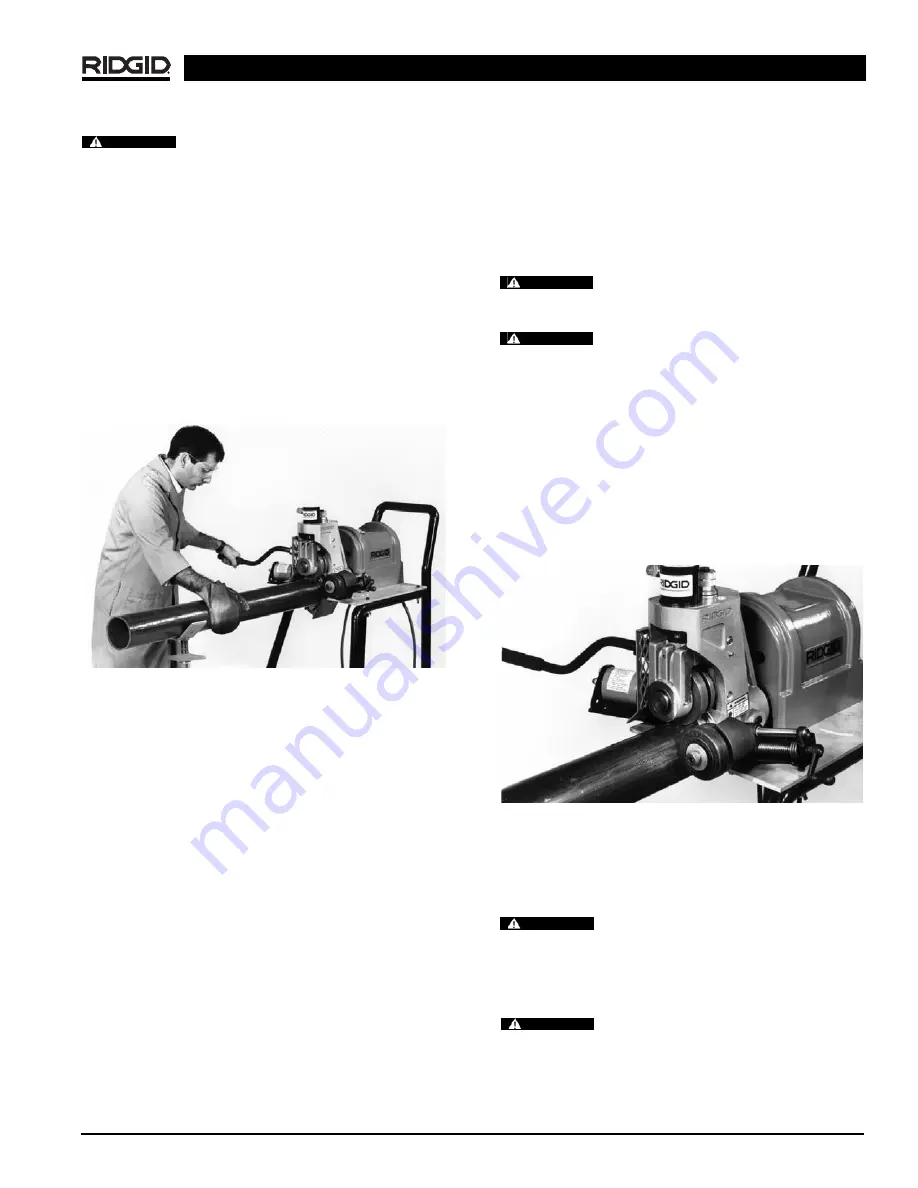
918-I Heavy Duty Roll Grooving Machine
Ridge Tool Company
9
Do not reach inside of pipe. Keep hands
away from sharp edges and burrs on end of pipe.
NOTE! Do not overfeed upper groove roll. Maintain con-
stant even downward pressure, pausing to allow
one pipe revolution per quarter stroke of the
pump handle.
3. When the depth adjustment knob contacts the ma-
chine casting, allow two complete pipe revolutions
to even out groove depth.
4. Release foot switch and retract upper groove roll by
placing the pump release lever in the RETURN posi-
tion (toward operator).
5. Check groove diameter before proceeding with addi-
tional grooves.
Figure 9 – Grooving Pipe While Exerting Light Hand
Pressure Toward Operator
NOTE! Groove diameter should be measured using a di-
ameter tape. To decrease groove diameter (in -
crease groove depth), rotate the index depth ad-
justment knob one mark counter-clockwise. To in -
crease groove diameter (decrease groove depth),
rotate the depth adjustment knob clockwise.
Roll Grooving Tips with Model 918-I
1. If pipe tends to “walk off” drive roll, increase offset di-
mension
(Figure 7).
2. If drive roll flange shaves pipe end, decrease offset di-
mension.
3. If pipe end flare is excessive, lower pipe end to level
with roll groover.
4. If pipe wobbles and/or “walks off” drive roll, raise pipe
end to level with roll groover.
5. Short lengths of pipe (under three feet) may require
slight pressure to maintain the
1
/
2
degree offset di-
mension.
Grooving Short Lengths of Pipe
Without Stabilizer
1. Properly set-up pipe to ensure pipe is level and square
on the shoulder of the drive roll.
2. When grooving, exert pressure on the pipe towards
the operator
(Figure 9).
Do not attempt to groove any pieces of
pipe shorter than 8
″
(See Chart A). Increases risk of fingers
being crushed in the grooving rolls.
Do not reach inside of pipe. Keep hands
away from sharp edges and burrs on end of pipe.
With Stabilizer
NOTE! Once stabilizer is adjusted for a selected pipe
diameter and wall thickness, it does not have to
be readjusted.
1. Properly set up pipe to ensure pipe is level and square
on the shoulder of the drive roll.
2. Engage hydraulic pump and bring groove roll (upper
roll) down until it contacts outside diameter of the
pipe.
3. Tighten down stabilizer roll until roll contacts outside di-
ameter of the pipe. Continue to tighten stabilizer one
full turn after making contact on outside diameter of
pipe
(Figure 10).
Do not reach across pipe to adjust stabilizer.
NOTE! If pipe “walks off” of drive shaft during the roll
grooving operation, the stabilizer will need to be
further tightened
1
/
2
turn.
Do not use the pipe stabilizer on 8
″
or
short er workpieces. Increases risk of fingers being crushed
in the grooving rolls.
WARNING
WARNING
Figure 10 – Adjusting Pipe Stabilizer
WARNING
WARNING
WARNING