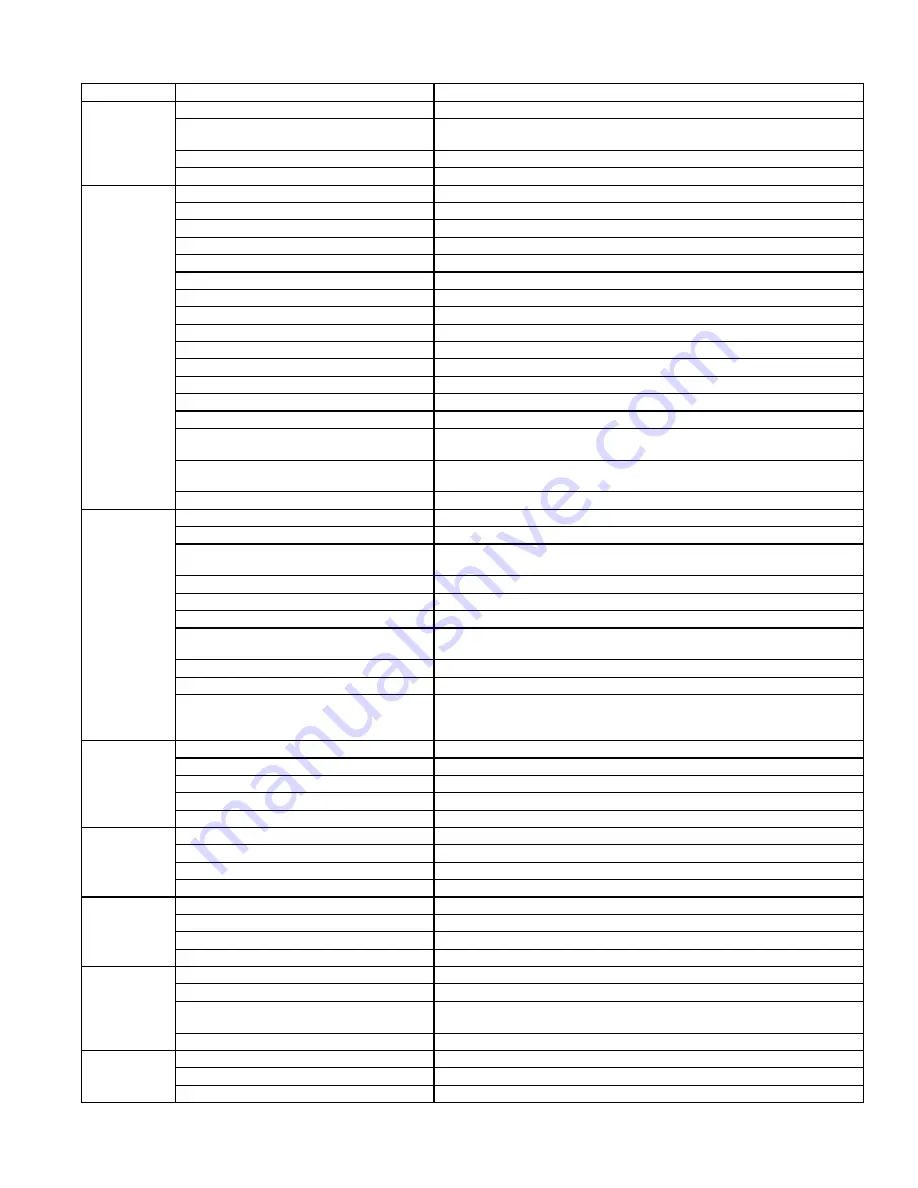
Form I-SSCBL/RPBL, P/N 149159 R8, Page 57
10.3 Troubleshooting
TROUBLE
PROBABLE CAUSE
REMEDY
Venter motor
will not start
1.
No power to the furnace.
1.
Turn on power, check supply fuses or circuit breaker.
2.
No 24-volt power to venter relay.
2.
Turn up thermostat, check control transformer output. Check for loose or
improper wire connections.
3.
Venter relay defective.
3.
Replace.
4.
Defective motor or capacitor.
4.
Replace defective part.
Pilot will not
light -- Venter
operating
1.
Manual valve not open.
1.
Open manual valve.
2.
Air in gas line.
2.
Bleed gas line.
3.
Dirt in pilot orifice.
3.
Remove and clean with compressed air or solvent.
4.
Gas pressure too high or too low.
4.
Adjust supply pressure. (See Paragraph 6.1).
5.
Kinked pilot tubing.
5.
Replace tubing.
6.
Pilot valve does not open.
6.
If 24 volts available at the valve, replace valve.
7.
No spark:
7.
a)
Loose wire connections
a)
Be certain all wires connections are solid.
b)
Transformer failure.
b)
Be certain 24 volts is available.
c)
Incorrect spark gap.
c)
Maintain spark gap at .100".
d)
Spark cable shorted to ground.
d)
Replace worn or grounded spark cable.
e)
Spark electrode shorted to ground.
e)
Replace pilot if ceramic spark electrode is cracked or grounded.
f)
Drafts affecting pilot.
f)
Make sure all panels are in place and tightly secured to prevent drafts at pilot.
g)
Ignition control not grounded.
g)
Make certain ignition control is grounded to furnace chassis.
h)
Faulty ignition controller.
h)
If 24 volt is available to the ignition controller and all other causes have been
eliminated, replace ignition control.
8.
Optional lockout device interrupting control
circuit by above causes.
8.
Reset lockout by interrupting control at thermostat.
9.
Faulty combustion air proving switch.
9.
Replace combustion air proving switch.
Pilot lights,
main valve will
not open
1.
Manual valve not open.
1.
Open manual valve.
2.
Main valve not operating.
2.
a)
Defective valve.
a)
If 24 volt is measured at valve connections and valve remains closed,
replace valve.
b)
Loose wire connections.
b)
Check and tighten all wiring connections.
3.
Ignition control does not power main valve.
3.
a)
Loose wire connections.
a)
Check and tighten all wiring connections.
b)
Flame sensor grounded. (Pilot lights - spark
continues)
b)
Be certain flame sensor lead is not grounded or insulation or ceramic is not
cracked. Replace as required.
c)
Gas pressure incorrect.
c)
Adjust gas pressure. (See Paragraph 6.1.)
d)
Cracked ceramic at sensor.
d)
Replace sensor.
e)
Faulty ignition controller.
e)
See Paragraph 10.2.2. If all checks indicate no other cause, replace ignition
controller.
Do not
attempt to repair the ignition controller. This device has no
field replaceable parts.
No heat (Heater
operating)
1.
Dirty filters in blower system.
1.
Clean or replace filters.
2.
Incorrect manifold pressure or orifices.
2.
Check manifold pressure (See Paragraph 6.1).
3.
Cycling on limit control.
3.
Check air throughput.
4.
Improper thermostat location or adjustment.
4.
See thermostat manufacturer's instructions.
5.
Belt slipping on blower
5.
Adjust belt tension
Cold air - On
startup/ during
operation
1.
Fan control improperly wired
1.
Connect as per wiring diagram.
2.
Defective fan control.
2.
Replace fan control.
3.
Incorrect manifold pressure.
3.
Check manifold line pressure (See Paragraph 6.1).
4.
Blower set for too low temperature rise.
4.
Slow down blower or increase static pressure. (See Paragraph 6.5.)
Motor will not
run
1.
Circuit open
1.
Check wiring and connections.
2.
Fan control inoperative
2.
Replace fan control.
3.
Contactor inoperative
3.
Replace contactor.
4.
Defective motor.
4.
Replace motor.
Motor turns
on and off
while burner is
operating
(see below)
1.
Fan control heater element improperly wired.
1.
Connect as per wiring diagram.
2.
Defective fan control
2.
Replace fan control.
3.
Motor overload device cycling
3.
Check motor load against motor rating plate. Replace motor or overload
device.
4.
3-phase motor rotating in opposite direction
4.
Interchange two legs of supply connections.
Motor cuts out
on overload
1.
Improper motor pulley adjustment
1.
See instructions on air throughput (See Paragraph 6.5).
2.
Improper static pressure on duct system
2.
Adjust dampers in duct system.
3.
Low voltage
3.
Check power supply.
Содержание RPBL 1050
Страница 58: ...Form I SSCBL RPBL P N 149159 R8 Page 58 ...