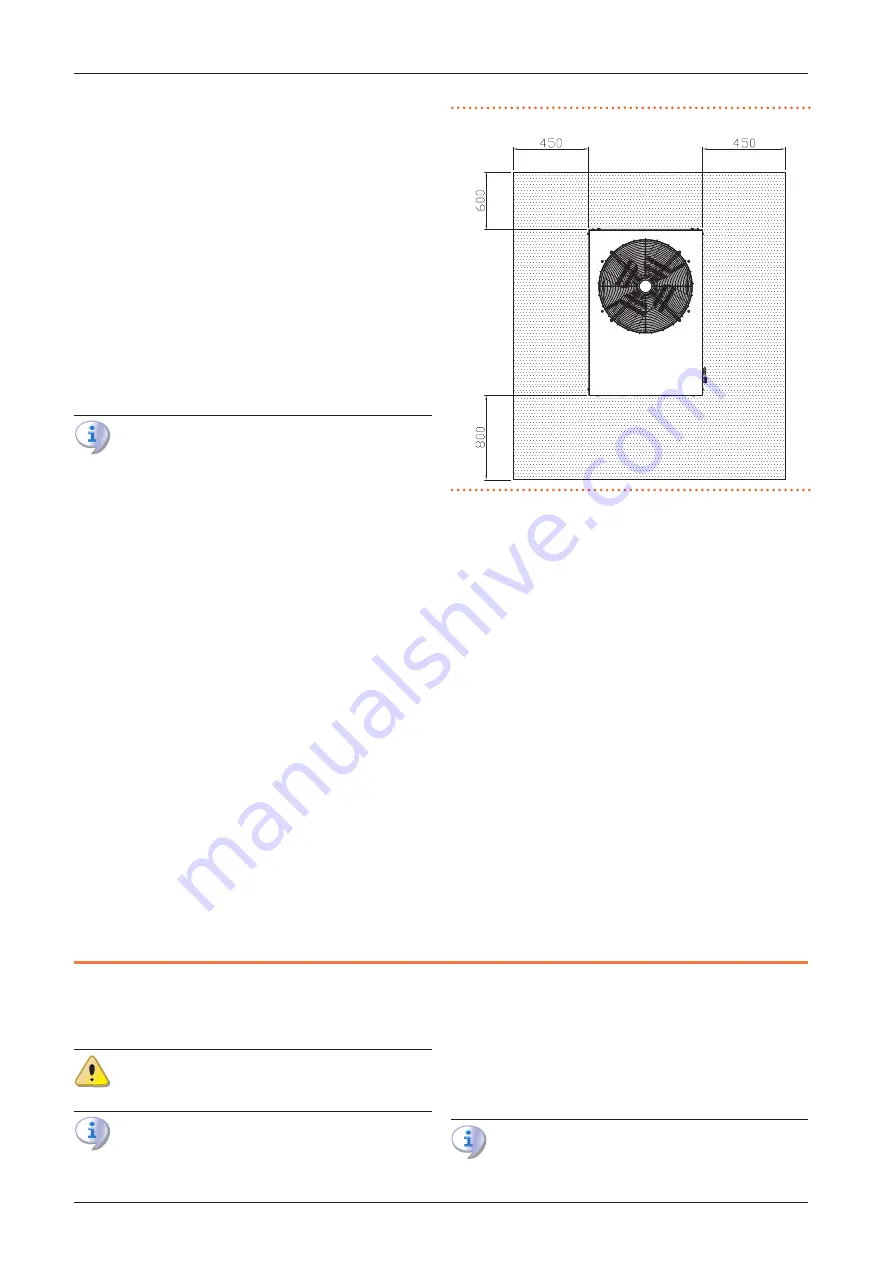
Heating engineer
Installation, use and maintenance manual – GAHP A
19
3
Where to install the appliance
▶
The appliance may be installed at ground level, on a terrace
or on a roof, compatibly with its dimensions and weight.
▶
It must be installed outside buildings, in an area of natural air
circulation, outside the dripping path of drainpipes or simi-
lar. It does not require protection from weathering.
▶
No obstruction or overhanging structure (e.g. protruding
roofs, canopies, balconies, ledges, trees) shall interfere either
with the air flowing from the top of the appliance or with the
exhaust flue gas.
▶
The appliance's flue gas exhaust must not be immediately
close to openings or air intakes of buildings, and must com-
ply with environmental regulations.
▶
Do not install near the exhaust of flues, chimneys or hot
polluted air. In order to work correctly, the appliance needs
clean air.
Defrosting water drainage
In winter, it is normal for frost to form on the finned
coil and for the appliance to perform defrosting cy-
cles�
To prevent overflowing and damage provide for a
drainage system.
Acoustic issues
▶
Pre-emptively assess the appliance's sound effect in connec-
tion to the site, taking into account that building corners, en-
closed courtyards, restricted spaces may amplify the acous-
tic impact due to the reverberation phenomenon.
2.4
MINIMUM CLEARANCE DISTANCES
Distances from combustible or flammable materials
▶
Keep the appliance away from combustible or flammable
materials or components, in compliance with applicable
regulations.
Clearances around the appliance
The minimum clearance distances shown in Figure 2.2
(bar any stricter regulations) are required for safety, operation
and maintenance.
Figure 2�2
Clearances
2.5
MOUNTING BASE
Mounting base constructive features
▶
Place the appliance on a levelled flat surface made of fire-
proof material and able to withstand its weight.
(1) - installation at ground level
▶
Failing a horizontal supporting base, make a flat and levelled
concrete base, at least 100-150 mm larger than the appli-
ance dimensions per side.
(2) - installation on terrace or roof
▶
The structure of the building must support the total weight
of the appliance and the supporting base.
▶
If necessary, provide a maintenance walkway around the ap-
pliance.
Anti vibration mountings
Although the appliance's vibrations are minimal, resonance
phenomena might occur in roof or terrace installations.
▶
Use anti-vibration mountings.
▶
Also provide anti-vibration joints between the appliance
and water and gas pipes.
3
HEATING ENGINEER
3.1
WARNINGS
General warnings
Read the warnings in Chapter III.1
p. 4, providing im-
portant information on regulations and on safety.
Compliance with installation standards
Installation must comply with applicable regulations
in force, based on the installation Country and site, in
matters of safety, design, implementation and mainte-
nance of:
heating systems;
cooling systems;
gas systems;
flue gas exhaust;
flue gas condensate discharge.
Installation must also comply with the manufacturer's
provisions.