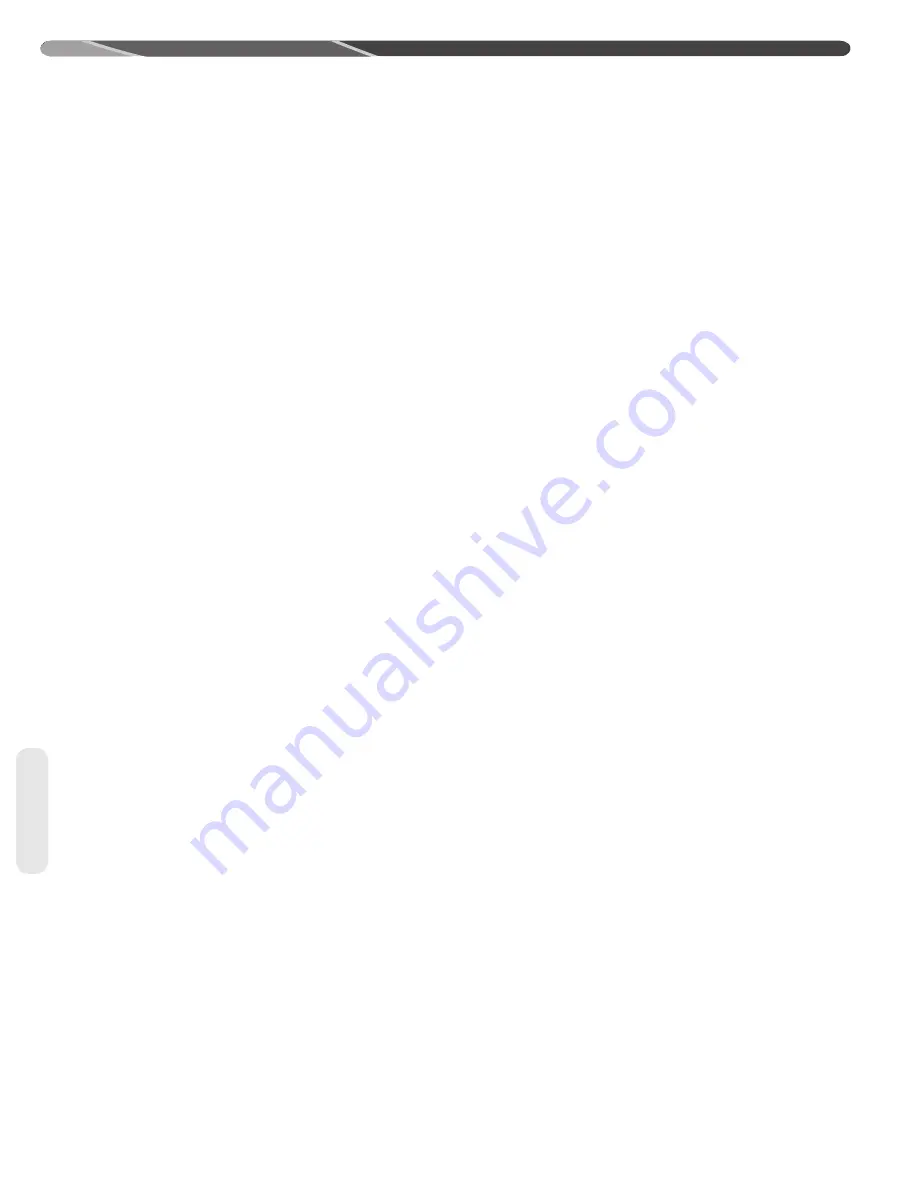
26
Start-Up
5.0 SYSTEM START-UP AND REFRIGERANT CHARGING
5.4 Initial System
Start-Up
Using the EcoNet™ Control Center service menu
(See Section 5.5 below) or using the thermostat
and air-handler or gas furnace control board TEST
& SW2 buttons (See Section 5.6 below), put the
system into the charging mode which will force it
to operate at 100% capacity and indoor air-flow
which is necessary for accurate indoor air-flow
verification and refrigerant charging. Check to
make sure “On-Demand Dehumidification” is
turned off in the EcoNet™ Control Center (or on
the air-handler or gas furnace control board for
conventional 24VAC control applications).
5.5 Entering Charge
Mode Using EcoNet
™
Control Center Service
Menu
1. Set the "Mode" to the "OFF" position.
2. Select "SERVICE" on the EcoNet™ Control
Center screen.
3. Select "ODU Checkout". If the next screen dis-
plays a flashing "Lock-Out" message, there will
be up to a 5 minute delay before it is possible
to continue.
4. Once the flashing lock-out message disap-
pears, touch OFF on the screen displayed to
the right of "Var Speed ODU Test".
5. Touch the "UP" arrow repeatedly until the "Heat
Charge" or "Cool Charge" menu item is dis-
played depending on which mode the system is
to be charged in.
6. Touch "Start Test".
7. System will now operate at 100% of capacity
and indoor air-flow to allow proper indoor air-
flow verification and refrigerant charging until
the Charge Mode is manually ended. There
may be a delay before the system actually
starts. If the system doesn't start, cycle power
to both the indoor and outdoor units and repeat
steps 1-6.
8.
Note:
When charging in the heating mode,
the system will initiate a defrost cycle every 34
minutes if the coil temperature is below 35ºF
[1.7ºC] to assure the coil stays frost free during
the charging process. Allow the system to
complete the defrost cycle and stabilize for at
least 10 minutes before attempting to evaluate
the charge level.
9. To end Charge Mode, touch the "UP" arrow
repeatedly until "OFF" is displayed on the
screen and then touch "Stop Test". Then touch
the left arrow on the screen to return to the
main screen.
10. If the indoor blower continues to run continu-
ously after exiting the Charge Mode, cycle the
power to the air-handler or furnace.
5.6 Entering Charge
Mode Using Variable
Speed Outdoor Control
(VSODC) Menu When
Using a Conventional
2-Stage 24VAC
Thermostat
1. Set the thermostat to the cool or heat mode
depending on which mode the system is to be
charged in.
2. Adjust the set point several degrees below
(cool mode) or above (heat mode) the room
temperature to assure the thermostat is calling
for 2nd stage operation and will continue to do
so throughout the charging process.
3. Depress the TEST and SW2 buttons on the
VSODC at the same time for 5-8 seconds.
4. The dual seven segment LED display should
show the first menu option of FC.
5. Depress the TEST button one time and the
display should switch to CS which represents
Compressor Speed.
6. Depress the SW2 button to enter the Compres-
sor Speed Menu.
7. The Display should show a value of 3. If a
value of 1 is displayed, the thermostat is not
calling for 2nd stage. Check the wiring and set-
point before proceeding and make the neces-
sary corrections until a 3 is displayed.
8. System will now operate at 100% of capacity
and indoor air-flow to allow proper indoor air-
flow verification and refrigerant charging until
the Charge Mode is manually ended. There
may be a delay before the system actually
starts. If the system doesn't start, cycle power
to both the indoor and outdoor units and repeat
steps 1-7.
9.
Note:
When charging in the heating mode,
the system will initiate a defrost cycle every 34
minutes if the coil temperature is below 35ºF
[1.7ºC] to assure the coil stays frost free during
the charging process. Allow the system to
complete the defrost cycle and stabilize for at
least 10 minutes before attempting to evaluate
the charge level.
10. After the charging process is complete, push
the TEST button to exit the Compressor Speed
menu which will alow the thermostat to regain
control of the system. The system will automat-
ically exit the Compressor Speed menu after 24
hours if it is not exited manually.