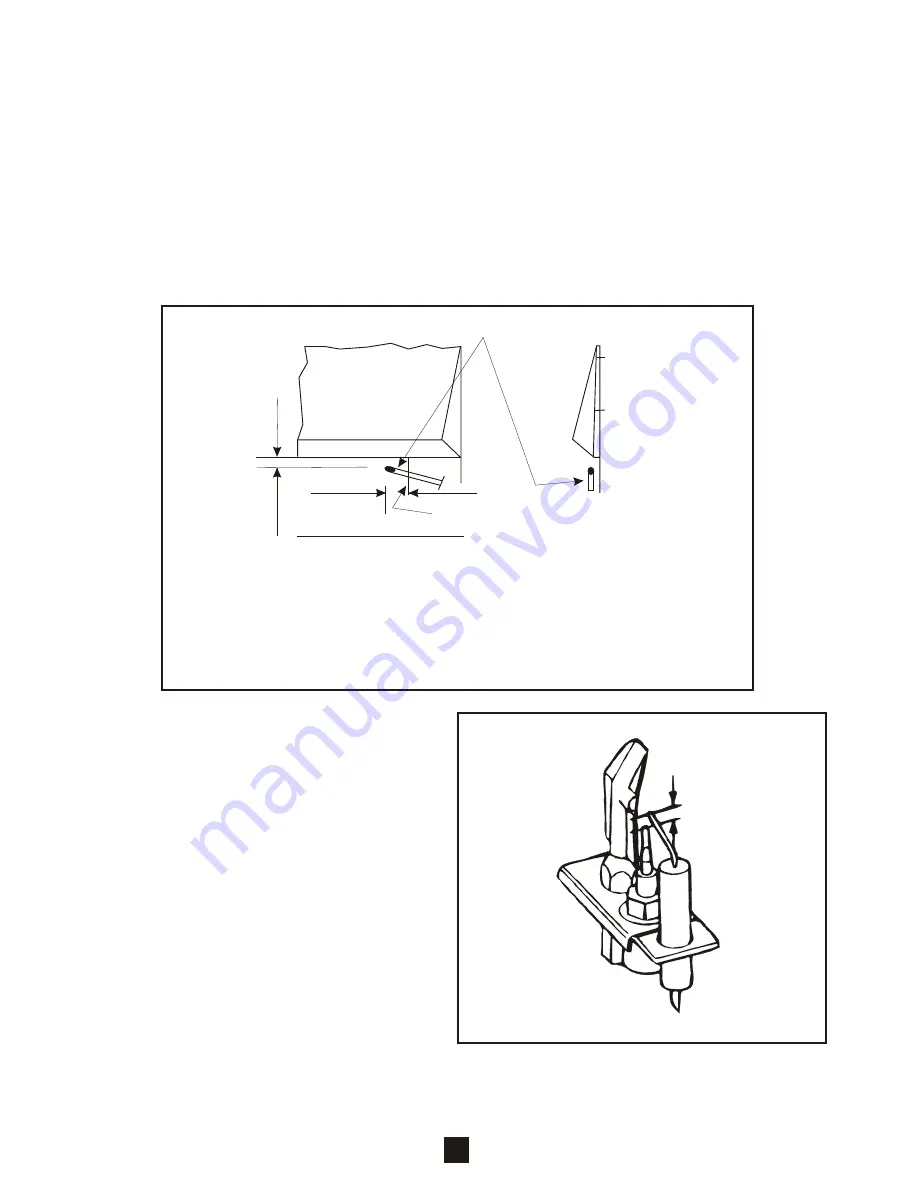
12
4.4 TEST FOR SPILLAGE
A test for spillage must be made before the installed fire is left with the user. This is carried out in the following manner. Light the
fire and leave at HIGH rate. Close all the doors and windows in the room and after the fire has been alight for five minutes insert
a lighted smoke match in line with the bottom edge of the canopy and 10mm below it (See Fig. 8). Hold the match with a pair of
pliers or in a metal tube. If all of the smoke is drawn into the fire the installation is satisfactory. if in doubt, repeat the test after a
further ten minutes.
If there is a fan or a fan operated appliance in a connecting room then the spillage test must be repeated with the fan running
and all inter-connecting doors between the fan and the fire left open. If the fan and the fire are in the same room, close all
windows and doors connected to the room. Switch on the fan and repeat the spillage test.
If spillage is detected, inspect the sealing of the fire to the surround / hearth. If this is satisfactory proceed as follows:
If a spigot restrictor was fitted, disconnect the fire and remove the spigot restrictor. Re-install the fire and repeat the above
spillage test. If there is still evidence of spillage then there may be a fault with the chimney or insufficient air in the room. if the
cause of the spillage cannot be corrected
DISCONNECT THE FIRE AND SEEK EXPERT ADVICE.
4.5 CHECK IGNITION
Check that ignition of the pilot and the cross lighting to the
main burner is satisfactory.
NB. The spark gap between the electrode and
thermocouple tip should be between 3.0 and 5.0mm (See
Fig. 9).
4.6 CHECK OPERATION OF FSD
Leave the fire running on HIGH rate for 5 minutes and then
turn off the gas at the service cock. After 3 minutes turn the
service cock on again. If the gas has stopped flowing the
FSD has operated satisfactorily.
NOTE: You may hear the FSD valve close within the 3
minute period but always check that the gas has stopped
flowing.
Fig. 9
3.0 - 5.0mm
Fig. 8
SMOKE MATCH
AIRBOX SIDE
25.0
1
0
.0
1. FIT CASE.
2. LIGHT FIRE AND LEAVE AT FULL RATE
3. CLOSE ALL DOORS AND WINDOWS
4. AFTER 5 MINUTES INSERT SMOKE MATCH AS SHOWN IN THE DIAGRAM.
5. SMOKE WILL BE DRAWN INTO THE FIRE IF INSTALLATION IS SATISFACTORY.
6. IF SPILLAGE OCCURS, WAIT FOR 10 MINUTES AND REPEAT THE TEST.
7. IF SPILLAGE IS STILL EVIDENT PROCEED AS IN FITTERS INSTRUCTIONS.