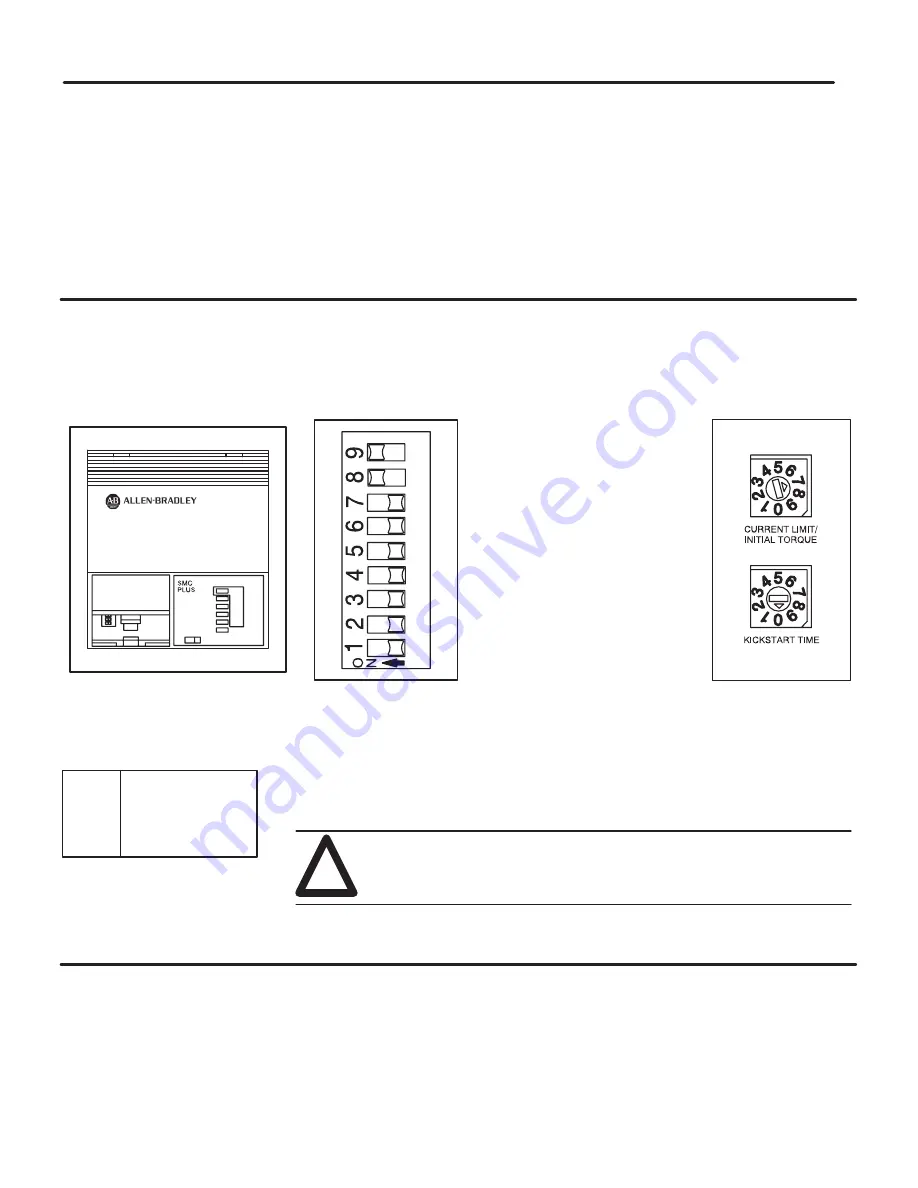
Chapter
Set-up Procedures: SMP PLUS
Controller without Options
3
3-3
During the “Starting” and “Running” modes, the controller’s microcomputer
monitors the following conditions. If any of the conditions exist, the controller
shuts down, changes state of the auxiliary contacts, and turns on the FAULT LED
and the appropriate LED.
•
Start Fault
•
Temperature Fault
•
Line Fault
•
Stalled Motor
Once tripped, the controller cannot be restarted until control voltage is cycled. To
reset the controller, remove control power and reapply. (Refer to Page 3-1,
Protective Features, for additional details.)
After the controller has been installed, further set-up may be necessary. This set-up
is accomplished through DIP and rotary digital switches located on the front of the
controller. See Figure 3.3 below.
Figure 3.3 - Switch Access Door and Factory Switch Settings (Without
Options)
Not Used
Not Used
Auxiliary Contact Select Up to
Speed/Normal
Current Limit /Soft Start Select
Energy Saver Select (On/Off)
Starting Time*
Starting Time*
Starting Time*
Stall Trip Select (On/Off)
*NOTE:
The time it takes for the motor to come up to speed may be less than the
start time setting and will vary depending on the frictional and inertial
characteristics of the system.
If the factory settings are not suitable for the specific application, Figures 3.5, 3.7,
and 3.8 which follow, describe how to set the standard unit for Soft Start with
Kickstart, Current Limit and Full Voltage Starting. Refer to the publications listed
in Figure 3.3.1 for instructions on how to set controller with options.
WARNING:
Disconnect power before opening access door.
!
Use a small screwdriver to pry open the access door. Set the switches to meet
application requirements.
This starting method has the most general application. The motor voltage is raised
to an initial torque value. This is adjustable between 5 and 90% of locked rotor
torque. The motor voltage is gradually increased during the ramp period, which can
be adjusted from 2 to 30 seconds. These customer settings should be set for the
best starting performance over the required load range.
A kickstart or boost can be provided. This is intended to provide a current pulse of
500% of full load current and is adjustable from 0.4 to 2 seconds. This will allow
the motor to develop additional torque at start.
Fault Trips
Customer Settings
Figure 3.3.1 Publications
150-805
150-806
150-807
150-808
150-809
150-810
Soft Stop
Pump Control
Preset Slow Speed
Smart Motor Brkg.
Accu-Stop
Slow Speed w/Brkg.
Soft Start
Soft Start with
Kickstart
Содержание Allen-Bradley SMC-PLUS Bulletin 150
Страница 2: ......