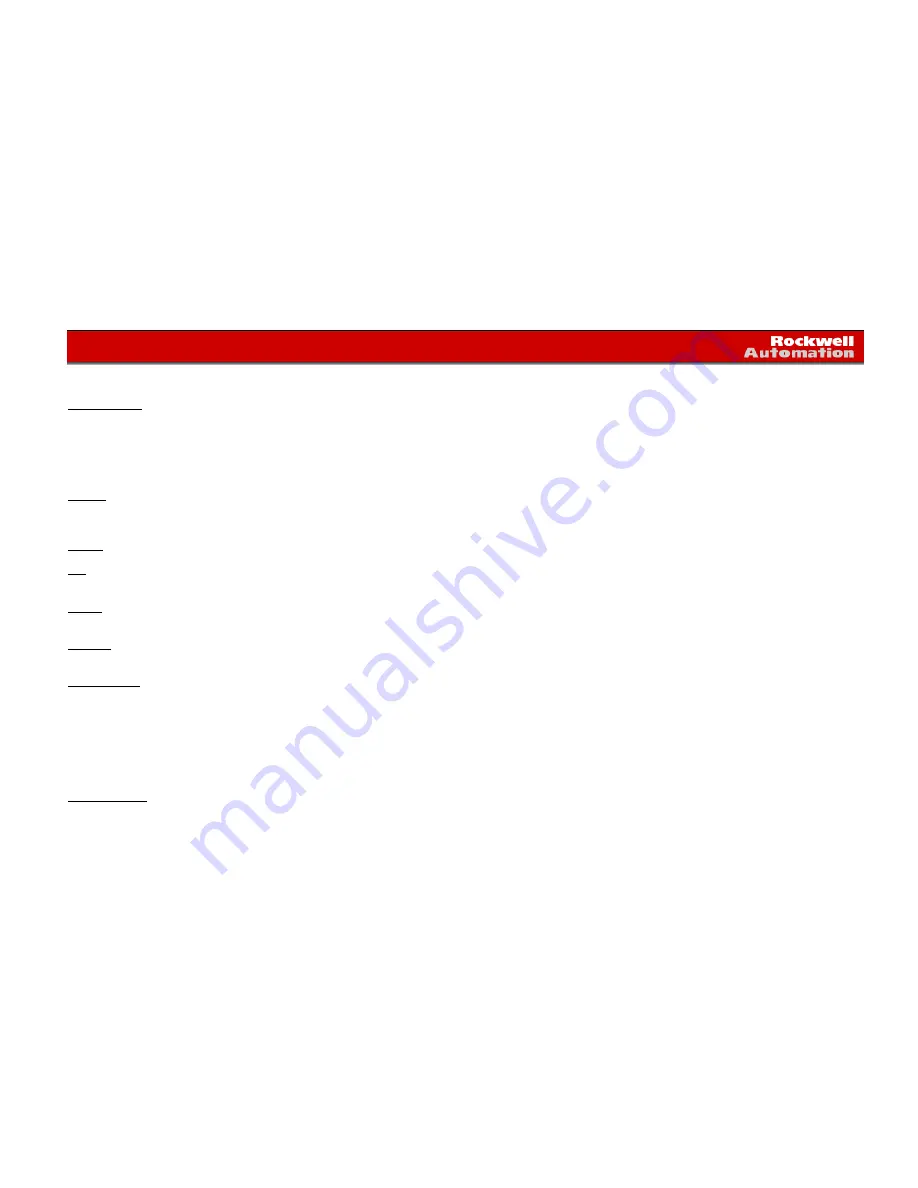
Maintenance Schedule, Cont’d
Vacuum Contactors - Contacts of vacuum contactors are not visible, so contact wear must be checked indirectly. Vacuum bottles should be replaced when:
1. The estimated number of operations equals one million, or
2. The contact life line indicator shows need for replacement, or
3. The vacuum bottle integrity tests show need for replacement. Replace all vacuum bottles in the contactor at the same time to avoid misalignment and uneven contact wear. If the vacuum battles do not require
replacement, check and adjust overtravel to the value listed on the maintenance instructions.
Terminals - Loose connections in power circuits can cause overheating that can lead to equipment malfunction or failure. Loose connections in control circuits can cause control malfunctions. Loose bonding or
grounding connections can Increase hazards of electrical shock and contribute to electromagnetic interference (EMI). Check the tightness of all terminals and bus bar connections and tighten securely any loose
connections. Replace any parts or wiring damaged by overheating, and any broken wires or bonding straps.
Arc Hood - Check for cracks, breaks, or deep erosion. Arc hoods and arc chutes should be replaced if damaged or deeply eroded.
Coils - If a cog exhibits evidence of overheating (cracked, melted or burned insulation), it must be replaced. In that event, check for and correct overvoltage or undervoltage conditions, which can cause coil
failure. Be sure to dean any residues of melted coil insulation from other parts of the device or replace such parts.
Batteries - Replace batteries periodically as specified in product manual or if a battery shows signs of electrolyte leakage. Use tools to handle batteries that have leaked electrolyte; most electrolytes are corrosive
and can cause burns. Dispose of the old battery in accordance with instructions supplied with the new battery or as specified In the manual for the product.
Pilot Lights - Replace any burned out lamps or damaged lenses. Photoelectric Switches-The lenses of photoelectric switches require periodic cleaning with a soft dry cloth. Reflective devices used in conjunction
with photoelectric switches also require periodic cleaning. Do not use solvents or cleaning agents on the lenses or reflectors. Replace any damaged lenses and reflectors.
Solid State Devices
-ATTENTION: Use of other than factory recommended test equipment for solid state controls may result in damage to the control or test equipment or unintended actuation of the controlled equipment. Refer to
paragraph titled HIGH VOLTAGE TESTING.
Solid state devices require little more than a periodic visual inspection. Discolored, charred or burned components may indicate the need to replace the component or circuit board. Necessary replacements should
be made only at the PC board or plug-in component level. Printed circuit boards should be inspected to determine whether they are properly seated in the edge board connectors. Board locking tabs should also be
in place. Solid state devices must also be protected from contamination, and cooling provisions must be maintained - refer to paragraphs titled CONTAMINATION and COOLING DEVICES. Solvents should not be used
on printed circuit boards.
High Voltage Testing - High voltage insulation resistance (IR) and dielectric withstanding voltage (DWV) tests should not be used to check solid state control equipment. When measuring IR or DWV of electrical
equipment such as transformers or motors, a solid state device used for control or monitoring must be disconnected before performing the test. Even though no damage is readily apparent after an IR or DWV test,
the solid state devices are degraded and repeated application of high voltage can lead to failure.