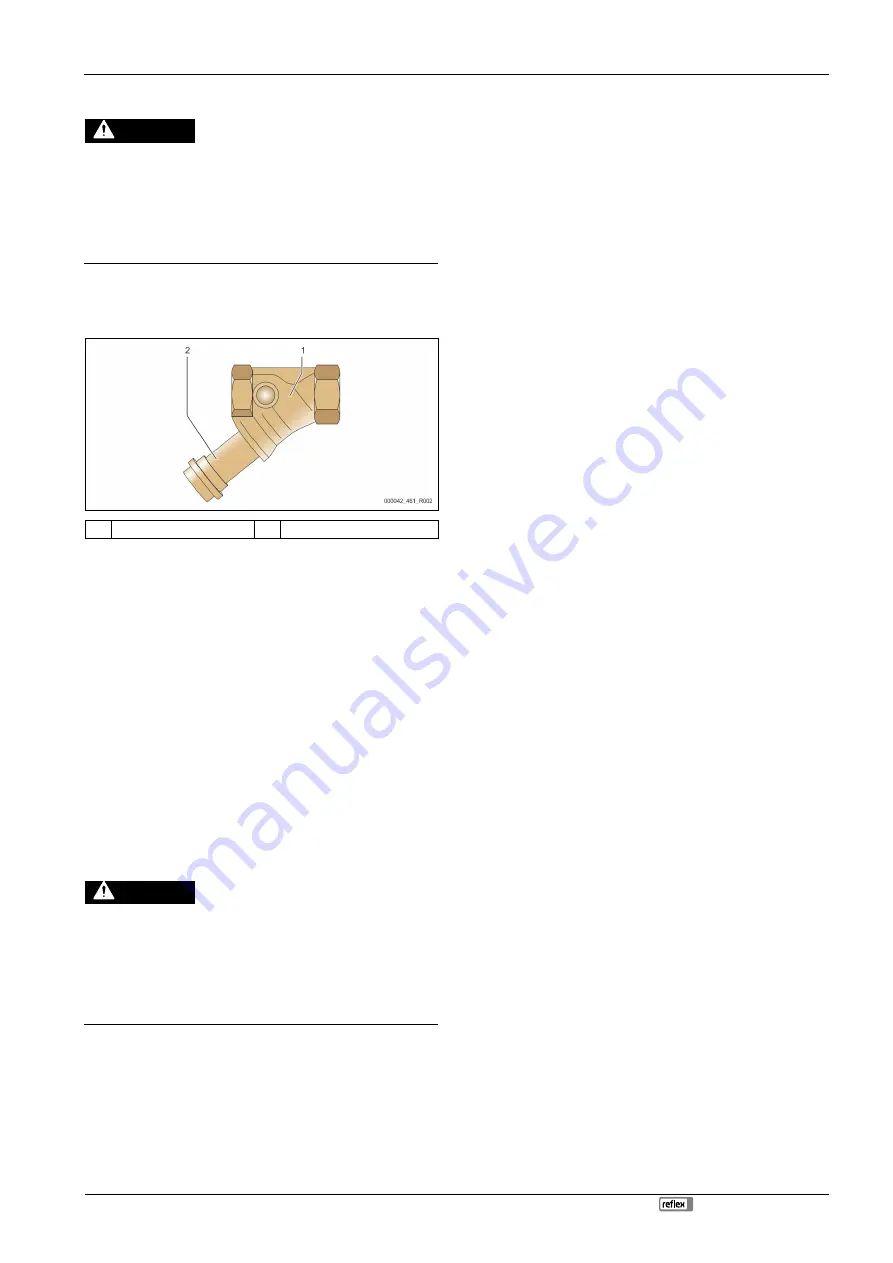
Maintenance
Variomat Basic
—
22.07.2020 - Rev.
A
English
—
25
11.1.1
Cleaning the dirt trap
CAUTION
Risk of injury due to pressurised liquid
If installation, removal or maintenance work is not carried out
correctly, there is a risk of burns and other injuries at the connection
points, if pressurised hot water or hot steam suddenly escapes.
•
Ensure proper installation, removal or maintenance work.
•
Ensure that the system is de-pressurised before performing
installation, removal or maintenance work at the connection
points.
The "ST" dirt trap must be cleaned after the expiry of the continuous
degassing time at the latest. An inspection is also required after longer
lasting operation.
1
"ST" dirt trap
2
Dirt trap insert
1.
Switch to Stop mode.
2.
Close the ball vales upstream of the "ST" dirt trap (1) and the
primary vessel.
3.
Slowly unscrew the dirt trap insert (2) from the dirt trap in order
for the residual pressure to escape from the pipeline segment.
4.
Pull the mesh from the dirt trap insert and rinse it with clear
water. Use a soft brush for cleaning.
5.
Re-insert the mesh into the dirt trap insert, check the gasket for
damage, and screw the dirt trap insert back into the housing of the
"ST" (1) dirt trap.
6.
Open the ball valve upstream of the "ST" dirt trap (1) and ball valve
to the primary vessel.
7.
Vent the "PU“ pump, see chapter
page 18 .
8.
Switch to Automatic mode.
Note!
Clean all other installed dirt traps (in the Fillset, for example).
11.1.2
Cleaning the tanks
CAUTION
Risk of injury due to pressurised liquid
If installation, removal or maintenance work is not carried out
correctly, there is a risk of burns and other injuries at the connection
points, if pressurised hot water or hot steam suddenly escapes.
•
Ensure proper installation, removal or maintenance work.
•
Ensure that the system is de-pressurised before performing
installation, removal or maintenance work at the connection
points.
Clean the primary tank and the secondary tanks from sludge deposits.
1.
Switch to Stop mode.
2.
Empty the tanks.
–
Open the "FD" feed and drain cocks and empty the tanks
completely from water.
3.
Remove the hose connection between the primary tank and the
device and the secondary tank, if provided.
4.
Remove the lower vessel covers from the tanks.
5.
Remove any sludge from the covers and the spaces between the
diaphragms and the tanks.
•
Check the diaphragms for tearing.
•
Check the tank interior walls for corrosion.
6.
Reinstall the covers on the tanks.
7.
Reinstall the flange connection betweens the primary tank and the
device and the secondary tank, if provided.
8.
Close the "FD" feed and drain cocks at the tanks.
9.
Use the "FD" feed and drain cock to fill the primary tank with
water, see chapter 8.4 "Filling the tanks with water" on page 18 .
10. Switch to Automatic mode.
11.2
Checking switching points
Prerequisite for checking the switching points are the following correct
settings:
•
Minimum operating pressure P
0
, see chapter 11.1.2 "Cleaning the
•
Level sensor at the primary tank.
Preparation
1.
Switch to Automatic mode.
2.
Close the cap valves upstream of the tanks and the "EC" expansion
lines.
3.
Record the displayed filling level (value in %).
4.
Drain the water from the tanks.
Checking the cut-in pressure
5.
Check the cut-in and cut-out pressure of the "PU" pump.
–
The pump cuts in at P
0
+ 0.3 bar.
–
The pump cuts out at P
0
+ 0.5 bar.
Checking the Make-up "On"
6.
If necessary, check the make-up value displayed at the controller.
–
The automatic make-up is activated at a level display of 20 %.
Checking Insufficient water "On"
7.
Switch off the make-up and continue to drain water from the
tanks.
8.
Check the displayed value for the "Insufficient water" filling level
message.
–
Insufficient water "On" is displayed at the controller at a
minimum filling level of 5 %.
9.
Switch to Stop mode.
10. Switch off the main switch.
Cleaning the tanks
If necessary, remove condensate from the tanks, see chapter 10.2.2
"Default settings" on page 22 .
Activating the device
11. Switch on the main switch.
12. Activate the make-up.
13. Switch to Automatic mode.
–
Depending on the filling level and pressure, the "PU" pump
and the automatic make-up will be switched on.
14. Slowly open the cap valves upstream of the tanks and secure them
against unintended closing.
Checking Insufficient water "Off"
15. Check the displayed value for the Insufficient water "OFF" filling
level message.
–
Insufficient water "Off" is displayed at the controller at a
minimum filling level of 7 %.
Checking Make-up "Off"
16. If necessary, check the make-up value displayed at the controller.
–
Automatic make-up is deactivated at a level display of 25 %.
Maintenance is completed.