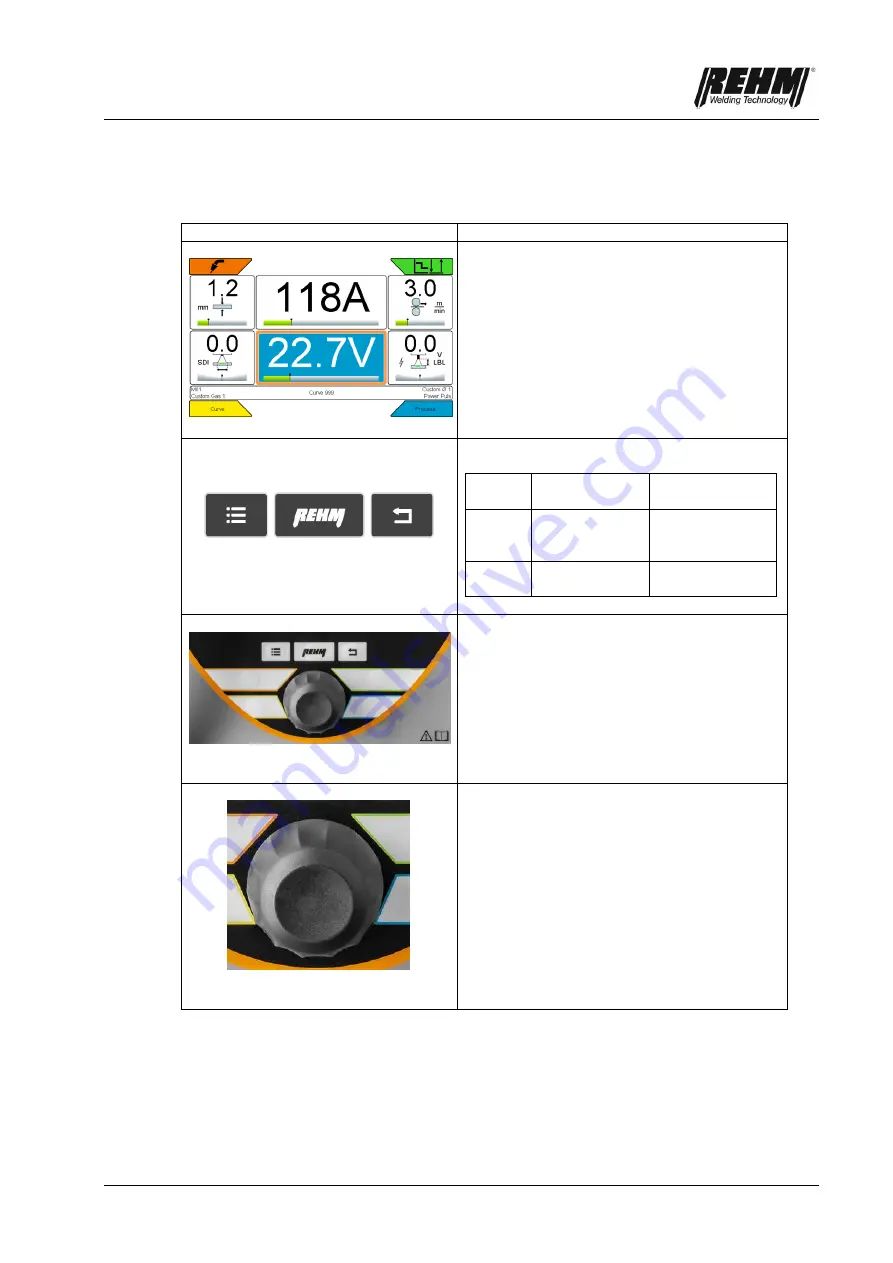
Function description
19
4.2 Control panel description
4.2.1 Operating elements
Controls
Function
Fig. 7 Main screen
Main screen
Operation via rotary encoder with push-
knob and buttons for menu selection in
the 4 corners of the screen
Fig. 8 Function buttons
Function buttons (from left to right)
Button
Submenu
“Submenu”
List of all
submenus
Button
Main screen
“Home”
Jumps directly
to the first
screen page
Button
Back
“Back”
Always jumps
back one level
Fig. 9 Corner function buttons
Corner menu selection buttons
Direct menu buttons for the selection
menus located in the 4 screen corners;
arranged around the rotary encoder.
Fig. 10 Rotary encoder with push-
knob
Rotary encoder with push-knob
Moves the pointer (cursor) on the
screen clockwise or counter clockwise.
Positions reached are highlighted in
colour and are activated by pressing
the rotary encoder knob.
Содержание FOCUS.ARC P 250
Страница 1: ...GB OPERATING INSTRUCTIONS MIG MAG impulse welding systems FOCUS ARC P 250 450...
Страница 15: ...Function description 15 Figure 4 FOCUS ARC P 450 Rear view Figure does not illustrate standard equipment...
Страница 16: ...Function description 16 Figure 5 FOCUS ARC P wire feed case...
Страница 37: ...Function description 37 Figure 20 Submenu MSG parameters...
Страница 67: ...Circuit diagrams 67 14 Circuit diagrams Figure 28 FOCUS ARC P current source...
Страница 68: ...Circuit diagrams 68 Figure29 FOCUS ARC P wire feed case...
Страница 69: ...Circuit diagrams 69 Figure30 FOCUS ARC P water cooling...
Страница 73: ...Components 73...
Страница 74: ...Components 74...
Страница 75: ...Components 75...
Страница 76: ...Components 76...
Страница 81: ......