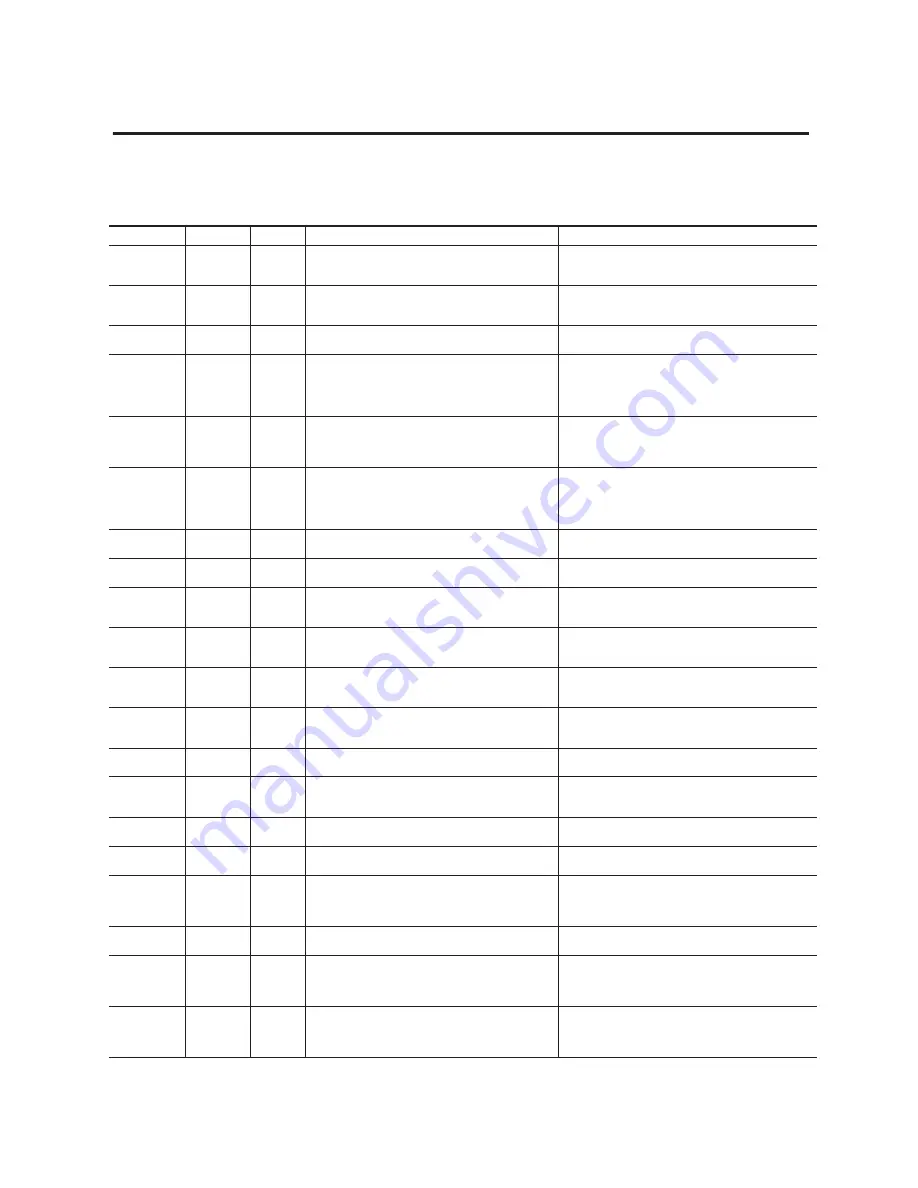
14
SMC™ Flex Quick Start
Troubleshooting - Abbreviated Listing
For a complete list of fault codes and troubleshooting tips, refer to the SMC Flex User Manual.
Display Fault Fault Code
Enabled
Possible Causes
Possible Solutions
Line Fault with
Phase Indication
1, 2, 3
prestart
only
Missing supply phase
Motor not connected properly
Incoming 3-phase voltage instability
Check for open line (i.e., blown fuse)
Check for open load lead
Verify power quality
Shorted SCR
with Phase
indication
4, 5, 6
all
Shorted power module
Check for shorted SCR, replace power module if necessary
Open Gate with
Phase Indication
7, 8, 9
start or
stop
Open gate circuitry
Loose gate lead
Perform resistance check; replace power module if necessary
Check gate lead connections to the control module
PTC Power Pole
and SCR
Overtemp
10, 11
Controller ventilation blocked
Controller duty cycle exceeded
Fan failure
Ambient temperature limit exceeded
Failed thermistor
Check for proper ventilation
Check application duty cycle
Wait for motor to cool or provide external cooling
Replace power module or control module as needed
Replace fan
Motor PTC
12
running
Motor ventilation blocked
Motor duty cycle exceeded
PTC open or shorted
Check for proper ventilation
Check application duty cycle
Wait for motor to cool or provide external cooling
Check resistance of PTC
Open Bypass
with phase
indication
13, 14, 15
running
Control voltage is low
Inoperable power module bypass
Check control voltage power supply
Replace power module
Check control module TB2…TB4 and TB5…TB7 for securness
Check Aux 1, 2, 3, 4 configurations are not set to External
Bypass
No Load Fault
16, 17, 18, 40
prestart
only
Loss of load side power wiring
Start command cycled unexpectedly with motor rotating
Check all load side power connections
Check motor windings
Line Unbalance
19
running
Supply unbalance is greater than the user-programmed value
The delay time is too short for the application
Check power system and correct if necessary
Extend the delay time to match the application requirements
Overvoltage
20
running
Supply voltage is greater than user programmed value
The delay time is too short for the application
Check power system and correct if necessary
Correct the user-programmed value
Extend the delay time to match the application requirements
Undervoltage
21
running
Supply voltage is less than user programmed value
The delay time is too short for the application
Check power system and correct if necessary
Correct the user-programmed value
Extend the delay time to match the application requirements
Overload
22
running
Motor overloaded
Overload parameters are not matched to the motor
Check motor overload condition
Check values for overload class and motor FLC
Verify current draw of the motor
Underload
23
running
Broken motor shaft, belts, toolbits, etc..
Pump cavitation
Incorrect user setting
Check pump system, machine drive components, and loading
Check settings
Repair or replace motor
Jam
24
running
Motor current has exceeded the user programmed jam level
Correct source of jam or excessive loading
Check programmed time value
Stall
25
running
Motor did not reach full speed by the end of the programmed
ramp time
Incorrect user setting
Correct source of stall or excessive loading
Adjust SMC starting parameters to compensate for load
Phase Reversal
26
prestart
only
Incoming supply voltage is not in the expected ABC sequence
Check power wiring, correct if necessary
Network and
Comm's Loss
30, 31, 32
27, 28, 29
all
DPI network loss
Communication disconnection at the serial port
Check communication adapters and verify connection to SMC
Reconnect each DPI connected device
Ground Fault
33
running
Ground fault current level has exceeded programmed value
The delay time is too short for the application
Check power system and motor; correct if necessary
Check programmed ground fault levels to match application
requirements
Extend the delay time to match the application requirements
Power Loss with
phase indication
35, 36, 37
start or
stop
Missing supply phase (as indicated)
Internal CT problem
Check for open line (i.e., blown line fuse)
Replace power pole as indicated
Line Loss with
phase indication
41, 42, 43
start or
stop
Incoming 3-phase voltage instability or distortion
High impedance connection
Check supply voltage for capability to start/stop motor
Check for loose connections on line side or motor side of
power wires
Verify and correct input power quality
Internal 24V and
System Faults
44, 45, 46,
128…209
all
Low line condition
Excessive load on
Check the control power, verify it is within the specification
Check connections and grounding to the SMC control
terminals
Replace control module