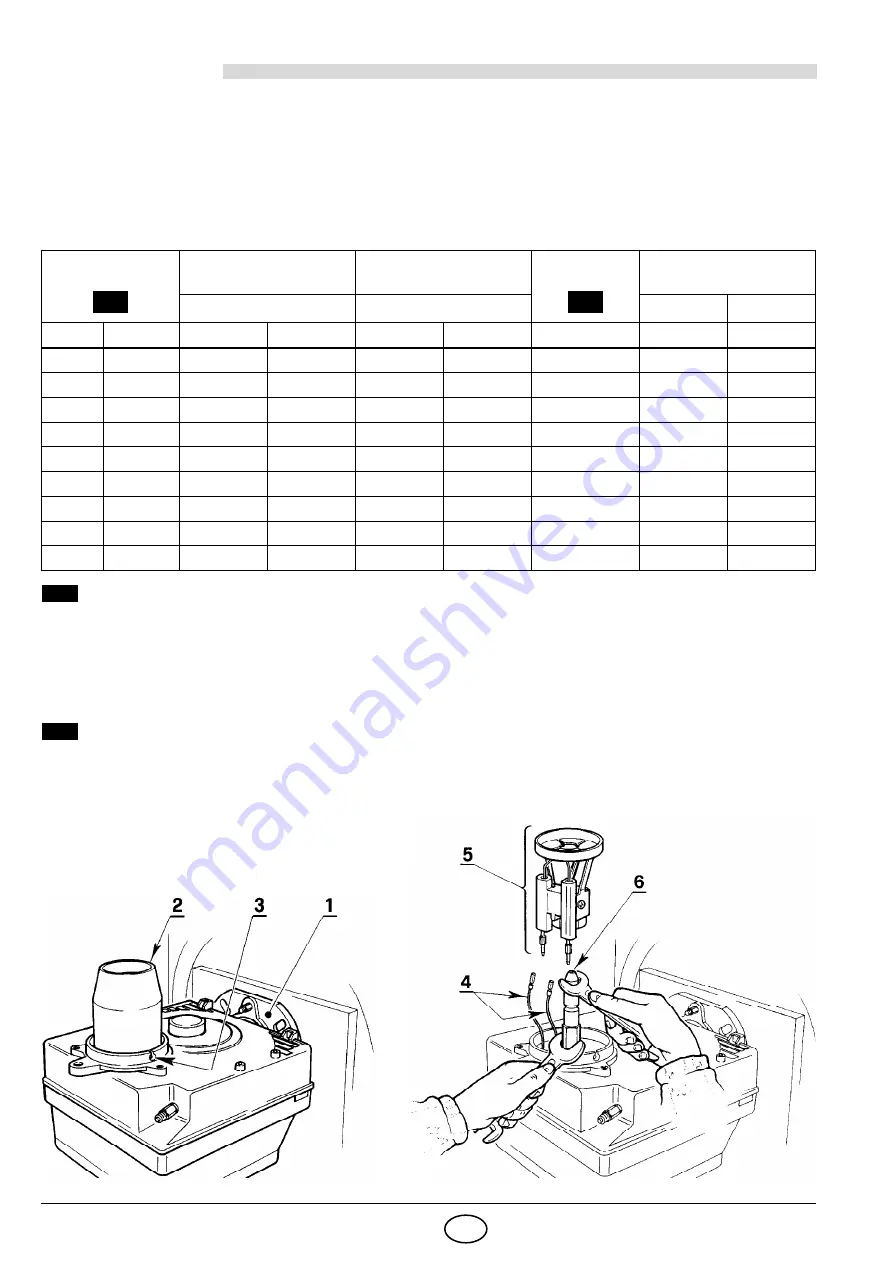
2305
6
GB
4.
WORKING
4.1
COMBUSTION ADJUSTMENT
In conformity with Efficiency Directive 92/42/EEC the application of the burner on the boiler, adjustment and
testing must be carried out observing the instruction manual of the boiler, including verification of the CO and CO
2
concentration in the flue gases, their temperatures and the average temperature of the water in the boiler.
To suit the required appliance output, choose the proper nozzle and adjust the pump pressure, the setting of
the combustion head, and the air damper opening in accordance with the following schedule.
Values in the table refer to 12% CO
2
and to sea level.
RECOMMENDED
NOZZLES
Monarch type R,
Delavan type W - E,
Steinen type Q,
Danfoss type S,
Satronic type S.
MAINTENANCE POSITION
Nozzle
Pump pressure
Burner output
Comb. head
adjustment
Air damper
adjustment
bar
kg/h ± 4%
1st stage
2nd stage
GPH
Angle
1st stage
2nd stage
1st stage
2nd stage
Set-point
Set-point
Set-point
0.40
80°
9
14
1.3
1.7
0.3
0
0.6
0.50
60° / 80°
9
14
1.7
2.1
1
0
0.9
0.60
60°
9
14
2.0
2.5
1.3
0.1
1.3
0.65
60° / 45°
9
14
2.2
2.7
1.5
0.2
1.7
0.75
60° / 45°
9
14
2.5
3.1
2
0.4
2.2
0.85
45°
9
14
2.8
3.5
3
0.5
2.7
1.00
45°
9
14
3.3
4.2
4
0.7
3.8
1.10
45°
9
14
3.7
4.6
5
0.8
4
1.25
45°
9
13
4.2
5.0
6
1
6
1
2
1
Fig. 11
S7197
S7184
THE ACCESSIBILITY TO THE NOZZLE, THE DIFFUSER DISC AND THE ELECTRODES IS MADE EASY
IN 2 WAYS:
Fig. 11
– Remove the burner out of the boiler, after loosing the fixing nut to the flange.
– Hook the burner to the flange (1), by removing the blast tube (2) after loosing the fixing screws (3).
– Remove the small cables (4) from the electrodes and the diffuser disc-holder assembly (5) from the noz-
zle-holder assembly after loosing its fixing screw (3, fig. 13, page 7).
– Screw the nozzle (6) correctly and tighten
it as shown in the figure.
A