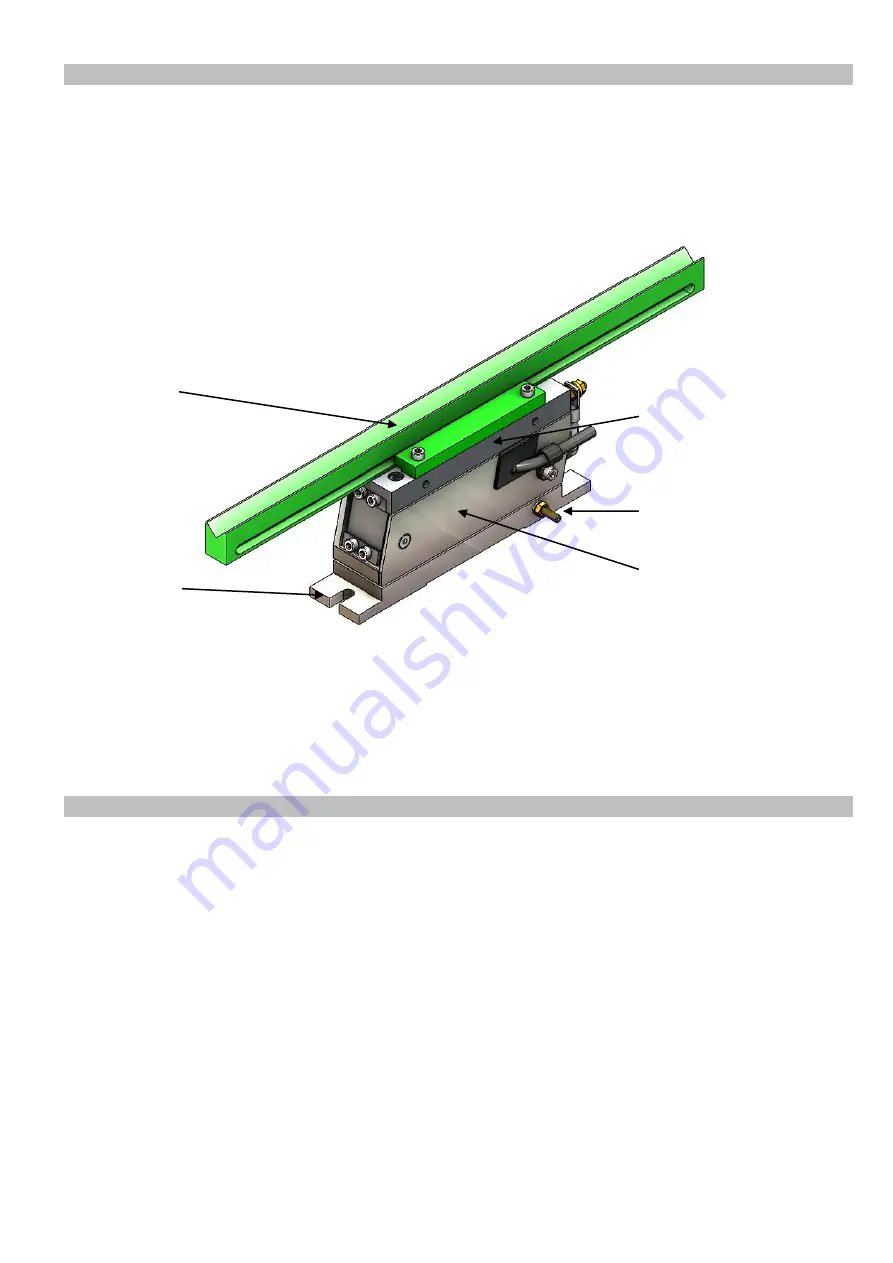
|
10
PARU Mini is a two-mass system. With PARU Mini, exciter mass and useful mass are connected to each
other by spring leaves inclined at a fixed angle. The usable mass also includes the tooling. The vibratory
system is excited by magnets. This results in an oscillating motion of the usable mass. This motion
accelerates the parts in horizontal and vertical direction, causing them to move along the tooling. PARU Mini
oscillates in the range of 100Hz (EU) resp. 120Hz (USA). The vertical amplitude is up to 30µm, the horizontal
amplitude is up to 150 µm.
Fig. 4 illustrates a PARU Mini XS unit with a typical tooling (4) shown green.
Fig. 4: PARU Mini XS with tooling (shown green)
The parts handled are finally oriented and buffered by means of the tooling (4) and the part-specific sorting
elements. Two M6 or M8 screws are used to fasten the PARU Mini to its mount via the stationary baseplate
(1). The exciter mass (2) and useful mass (3 and 4) are the vibrating components. The tooling is part of the
useful mass and is fastened to the useful mass plate (3) by means of clamps, for example. The connection
for user’s earth (5) is located on the baseplate.
We recommend you to observe following general conditions when designing tooling units for PARU Mini.
The tooling must be a rigid body in order to transmit the motion of the useful mass in the best possible way.
We recommend a feed rail height-to-width ratio of 2:1 or higher. We recommend the use of threaded
assemblies suitable for rigid bodies.
To ensure stability of the PARU Mini with minimum transmission of bearing forces to its mount, the rail should
not exceed the maximum weight stated in chapter 2.2.
The tooling centre of gravity should be located in the middle of the PARU Mini, and the centrifugal moment
about the feeding axis of PARU Mini should be close to 0.
For virtual validation of the feeding behaviour and system tuning/matching we recommend to design the
tooling using the CAD dummy for PARU Mini and the simulation tool of Rhein-Nadel Automation GmbH.
2.4.
Functional description
2.5.
Tooling development
4
5
3
2
1