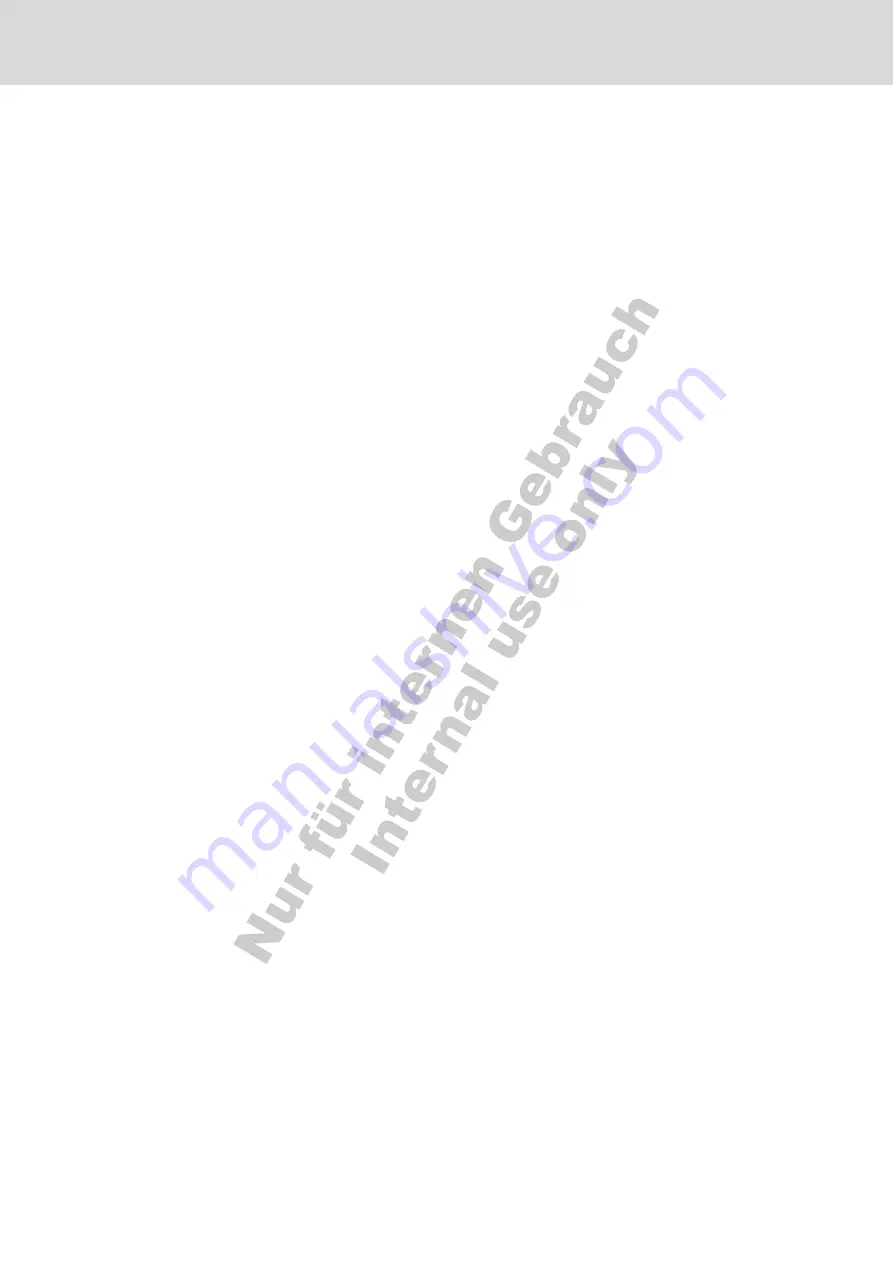
minimize radiation of interference fields. If possible, route the motor power
cables and motor encoder cables in metal-grounded cable ducts.
Route the motor power cables and motor encoder cables
●
with a distance of at least d5=100 mm to inference-free lines, as well as
to signal cables and signal lines
(alternative separated by a grounded distance plate)
●
in separate cable ducts, if possible
Routing the Motor Power Cables
and Mains Connection Lines
For converters (drive controllers with individual mains connection), route mo‐
tor power cables and (unfiltered) mains connection lines in parallel for a maxi‐
mum distance of 300 mm. After that distance, route motor power cables and
power supply cables in opposite directions and pre
Ground connections
Housing and Mounting Plate
By means of appropriate ground connections, it is possible to avoid the emis‐
sion of interference, because interference is discharged to ground on the
shortest possible way.
Ground connections of the metal housings of EMC-critical components (such
as filters, devices of the drive system, connection points of the cable shields,
devices with microprocessor and switching power supply units) have to be
well contacted over a large surface area. This also applies to all screw con‐
nections between mounting plate and control cabinet wall and to the mount‐
ing of a ground bus to the mounting plate. The best solution is to use a zinc-
coated mounting plate. Compared to a lacquered plate, the connections in
this area have a good long-time stability.
Connection Elements
For lacquered mounting plates, always use screw connections with tooth lock
washers and zinc-coated, tinned screws as connection elements. At the con‐
nection points, remove the lacquer so that there is safe electrical contact over
a large surface area. You achieve contact over a large surface area by
means of bare connection surfaces or several connection screws. For screw
connections, you can establish the contact to lacquered surfaces by using
tooth lock washers.
Metal Surfaces
Always use connection elements (screws, nuts, plain washers) with good
electroconductive surface.
Bare zinc-coated or tinned metal surfaces have good electroconductive prop‐
erties.
Anodized, yellow chromatized, black gunmetal finish or lacquered metal sur‐
faces have bad electroconductive properties.
Ground Wires and Shield Connec‐
tions
For connecting ground wires and shield connections, it is not the cross sec‐
tion but the size of contact surface that is important, as the high-frequency in‐
terference currents mainly flow on the surface of the conductor.
Always connect cable shields, especially shields of the motor power cables,
to ground potential over a large surface area.
Installing signal lines and signal cables
Line Routing
For measures to prevent interference, see the Project Planning Manuals of
respective device. In addition, we recommend the following measures:
●
Route signal and control lines separately from the power cables with a
minimum distance of d5=100 mm (see
"Division into areas (zones)" on
) or with a grounded separating sheet. The optimum way is to
route them in separate cable ducts. If possible, lead signal lines into the
control cabinet at one point only.
DOK-RCON02-FV*********IB01-EN-P
Rexroth Frequency Converter Fv
Bosch Rexroth AG
159/219
Technical Data
Содержание Fv Series
Страница 20: ...Bosch Rexroth AG DOK RCON02 FV IB01 EN P Rexroth Frequency Converter Fv 18 219...
Страница 30: ...Bosch Rexroth AG DOK RCON02 FV IB01 EN P Rexroth Frequency Converter Fv 28 219...
Страница 34: ...Bosch Rexroth AG DOK RCON02 FV IB01 EN P Rexroth Frequency Converter Fv 32 219...
Страница 52: ...Bosch Rexroth AG DOK RCON02 FV IB01 EN P Rexroth Frequency Converter Fv 50 219...
Страница 58: ...Bosch Rexroth AG DOK RCON02 FV IB01 EN P Rexroth Frequency Converter Fv 56 219...
Страница 144: ...Bosch Rexroth AG DOK RCON02 FV IB01 EN P Rexroth Frequency Converter Fv 142 219...
Страница 164: ...Bosch Rexroth AG DOK RCON02 FV IB01 EN P Rexroth Frequency Converter Fv 162 219...
Страница 180: ...Bosch Rexroth AG DOK RCON02 FV IB01 EN P Rexroth Frequency Converter Fv 178 219...
Страница 214: ...Bosch Rexroth AG DOK RCON02 FV IB01 EN P Rexroth Frequency Converter Fv 212 219...
Страница 216: ...Bosch Rexroth AG DOK RCON02 FV IB01 EN P Rexroth Frequency Converter Fv 214 219...
Страница 220: ...Bosch Rexroth AG DOK RCON02 FV IB01 EN P Rexroth Frequency Converter Fv 218 219...
Страница 221: ...Notes DOK RCON02 FV IB01 EN P Rexroth Frequency Converter Fv Bosch Rexroth AG 219 219...