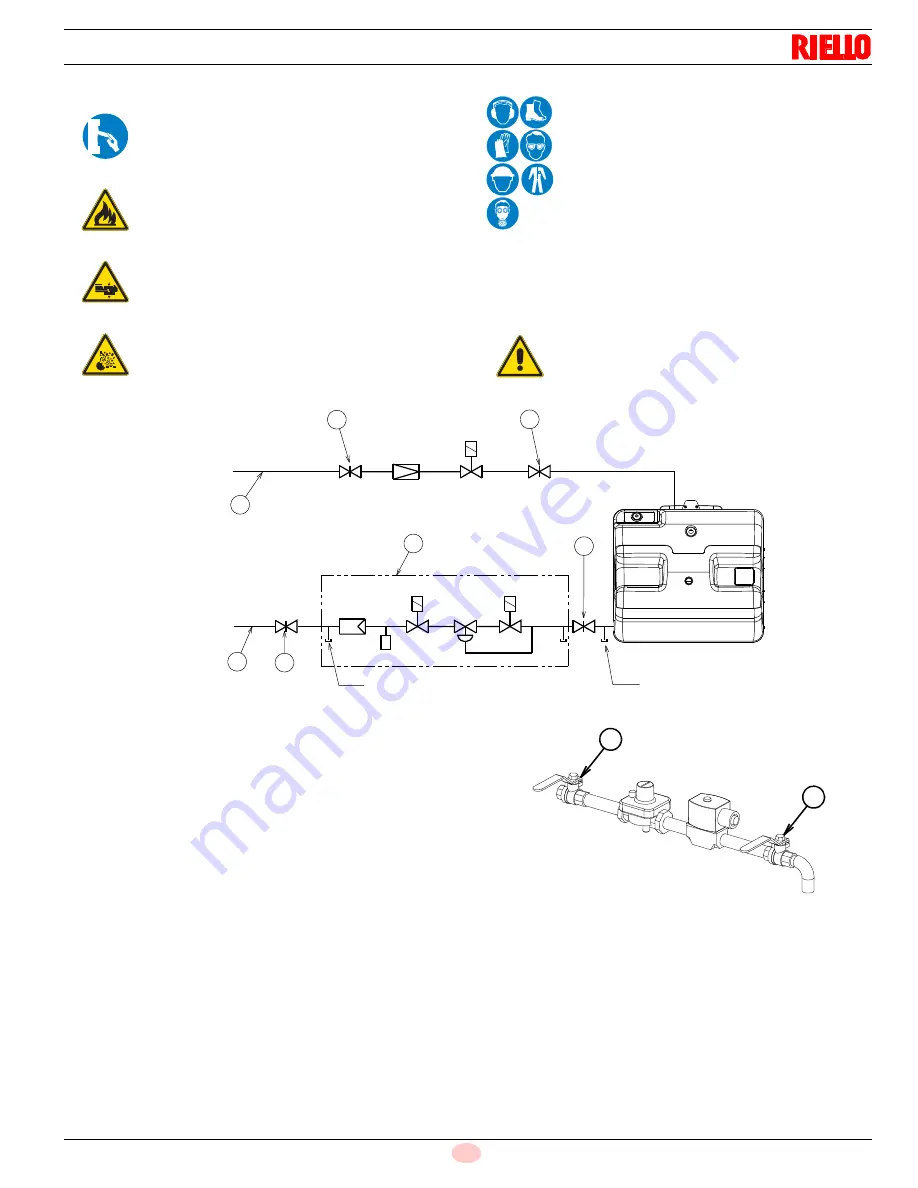
Installation
25
20093868
GB
4.8.1
Gas line
This has been type-approved in accordance with regulation NFPA
54/ANSI Z223.1 National Fuel Gas Code, NFPA 58 Liquefied Pe-
troleum Gas Code, and International Fuel Gas Code, CAN/CGA
B149.1 & B149.2 Installation Codes, and is supplied as standard
(Fig. 22).
4.8.2
Gas pilot line
Key (Fig. 22 - Fig. 23)
1
Gas supply
2
Manual valve
3
Valve including:
F
screen/strainer
V1 1
st
SSOV
R
pressure regulator
V2 2
nd
SSOV
L
Gas train supplied
LGP
Low gas pressure switch
P1
Upstream gas pressure test point
P2
Downstream gas pressure test point
PR
Pressure regulator
VS1
Safety shut-off valve
Before carrying out maintenance, cleaning or
checking operations, identify and close the manual
shut-off valve on the gas supply drop-line to the
burner.
Check that there are no gas leaks.
Beware of train movements: danger of crushing of
limbs.
Make sure that the gas train is properly installed by
checking for any fuel leaks.
The operator must use appropriate tools for instal-
lation.
CAUTION
Recommended pilot gas pressure: 2 - 8 “wc.
V1
V2
R
F
1
2
3
P1
LGP
2
VS1
1
PR
2
2
GAS PILOT LINE
MAIN GAS LINE
P2
Fig. 22
20092909
Fig. 23
20093850
PR
VS1
2
2
Содержание 20082125
Страница 2: ...Original instructions ...
Страница 77: ......
Страница 78: ......
Страница 79: ......