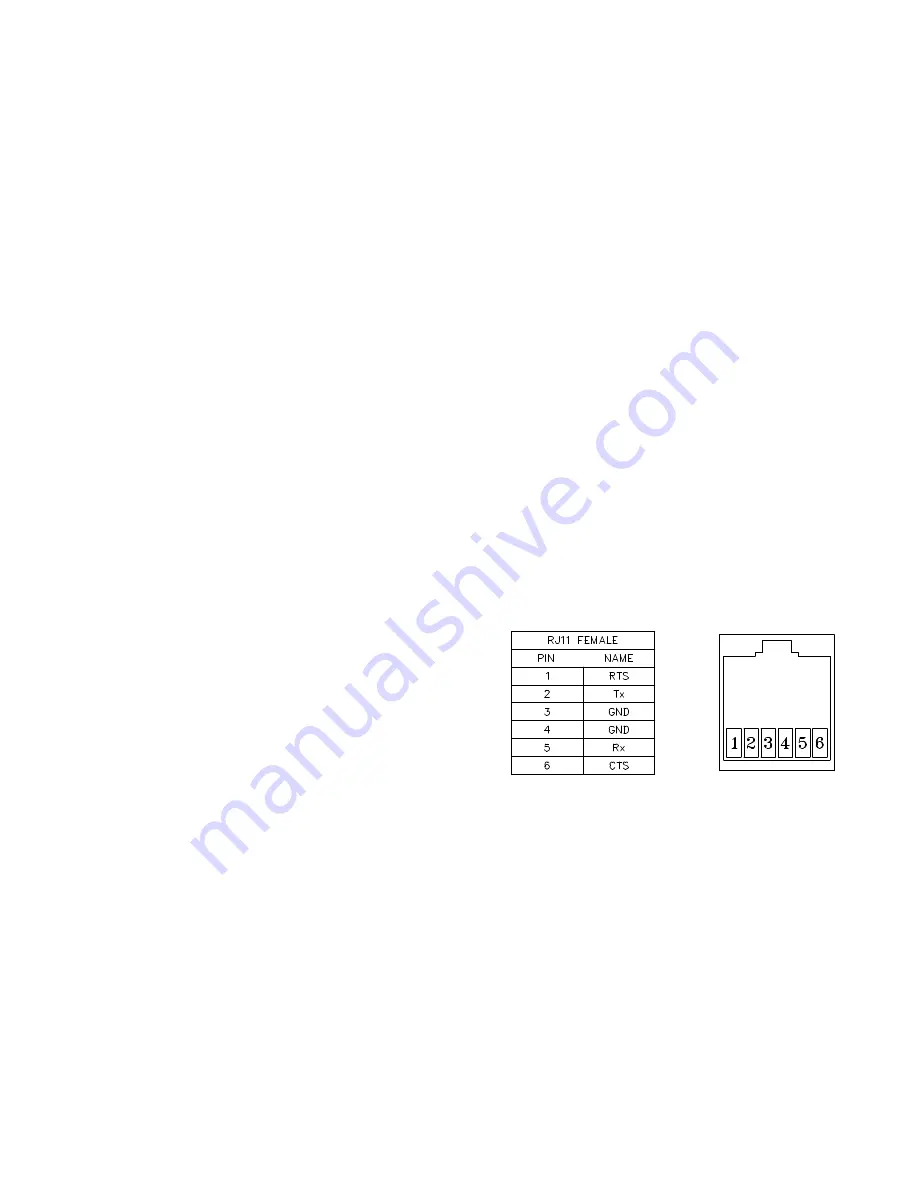
HARDWARE INFORMATION
This bulletin contains a variety of information related to the installation and
operation of the Operator Interface supplied. Ideally, you should read this
document thoroughly before attempting to use the equipment. For information
about the software aspects of the terminal, please consult other documentation.
CONTENTS OF PACKAGE
The Operator Interface is supplied in a packaging box containing the
following...
u
The interface terminal itself.
u
A NEMA 4/IP65 rated mounting gasket.
u
A bag containing panel hardware.
u
This hardware bulletin.
u
If any of these items is missing, please contact your supplier
immediately.
POWER SUPPLY REQUIREMENTS
The Operator Interface requires a 24 V power supply rated at 0.5 A unless
otherwise stated on the label.
u
The Operator Interface requires a power supply capable of supplying a
current of 500 mA at a regulated voltage of 24 V. Supplies providing
between 18 V and 30 V are also suitable.
u
The terminal may take as little as 100 mA in certain circumstances, so
be sure that the chosen power supply can operate correctly with this
load. Large switch-mode supplies tend to need a certain minimum load
before they will operate correctly.
In any case, it is very important that the power supply is mounted correctly if
the unit is to operate reliably. A very high proportion of reported problems are
caused by incorrect power supply installation, so please take care to observe the
following points...
u
The power supply must be mounted close to the unit, with usually not
more than 6 feet of cable between the supply and the Operator Interface.
Ideally, as short a length as is possible should be used. In particular, the
power supply should not be mounted on the back of the panel when the
Operator Interface is installed in the panel door unless a short cable run
can be achieved.
u
The wire used to connect the Operator Interface’s power supply should
be of at least 22 gauge wire. If a longer cable run is used, you should
use even thicker cable. The routing of the cable should be kept away
from large contactors, inverters and other devices which may generate
significant electrical noise.
BATTERY BACKUP ISSUES
The Operator Interface is supplied with a Lithium Battery designed to
maintain the internal memory and real-time clock during power outages.
Assuming the operator interface terminal is powered up for 50% of the time,
this battery should last over 4 years. A “Battery Low” system variable is
available so that the programmer can choose specific action(s) to occur when
the battery voltage drops below its nominal voltage.
It is possible to replace the battery without losing the contents of the Operator
Interface’s memory, but this does not reduce the importance of ensuring that a
copy of the terminal’s configuration is kept readily at hand to allow the terminal
to be re-loaded in the case of mishaps. Please remember that it is not possible to
extract the contents of a terminal for subsequent re-loading, so the importance
of keeping a copy on disk cannot be over stressed.
CHANGING THE BATTERY
To change the internal battery, follow these steps...
u
Remove the power and PLC communications connector from the unit.
u
Remove the four screws from the rear-cover.
u
Remove the cover, ensuring that the right-hand edge is raised first to
avoid fouling the earth stud. You may have to pivot the cover to an
angle of about 30°to achieve this.
u
If you wish to avoid losing the terminal’s configuration, reconnect the
power connector and re-apply power. Note that this will require the
panel to be powered-up and, as such, only suitably qualified staff should
carry out this procedure.
u
The battery is located in a holder on the main circuit board. This should
be clearly visible. Remove the battery from its holder.
u
Place the new battery in the holder. The terminal’s power supply can
now be disconnected, if you re-applied power in the step above.
u
Replace the lid, screws and connector by following the above procedure
in reverse. You may like to make a note of the date the battery was
replaced to allow planned maintenance to be carried out.
u
If you did not keep the unit powered-up during battery replacement, hold
down the EXIT and MUTE keys on the keyboard and remove and then
re-apply power. This will clear the internal memory and thus the suitable
configuration database should then be re-loaded.
Please note that the old battery must be disposed of in a manner which
complies with your local waste regulations. Also, the battery must not be
disposed of in fire or in a manner whereby it may be damaged and its contents
come into contact with human skin.
INSTALLATION & CONNECTIONS
The unit meets NEMA 4/IP65 requirements for indoor use, when properly
installed. The units are intended to be mounted into an enclosed panel.
Installation Environment
The unit should be installed in a location that does not exceed the maximum
operating temperature and provides good air circulation. Placing the unit near
devices that generate excessive heat should be avoided.
Continuous exposure to direct sunlight may accelerate the aging process of
the bezel. The bezel should be cleaned only with a soft cloth and neutral soap
product. Do NOT use solvents.
Do not use tools of any kind (screwdrivers, pens, pencils, etc.) to operate the
keypad of the unit.
CONNECTING TO A PLC
The Operator Interface is designed to operate with a PLC. A serial
communication connection must be made between the operator interface
terminal and PLC, and the details of this connection vary according to which
PLC is used.
The following section lists the connection details for the PLC to be used .
PLC TYPE
Details on how to connect to most PLCs are available on request from RLC.
CONNECTING TO AN IBM PC/AT
The Operator Interface is programmed via software running on an IBM
PC/AT or a compatible computer. The connection between the PC/AT and the
operator interface terminal is made via a custom cable provided with the EDICT
Developer’s Kit. The cable is designed for a 9-way serial port. Please contact
your supplier if you require a 25-way version.
PROGRAMMING PORT PIN OUT
The Operator Interface’s programming port is sometimes used to connect
other RS-232 devices, such as printers. The following illustration and table
gives the pin-out of this port to enable such connections to be made.
The above table denotes the pin names of the programming port. When
connecting, the pin name at the programming port is connected to the opposite
of that pin name at the destination device.
MOUNTING INSTRUCTIONS
The Operator Interfaces are designed for through-panel mounting. A
neoprene gasket is provided, to enable sealing to NEMA 4/IP65 specification.
The panel cut-out diagram for the model supplied is provided. All mounting
holes should be drilled for 0.14” clearance. Care should be taken to remove any
loose material from the mounting hole to avoid such metal falling into the
Operator Interface itself during installation.
FUNCTION KEY STRIPS
The function keys on the Models CL-10, CL-20, CX-100, and CX-200, have
clear windows that permit the user to insert labels appropriate to the process. A
formatted page is supplied upon which the user can enter function names (e.g.
RUN, PRINT, etc.). These strips are inserted from the rear of the panel through
slots below the function keys located underneath the gasket.
Take care that the ink applied will not rub off of the paper, or else blemishes
will be left on the inside of the window. Laminated paper or plastic film can
prove easier to insert than normal photocopier paper. It also helps if the starting
edge of the paper has about 0.25 inches of its corners cut off at a 45 degree
angle.
Note: Add an additional 1.5” to label length to allow for easier insertion and
removal.
3
AUDIN - 8, avenue de la malle - 51370 Saint Brice Courcelles - Tel : 03.26.04.20.21 - Fax : 03.26.04.28.20 - Web : http: www.audin.fr - Email : [email protected]