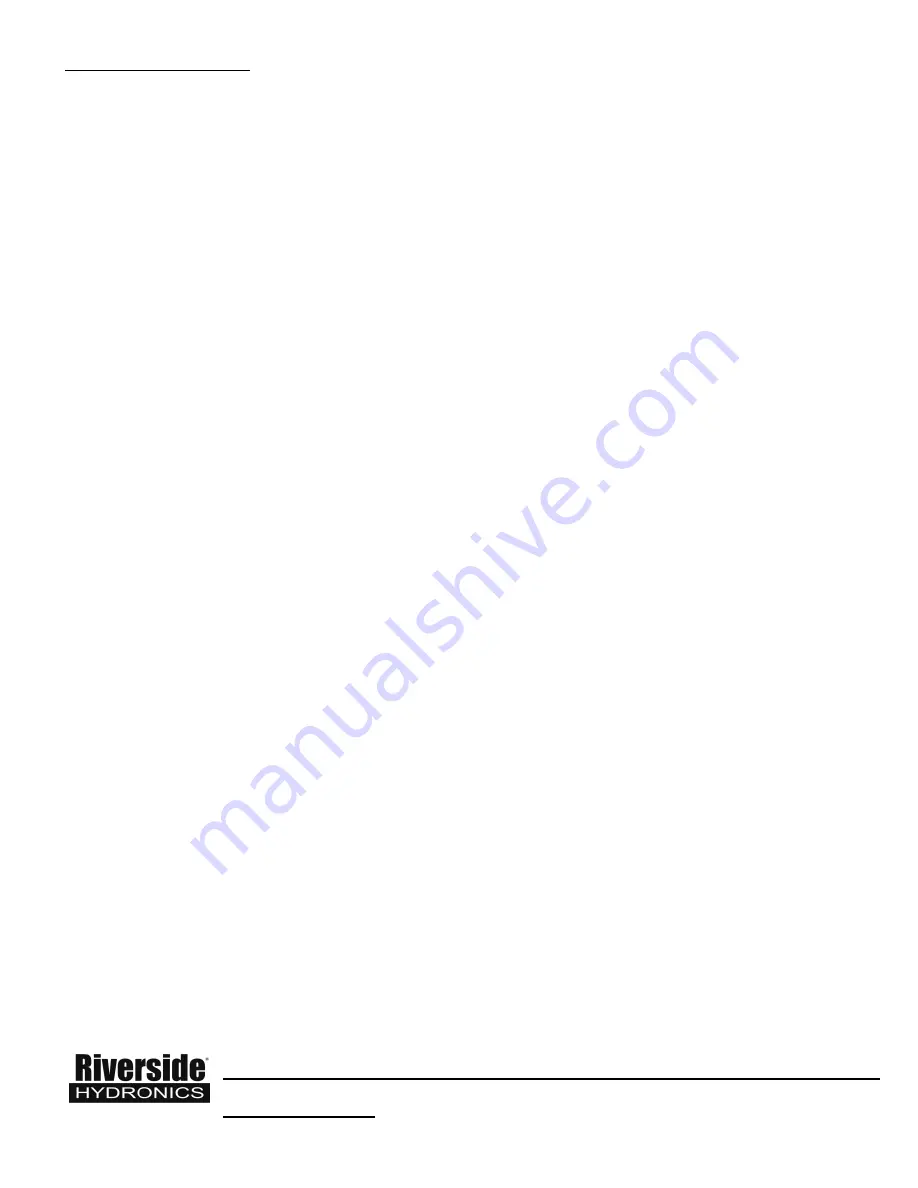
7
WATER CONSIDERATION
WATER CONDITIONING -
Every new system will have certain harmful substances which remain in the boiler and piping
after construction. It is com to find oils, weld slag, and other contaminates within the system. If the foreign materials
remain, the boiler could be affected by loss of heat transfer on heat exchanger surfaces and/or an acidic water condition.
Boiler life may be reduced as a result of an unclean system.
A water treatment company will be able to recommend a chemical cleaning or boil-out procedure.
CHEMICAL TREATMENT -
It is recommended that chemical treatment be provided for initial fill of the system.
Generally, chemicals will be required to prevent scale formation, promote elimination of dissolved gases and control pH.
Most hot water boilers operate in a closed system and are considered to require little attention for water treatment.
Experience has shown, however, few systems can be considered completely closed. Loss of water can occur from
pump packing, glands, air venting devices, and threaded or flanged pipe connections. A means must be provided to
chemically treat the raw water make-up. This is generally accomplished through the use of a shot-type chemical feeder.
Consult a water treatment company for details.
MAKE-UP WATER -
It is generally accepted in system design that hat water boilers are in a closed system and,
therefore, no make-up water is needed. This is not always the case. Untreated make-up water is a leading cause for
failures of hat water boilers. Provisions must be made for properly introducing, metering, and treating make-up water.
Below are some considerations.
•
Provision should be made for removal of air from the make-up water.
•
It is recommended that make-up water be tempered so as not to introduce cold water to the system.
•
A raw water meter should be used to identify the amount of water used by the system. This may indicate a
potential problem with the system.
ETHYLENE GLYCOL AS HEAT TRANSFER MEDIUM -
On application requiring freeze protection, a mixture of
ethylene glycol and water is commonly used.
When using ethylene glycol certain design limitations are important, due to the characteristics of the fluid verses water.
These characteristics are: Elevated saturation temperature, and increased viscosity and density. In addition, ethylene
glycol degrades when it is heated above the manufacturer’s specified maximum film temperature.
The following design parameters must be followed when operating EMBLEM
®
with ethylene glycol:
•
The maximum concentration should be 50%.
•
Maximum temperature 200°F.
•
Minimum operating pressure 50 psig.
•
A means of monitoring the condition of the system fluid should be provided. Frequent analysis of the system
should be conducted in the first few month of operation. Simi-annual checks thereafter are recommended.
•
Excessive use of inhibitors can create precipitation of solids causing reduce circulation and reduced heat
transfer.
Riverside Hydronics
®
, LLC - 990 Haltom Road - Fort Worth, Texas 76117 - Tel 1-800-990-5918
LEAD/LAG SYSTEMS