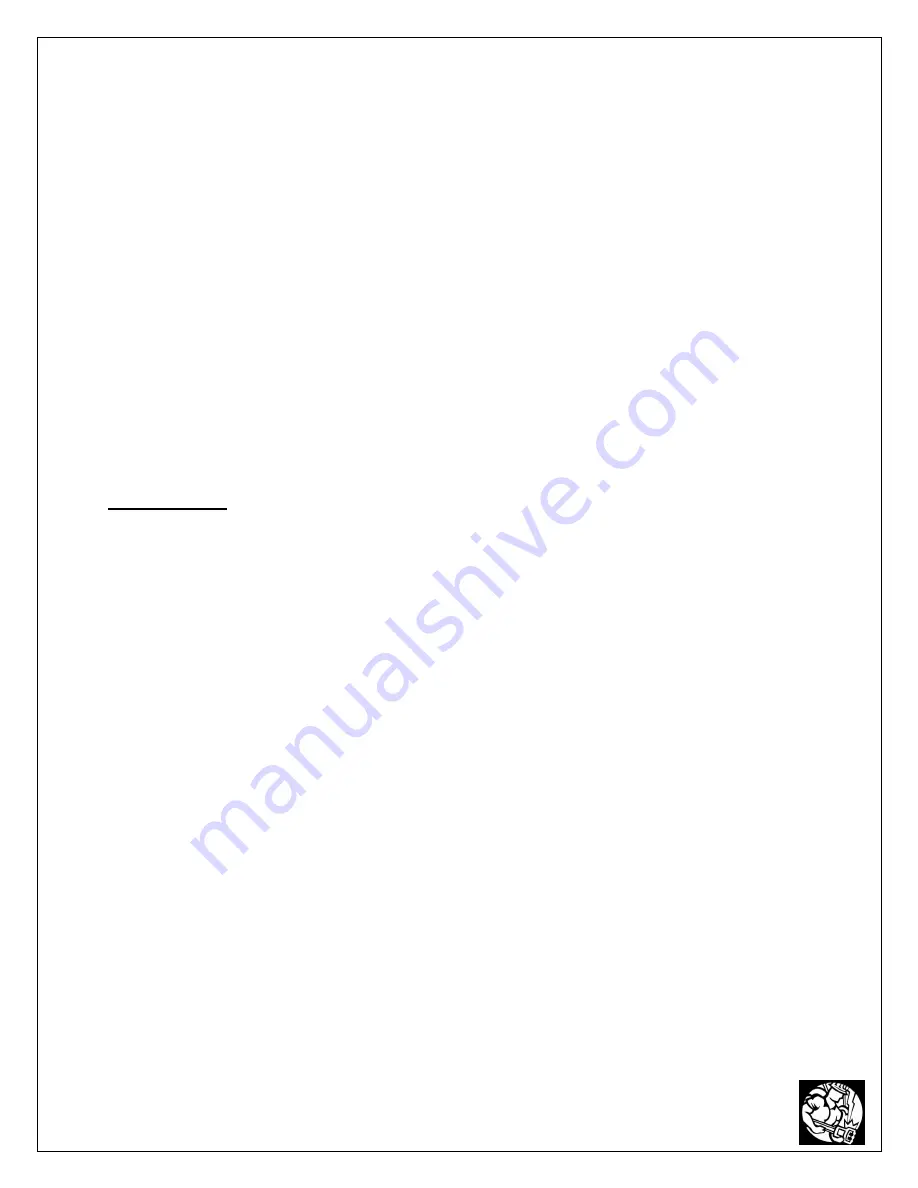
Copyright 2021. All rights reserved by Rockmore International.
3
3.2 – Contamination
Contamination is another common cause of DTH hammer and bit failures. Be sure to keep all
connections covered and clean at all times. It is a good idea when connecting a hammer to a drill string
to cover the connection to the hammer and blow high-pressure air and water through the drill string for
several seconds to remove any loose scale, rust or other foreign materials. When installing a bit in the
hammer, take care to remove any cuttings or foreign material from the bit shank.
3.3 – Corrosion
Corrosion is another common cause of DTH hammer and bit failures. Corrosion is the deterioration of a
material due to a reaction with its environment. The best preventative action against corrosion is to keep
the DTH hammer well lubricated with rock drill oil. In addition, when finished drilling with foam/polymers,
it is necessary to rinse all drilling tools with fresh clean water and lubricate them properly. Prolonged
exposure to the atmosphere creates a corrosive reaction between the steel and the foam.
The most detrimental type of corrosion encountered in DTH hammers is oxidation cavitation (finite
notches in the material surfaces). The easiest areas for this condition to exist are in the non-moving
areas of the hammer. For example, thread roots and O-ring grooves are common places to find oxidation
cavitation.
4. SERVICING:
4.1 – Disassembly
The ROK LT hammers use right–hand threads.
Use tools appropriate for removing the Driver Sub and the Top Sub from the Wear Sleeve of the ROK LT
hammer. There are wrench flats on both the Top Sub and the Driver Sub for assembly and disassembly.
Do not apply heat to the hammer. Do not hit the hammer or apply excessive force with improper tools as
this could initiate cracks, reduce operating life, and most importantly would void any warranty.
4.2 – Routine Inspection
Regularly inspect all parts carefully for any signs of damage – galling, cracks, corrosion. Any sharp
edges should be removed from the Piston striking face using emery paper or files. In cases of severe
galling or cracking, we strongly recommend replacing the Piston to avoid further damage to the hammer.
Galling and cracking can be signs of poor lubrication techniques or contamination. Please refer back to
sections 3.1 and 3.2 on lubrication and contamination.
The amount of wear on all major components (Wear Sleeve, Piston, Air Guide, and Top Sub) should be
regularly inspected and checked. The minimum diameter difference between the Wear Sleeve and bit
should be no less than 8mm or 0.3 inches.
4.3 – Assembly
Remove and polish all galling and burrs with emery paper. Particularly during the replacement of broken
components, extra care must be taken to be certain that the mating surfaces were not damaged.
Carefully lubricate all internal hammer parts again with rock drill oil and coat threads with thread grease
prior to reassembly. Use a soft-headed hammer tool to carefully tap components together to ensure
proper alignment. Never use excessive force.