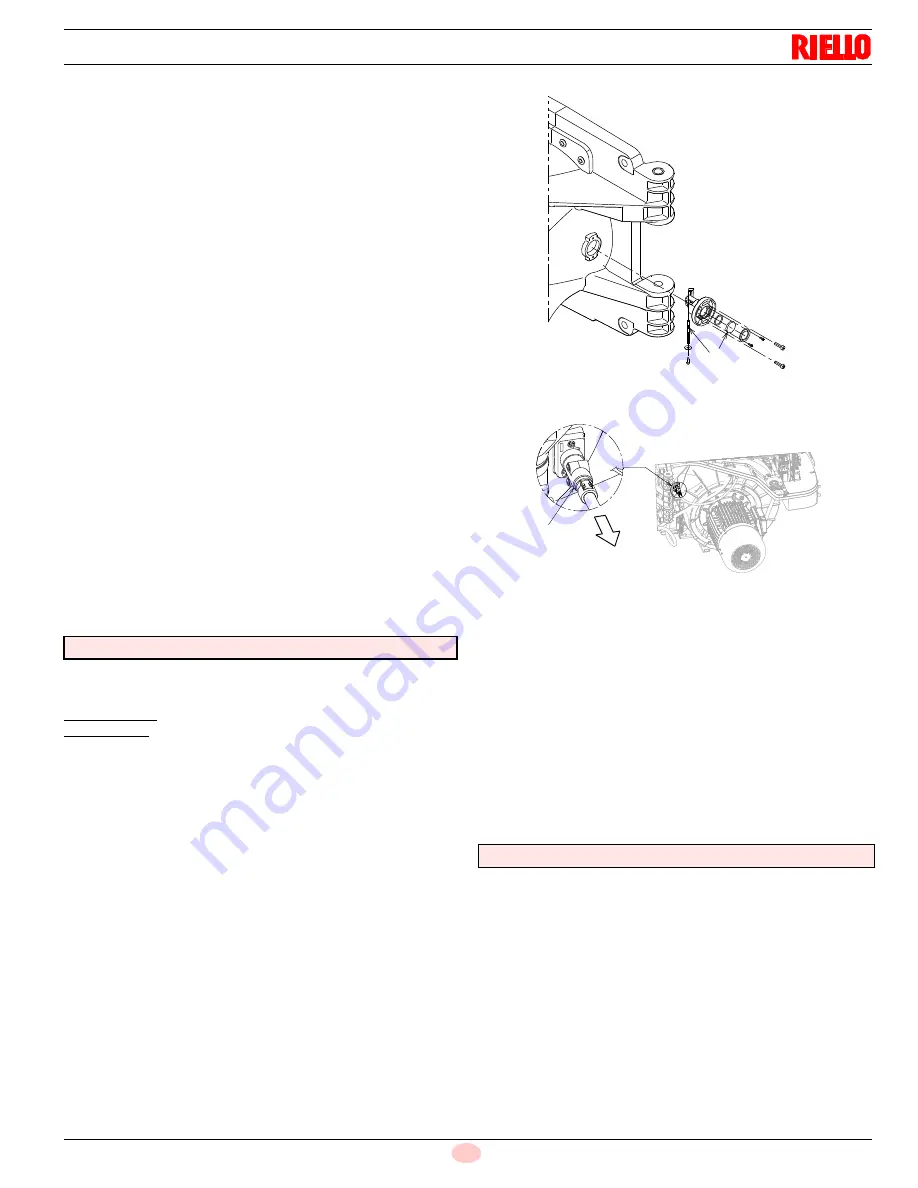
Maintenance
43
20106891
GB
Flame inspection window
Clean the flame inspection window 1)(Fig. 40).
Fan
Check to make sure that no dust has accumulated inside the fan or
on its blades, as this condition will cause a reduction in the air flow
rate and provoke polluting combustion.
Boiler
Clean the boiler as indicated in its accompanying instructions in or-
der to maintain all the original combustion characteristics intact, es-
pecially the flue gas temperature and combustion chamber
pressure.
Combustion
The optimum calibration of the burner requires an analysis of the
flue gases. Significant differences with respect to the previous
measurements indicate the points where more care should be ex-
ercised during maintenance.
In case the combustion values found at the beginning of the inter-
vention do not respect the standards in force or, in any case, do not
correspond to a proper combustion, contact the Technical Assis-
tant and have him carry out the necessary adjustments.
Pump
Delivery pressure must correspond with the Tab. L on page 26.
The depression must be less than 0.45 bar
.
Unusual noise must not be evident during pump operation
.
If the pressure is found to be unstable or if the pump runs noisily,
the flexible hose must be detached from the line filter and the fuel
must be sucked from a tank located near the burner. This measure
permits the cause of the anomaly to be traced to either the suction
line or the pump.
If the problem lies in the suction line, check to make sure that the
filter is clean and that air is not entering the piping.
Filters
Check the filtering baskets on line and at nozzle present in the sys-
tem. Clean or replace if necessary.
If rust or other impurities are observed inside the pump, use a sep-
arate pump to lift any water and other impurities that may have de-
posited on the bottom of the tank.
Nozzles
It is advisable to replace nozzles every year during regular main-
tenance operations.
Do not clean the nozzle openings; do not even open them.
Combustion must be checked after the nozzles have been
changed.
Flexible hoses
Check to make sure that the flexible hoses are still in good condi-
tion and that they are not crushed or otherwise deformed.
Fuel tank
Approximately every 5 years, or whenever necessary, suck any
water or other impurities present on the bottom of the tank using a
separate pump.
Gas leaks
Make sure that there are no gas leaks on the pipework between the
gas meter and the burner.
Gas filter
Change the gas filter when it is dirty.
1
Fig. 40
20123216
2
Fig. 41
20123221
LIGHT OIL OPERATION
GAS OPERATION
Содержание RLS 280/E
Страница 2: ...Original instructions ...
Страница 47: ...Appendix Spare parts 45 20106891 GB A Appendix Spare parts ...
Страница 53: ......
Страница 54: ......
Страница 55: ......