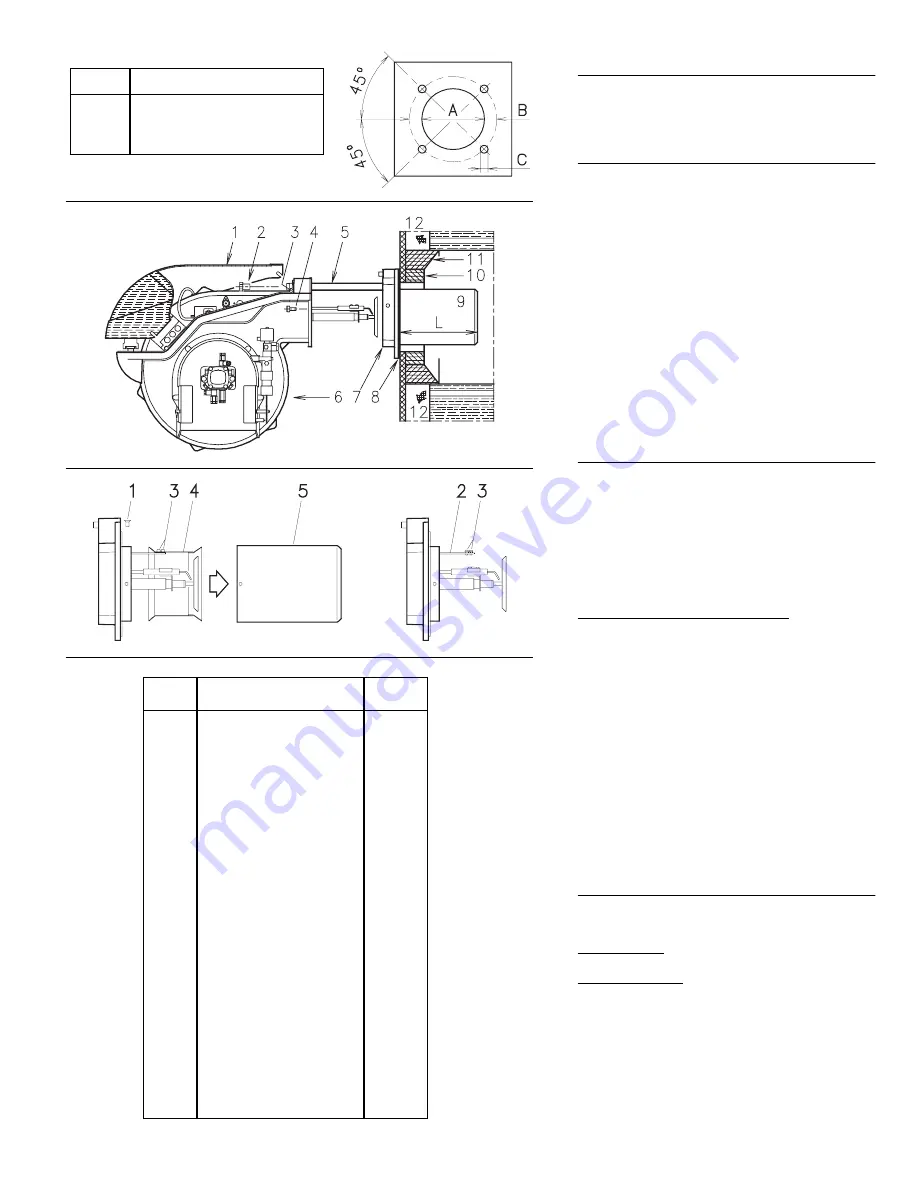
6
INSTALLATION
BOILER PLATE (A)
Drill the combustion chamber mounting plate as
shown in (A). The position of the threaded holes can
be marked using the burner gasket supplied with the
burner.
BLAST TUBE LENGTH (B)
The length of the blast tube must be selected accord-
ing to the indications provided by the manufacturer of
the boiler, and it must be greater than the thickness of
the boiler door complete with its insulation. The range
of lengths available, L (inch), is as follows:
Blast tube 9):
RL 70
RL 100
RL 130
• short
9
27/32
9
27/32
9
27/32
• long (with the kit)
15
5/32
15
5/32
15
5/32
For boilers with front flue passes 12) or flame inversion
chambers, protective insulation material 10) must be
inserted between the boiler's refractory 11) and the
blast tube 9).
This protective insulation must not compromise the ex-
traction of the blast tube.
For boilers having a water-cooled front, the insulation
10)-11)(B) is not required unless it is required by the
boiler manufacturer.
SECURING THE BURNER TO THE BOILER (B)
Disassemble the blast tube 9) from the burner 6) by
proceeding as follows:
- Loosen the four screws 3) and remove the cover 1).
- Remove the screws 2) from the two slide bars 5).
- Remove the two screws 4) fixing the burner 6) to the
flange 5).
- Withdraw the blast tube 9) complete with flange 7)
and slide bars 5).
COMBUSTION HEAD CALIBRATION
At this point check, for model RL 130, whether the
maximum delivery of the burner in high fire operation
is contained in area B or in area C of the firing rate.
See page 5.
If it is in area B then no operation is required.
If, on the other hand, it is in area C:
- Unscrew the screws 1)(C) and disassemble the
blast tube 5).
- Unscrew the screws 3) and remove the shutter 4).
- Tighten the screws 3) on the rod 2).
- Now refit the blast tube 5) and the screws 1).
Once this operation has been carried out (if required),
secure flange 7)(B) to the boiler plate inserting the
supplied gasket 8). Use the 4 screws provided after
having protected the thread with an antiseize product
(high-temperature grease, compounds, graphite). The
burner-boiler seal must be airtight.
CHOICE OF NOZZLES FOR LOW AND HIGH FIRE
Both nozzles must be chosen from among those listed
in Table (D).
The first nozzle determines the delivery of the burner
at low fire.
The second nozzle works in combination with the low
fire nozzle to determine the delivery of the burner at
high fire.
The total deliveries of low and high fire must be con-
tained within the value range indicated on page 3.
Use nozzles with a 60° spray angle at the recommend-
ed pressure of 174 PSI.
(A)
inch
A
B
C
RL 70
7
9/32
“
10
27/32
“ - 12
13/16
“
1/2
W
RL 100
7
9/32
“
10
27/32
“ - 12
13/16
“
1/2
W
RL 130
7
9/32
“
10
27/32
“ - 12
13/16
“
1/2
W
Nozzle
size
GPH
MBtu/hr
174 PSI
145 PSI
174 PSI
203 PSI
5.0
5.5
6.0
6.5
7.0
7.5
8.0
8.3
8.5
9.0
9.5
10.0
10.5
11.0
12.0
12.3
13.0
13.8
14.0
15.0
15.3
16.0
17.0
17.5
18.0
19.0
19.5
20.0
21.5
22.0
6.15
6.76
7.40
8.00
8.61
9.22
9.86
10.21
10.47
11.08
11.69
12.30
12.94
13.54
14.76
15.15
16.01
17.00
17.23
18.48
18.83
19.69
20.94
21.55
22.16
23.38
24.01
24.62
26.48
27.09
6.79
7.46
8.17
8.84
9.51
10.18
10.85
11.27
11.56
12.23
12.90
13.58
14.28
14.95
16.30
16.71
17.64
18.73
19.02
20.37
20.78
21.74
23.09
23.76
24.46
25.81
26.48
27.15
29.20
29.86
7.40
8.13
8.87
9.60
10.34
11.08
11.81
12.26
12.55
13.29
14.06
14.76
15.50
16.23
17.71
18.16
19.18
20.27
20.65
22.16
22.57
23.63
25.10
25.84
26.58
28.05
28.79
29.52
31.73
32.47
951
1044
1144
1238
1331
1425
1519
1578
1618
1712
1806
1901
1999
2093
2282
2339
2470
2622
2663
2852
2909
3044
3233
3326
3424
3613
3707
3801
4088
4180
(B)
(C)
D455
D2326
D690
(D)