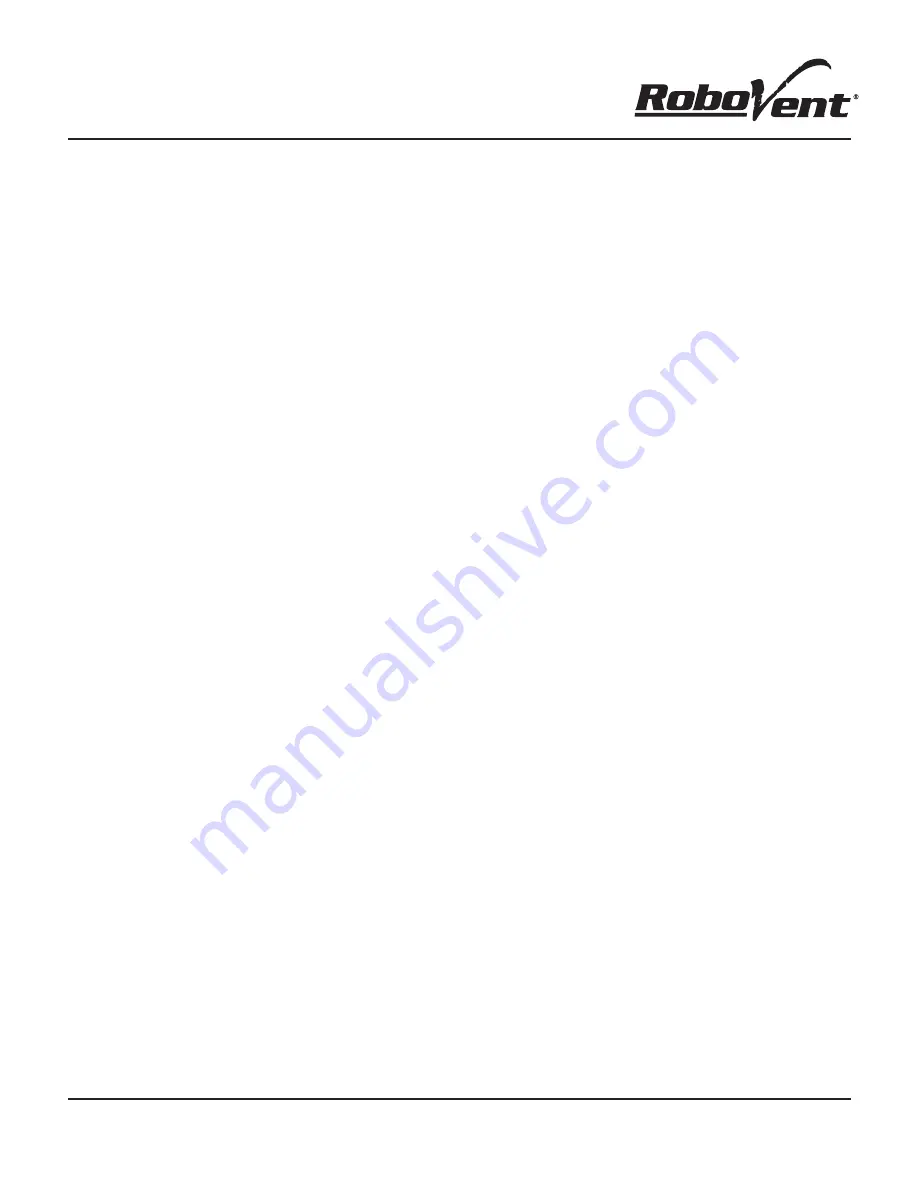
ProCube Owner's Manual & Operating Instructions
E2-20171010
©2017 ROBOVENT PRODUCT GROUP, INC.
13
Preventative Maintenance
Safety
Changing or emptying the dust containment tube, performing monthly
service or changing filters requires PPE to minimize exposure to metal
dust. It is recommended to wear disposable coveralls, non-porous gloves,
dust mask and safety goggles when performing these procedures. Follow
company MSDS and PPE guidelines.
Dust collected by this machine may be hazardous. Toxicity testing must
be performed by your local waster service provider and dust disposed of
according to local disposal and workplace safety regulations.
Changing the Dust Containment Tube
Change or empty the tube as soon as it is full. The time between changes
will vary with production schedules, processes or other factors. A good
estimate of time required between tube changes can be determined after
a few changes; record percentage full and hours each time to help you
estimate when the next change is needed.
To minimize hazards from dust or hazardous chemicals within the dust, the
tube can be capped and disposed.
To change the dust containment tube, follow these steps:
1. Open filter lid, make sure no piles of dust are built up at the bottom
that will fall out when dust tube is removed. Dust tube level can also
be checked here using a flashlight.
2. Grasp the tube around the middle and press down until top of tube is
visible from the side.
3. Rotate top of tube outward. Once top is clear of machine, downward
pressure can be released and dust either emptied or tube capped and
disposed as deemed appropriate by safety policies.
4. Use a vacuum to pick up any dust that spills.
5. Record machine hours and service action.
Monthly Maintenance
On a monthly schedule, perform the following steps and checks:
1. Start machine, allow it to ramp up. Record machine hours and filter
differential pressure. Turn machine off once values are recorded.
2. Press the pulse to enact an offline cleaning cycle.
3. Once pulsing has finished, open filter cabinet and brush any piles of
dust into containment tube at bottom.
4. Inspect inside of cabinet and vacuum out large build up of dust.
5. Inspect hoses for leaks and damage.
6. Close filter compartment and start machine again.
7. Record post-cleaning filter differential pressure.
Filter Change
Once the filter differential pressure gauge has reached the red zone
(indicated by the green & red) above the gauge it is time to replace the filter.
Perform the procedures outlined in monthly maintenance. While filter com-
partment is open, and once cleaning of dust build-up is complete, replace
the existing filter (Filter Part Number: EX3-11D18-B16)