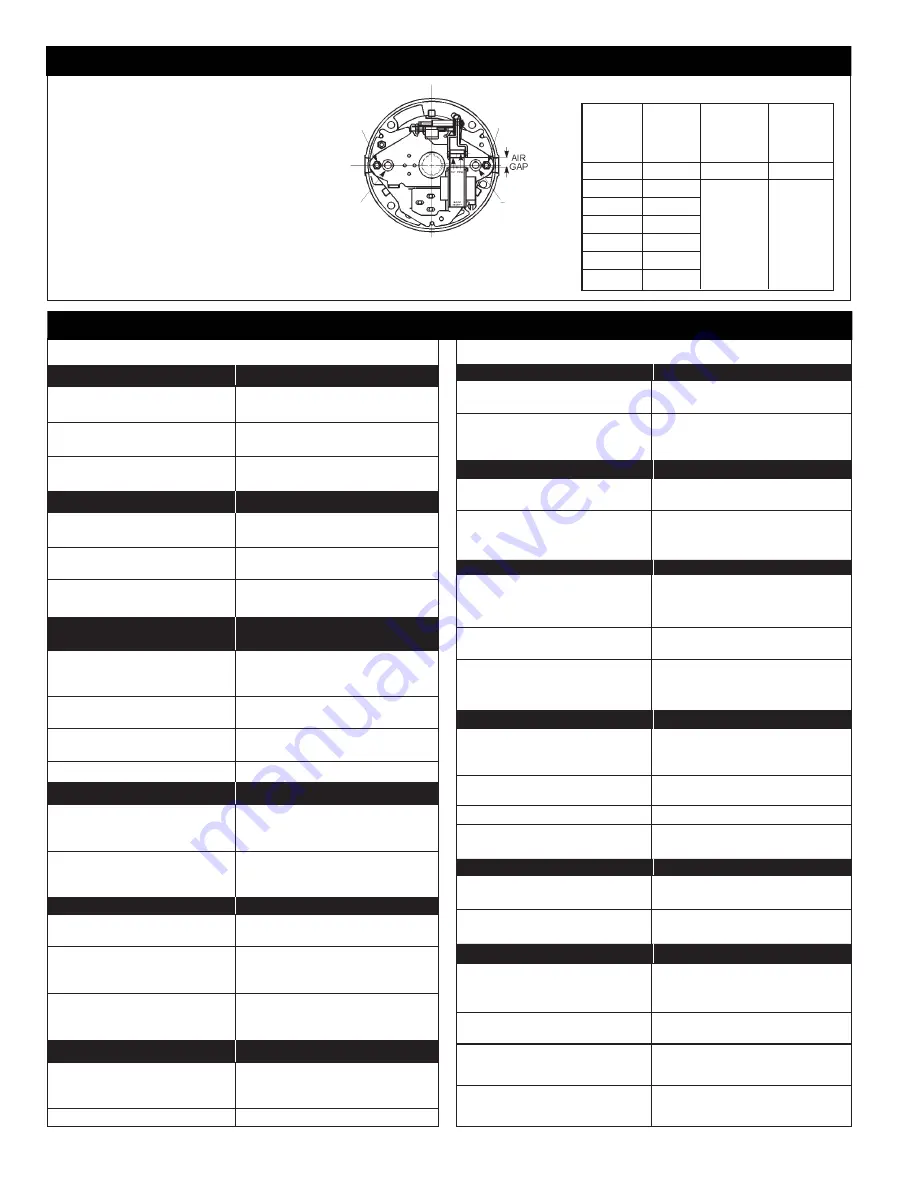
Torque Adjustment
Brake is factory set for nominal rated static
torque which is maximum torque. Torque
may be decreased up to 50% for increased
stopping times up to 2 second stop time.
The torque on the 1-1/2 lb-ft brake may not
be reduced.
Turn both spring adjustment screws (11),
Figure 6, equal amounts counterclockwise
to decrease torque. See Table A for torque
reduction permissible amounts.
11
11
10
10
Figure 6
Nominal Original Maximum
% Torque
Static
Spring Counter- Reduction
Torque
Height clockwise
per
(lb-ft) (inches) Turns
Turn
1-1/2
1.69”
- -
3
1.47”
6
1.47”
10
1.53”
5-1/2
9%
15
1.53”
20
1.53”
25
1.47”
TABLE A
COIL FAILURE
SUPPLY VOLTAGE CAUSE
SUPPLY VOLTAGE CORRECTION
Line voltage >110% of coil rating
Reduce voltage or replace with
proper rated coil
AC input on a DC coil
Replace rectifier or replace with
proper rated coil.
Excessive voltage drop during
inrush time
Increase current rating of power
supply.
WIRING CAUSE
WIRING CORRECTION
Leadwires interfering with plunger
pull-in
Reroute wiring away from plunger
and other moving components.
Excessive voltage drop during
inrush time
Increase leadwires size from power
supply
Coil leadwire shorted to ground
Replace coil or leadwire and protect
with wire sleeving
SOLENOID ASSEMBLY CAUSE
SOLENOID ASSEMBLY
CORRECTION
Plunger not seating flush against
solenoid frame
Loosen solenoid mounting screws
and reposition frame to allow full
face contact
Plunger cocked in coil preventing
pull-in
Realign solenoid frame
Excessive solenoid/plunger wear
at mating surface
Replace solenoid assembly
Broken shading coils
Replace solenoid assembly
WORN PARTS CAUSE
WORN PARTS CORRECTION
Excessive wear of solenoid link
arm and/or shoulder bolt
Replace link arm and link bolt; also
inspect plunger thru-hole for
elongation
Plunger guides worn down and
interfering with plunger
movement
Replace guides
APPLICATION CAUSE
APPLICATION CORRECTION
Machinery cycle rate is exceeding
brake rating
Reduce brake cycle rate or use
alternate control method
High ambient temperature
(>110%) and thermal load
exceeding coil insulation rating
Use Class H rated coil and /or find
alternate method of cooling brake
Brake coil wired with windings of
an Inverter motor or other
voltage/current limiting device
Wire coil to dedicated power source
with instantaneous coil rated voltage
MISCELLANEOUS CAUSE
MISCELLANEOUS CORRECTION
Wrong or over tightened torque
Replace with proper spring or refer
to Installation section for proper
spring height
Excessive air gap
Reset, refer to Installation Section 4
EXCESSIVE WEAR / OVERHEATING
AIR GAP CAUSE
AIR GAP CORRECTION
Low solenoid air gap
Reset air gap (refer to Air Gap
Adjustment)
Disc pack dragging
Inspect endplate, hub and discs for
dirt, burrs, wiring and other sources
of interference preventing disc “float”
CYCLE RATE CAUSE
CYCLE RATE CORRECTION
Brake “jogging” exceeding coil
cycle rate
Reduce cycle rate or consider
alternate control method
Thermal capacity is being
exceeded
Reduce cycle rate, use alternate
control method or increase brake
size
ALIGNMENT CAUSE
ALIGNMENT CORRECTION
Broke endplate not concentric to
motor C-Face
Motor register must be within
.004” on concentricity.
Motor shaft runout is excessive
Must be within .002”; runout;
consult motor manufacturer
Brake is being operated on a
incline greater than 15° above or
below horizontal
Vertical separator springs must be
used to prevent discs from
becoming cocked
WORN PARTS CAUSE
WORN PARTS CORRECTION
Friction disc excessively worn
(disc can wear to 1/2 original
thickness or .093”)
Replace friction discs.
Endplate, stationary disc or
pressure plate warped
Replace warped or worn component
Linkages and/or pivot pins worn
Replace all worn components
Motor shaft endfloat excessive
Endfloat must not exceed .020”;
consult motor manufacturer
HUB CAUSE
HUB CORRECTION
Burr on hub interfering with disc
“float”
File off burr
Set screw backed out and
interfering with disc
Retighten set screw; use Loctite®
242 to help secure
MISCELLANEOUS
MISCELLANEOUS
Solenoid plunger not pulling
completely
Check line voltage (±10% of
nameplate rating) or replace worn
solenoid assembly
Wiring is restricting disc pack
movement
Reroute wiring
Excessive stop time
(2 seconds or greater)
Increase brake size/torque or use
alternate control method
High Ambient temperature
(in excess of 110°F)
Reduce cycle rate or use alternate
method of cooling
TROUBLESHOOTING
Rexnord Industries, LLC, Stearns Division, 5150 S. International Dr., Cudahy, WI 53110, (414) 272-1100 Fax: (414) 277-4364 www.stearns.rexnord.com
TORQUE ADJUSTMENT
BACK TO PRODUCT PAGE