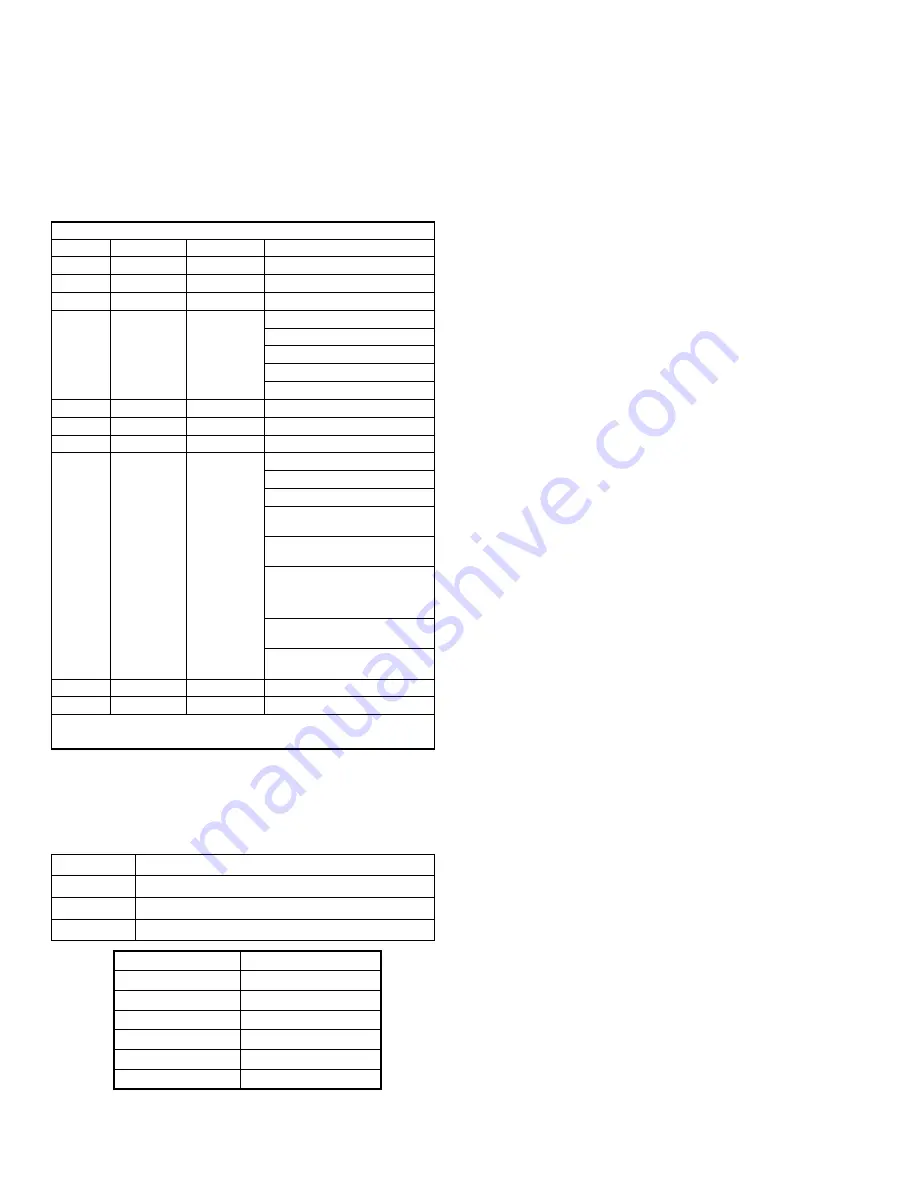
For Sales and Support, Contact Walker EMD • Toll-free: (800) 876-4444 • Tel: (203) 426-7700 • Fax: (203) 426-7800 • www.walkeremd.com
4
SERIAL PROGRAMMING
Before communication can take place, the Apollo must be programmed to the
same baud rate as the connected equipment. In addition, a loop address and print
options, if the print request terminal is to be used, may be programmed. If only
one Apollo is being used, an address of zero may be used. If more than one
Apollo is being used, assignment of unique addresses, other than zero, for each
Apollo is recommended. Valid addresses of 0 to 9 may be assigned, however,
the Apollo’s internal current source is capable of driving only 7 units on the
loop. Additional drive capability may be afforded by an external current source
with a higher voltage compliance
(ie. >15 VDC)
.
Following the procedure outlined in SET-UP and CALIBRATION, press the
buttons indicated in the following chart and observe the indicated display.
SENDING COMMANDS TO THE APLTC
When sending commands to the Apollo, a command string must be
constructed. The command string may consist of command codes, value
identifiers and numerical data. Below is a table outlining the codes and
identifiers the Apollo will recognize.
The command string is constructed by using the above commands and
identifiers along with any data values that are required. The Apollo will accept
+ or - sign in front of the data value, however unsigned numbers are understood
to be positive. Leading zeros can be eliminated and both upper and lower case
characters are accepted. The address command is used to allow a command to
be directed to a specific unit in the serial loop. Whenever the unit address is
zero, transmission of the address command is not required. This is done for
applications which require only one Apollo in the loop. For applications which
require several units, it is necessary that each Apollo be given unique addresses
so that each unit can be individually accessed.
The command string is constructed in a specific logical sequence. The Apollo
will reject command strings that do not conform. Only one operation can be
performed per command string. Below is a description of how to construct a
command string.
1. If the Apollo has an address other than zero, the first two characters of the
string must consist of the address command
(N)
and the address number of
the unit.
2. The next two characters in the string are the actual command that the Apollo
must perform and the identifier on which it operates.
3. If the change command
(V)
is being used, the next characters in the string,
after the value identifier, are the numerical data.
4. All commands must be terminated by an asterisk
(*)
. Carriage return and line
feed characters are not valid terminators and should be suppressed
(ie, in
BASIC, use semicolon after print statement)
.
EX. 1:
Have the Apollo with address of 3 transmit thermocouple temperature.
N3T*
EX. 2:
Have the Apollo with address of 0 change the high alarm value to 800
degrees.
VC800*
(Note that degrees correspond to the current temperature scale.)
EX. 3:
Have the Apollo with address of 0 and a Print Select Options
(PSEL)
of
6, transmit the T.C. Temperature, Alarm Values & Hysteresis Values.
TP*
As shown, all commands must be terminated with a “command terminator”(*).
The Apollo will not process the command until the terminator is sent. If illegal
commands or characters are sent to the Apollo, they still would need to be
terminated by an (*), so the unit could reset its receive buffer. When sending a
command under BASIC, be sure to terminate the PRINT statement with a
semicolon to suppress sending carriage return and linefeed characters (ex.PRINT
“TA*”;). The Apollo does not have a response for an illegal command.
Allow 800 msec for the Apollo to respond to either commands or hardware
print requests before sending another command. If a command is sent during
this period, the transmitted data may be invalid. Since the receive channel into
the Apollo is monitored and used as (DTR), current must be flowing through it
(mark condition) before transmission will commence.
STEP
CAL. BUTTON
SEL. BUTTON
DISPLAY
A
X 10 secs.
CAL
0
B
X
CAL
3
C
X
D
X
0 - Disable Comm.
1 - 300, 2 - 600
3 - 1200, 4 - 2400
E
X
F
X
G
X
H
X
0 - No Print
1 - Print TC Temp.
5 - Print TC Temp., and
Alarm Values
6 - Print TC Temp., Alarm
Values, & Hysteresis
I
X
CAL
0
J
X
bAud
X
(Current Rate)
bAud
X
(Desired Rate)
BAUD RATE CODE
Addr
X
(Current Addr.)
Addr
X
(desired Addr.0 thru 9)
PSEL
X
(Current PCode)
PSEL
X
(Desired PCode)
888.8
8
Then TC Disp.
*
2 - Print Cold
Junction Temp.
3 - Print Alarm
Values
4 - Print TC Temp.,
Cold Junction
Temp. & Alarm
Values
CAL 3 SERIAL COMMUNICATION PROGRAMMING
*
It is not necessary to exit to the thermocouple display if further set-up or calibration are
required, just press the “SEL” button. While in CAL
0
, select the desired CAL #.
COMMAND
FUNCTION
(T)
(V)
(N)
address a particular Apollo in a multiple unit loop
change the requested value specified by identifier (C, D, & E)
transmits the requested information specified by identifier
FUNCTION
A
T/C temperature
B
Cold jct. temp.
C
Alarm high
D
Alarm low
E
Hysteresis
P
Print Select
VALUE IDENTIFIER