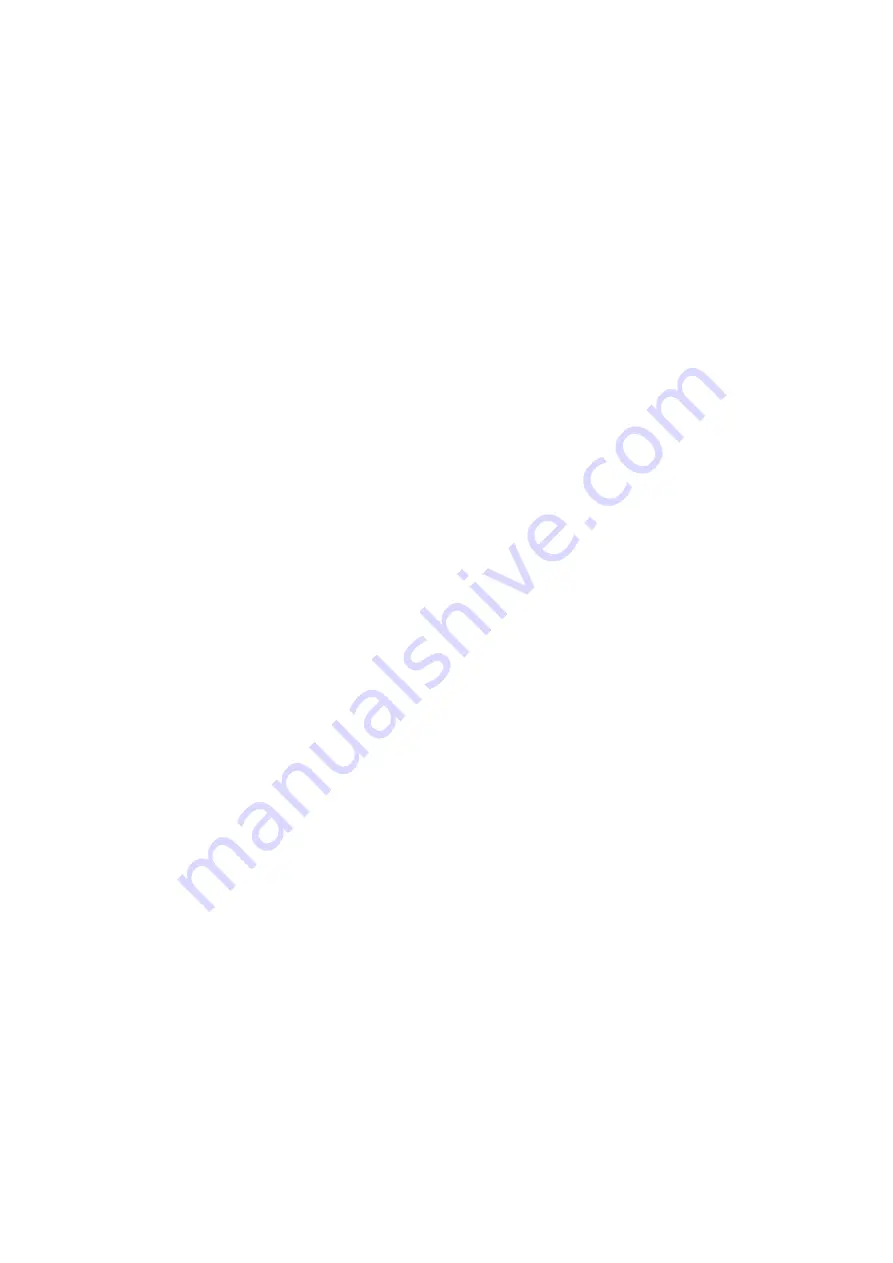
6
1.3 Additional Health & Safety for Woodturning Lathes
Safe Operation
Familiarise yourself with the machine
• Machining operations using wood turning lathes have a history of
serious accidents. Most serious accidents resulted from the work piece
being thrown from the lathe whilst turning. Other accidents can be
caused by loose clothing being drawn in to the rotating work piece or
hands becoming trapped between the rotating work piece and fixed
parts of the lathe.
2. Before switching the machine ‘ON’
• Before attaching a work piece to a faceplate, always prepare it to be as
round as possible. This will minimise vibration whilst turning. For further
instructions please see the section of this manual entitled
Intended
Use of the Lathe & Basic Woodturning Instructions
.
• Adjust the tool rest to the correct height and distance from the work
piece and check that all fixings are secure.
• Check that the size of the work piece is within the safe working capaci-
ties of the lathe as detailed in the manual.
• Select the correct speed according to the size and type of work piece.
The slowest speed is the safest speed to start any new work piece.
• Always rotate the work piece by hand before starting the lathe to en-
sure it does not come into contact with the tool rest. If the work piece
strikes the tool rest during operation, it could be split and thrown from
the lathe.
• When using a faceplate always ensure the work piece is well secured
with screws of a suitable diameter and length.
• Remove any loose knots and bark from the work piece before mounting
it to the lathe.
• If mounting a work piece between centres, always ensure that the
tailstock is correctly adjusted and fully secure. Check that the locking
handle for the tailstock barrel is fully tightened.
3. Whilst using the lathe
• Do not allow the turning tool to dig in to the work piece, which could
result in the work piece splitting or being thrown from the lathe. Al-
ways position the tool rest at the correct height. For further instructions
please see the section of this manual entitled
Intended Use of the
Lathe & Basic Woodturning Instructions
.
• Before starting to machine a work piece that is off centre or not
perfectly round, always set the machine to the slowest speed and
gradually increase speed as the work piece becomes more balanced as
material is removed. Running the lathe too fast could cause the work
piece to be thrown from the lathe or the turning tool to be snatched
from
your hands.
• Always store turning tools in a safe place away from the work area of
the lathe. Never reach over the rotating work piece to reach for turning
tools or accessories.
• Never attempt to adjust the position of the tool rest whilst the machine
is running. Always switch the machine ‘OFF’ and wait until the work
piece has stopped rotating before attempting any adjustments.
• Do not mount a work piece that contains excessive splits or loose knots
or bark.
• Keep firm hold and control of the turning tool at all times. Use extreme
caution when knots and voids are exposed in the work piece.
• Finish all hand sanding before removing the work piece from the lathe.
Do not exceed the speed used for the last cutting operation. For further
instructions please see the section of this manual entitled
Intended
Use of the Lathe & Basic Woodturning Instructions
.
• Do not attempt to remount a work piece that has been turned on a
faceplate unless you are deliberately turning eccentric work. You cannot
remount faceplate turned work and expect it to run true, as the timber
will have expanded or contracted.
• Do not remount a work piece that has been turned between centres
if the original centres have been altered or removed, unless you are
deliberately turning eccentric work.
• If re-mounting any work piece, always set the machine to the slowest
speed and gradually increase the speed as the work piece becomes
more balanced as material is removed.
• Use extra caution when mounting a work piece that has been turned
between centres to a faceplate, or when mounting a faceplate turning
between centres, for subsequent machining operations. Always ensure
that the lathe is set to the slowest speed before switching ON.
• Do not attempt to perform any machining operations when holding the
work piece by hand.
• Do not mount a reamer, milling cutter, wire wheel, buffing wheel, drill
bit or any other tool to the headstock spindle.
• Always ensure that the turning tool is in contact with the tool rest and
fully supported before applying the tool to the work piece.
• When the tool rest base unit is not in use (e.g. when sanding), it should
be moved away from the headstock, and the tool rest removed.
4. Maintenance
• Before attempting any maintenance and particularly when cleaning the
machine, always remove any accessories and tooling from the machine.
• Always ensure that any accessories used on the lathe are kept clean
and free from rust and deposits of resin.
• Keep all turning tools sharp and in good condition. Check that the
handles are secure and not split or damaged.
5.
This machine falls under the scope of the ‘Health & Safety at Work etc.
Act 1974’, and the ‘Provision & Use of Work Equipment Regulations
1998’. In addition the elimination or control of risks from wood dust
is included in the above regulations and the ‘Control of Substances
Hazardous to Health (COSHH) Regulations 2002’. We recommend that
you study and follow these regulations.
Further guidance is available from The Health & Safety Executive and
their website www.hse.gov.uk and from the authorised distributor in
your country (details on back cover of the manual).
1.2 General Health & Safety Guidance
determine that it will operate properly and perform its
intended function.
• Check for alignment of moving parts, binding of moving parts, breakage
of parts and any other conditions that may affect the operation of
the machine.
• A guard or other part that is damaged should be properly repaired
or replaced by a qualified person unless otherwise indicated in this
instruction manual.
• Do not use the machine if the switch does not turn the machine ‘ON’
and ‘OFF’.
• Have defective switches replaced by a qualified person.
31. Warning!
• The use of any accessory or attachment, other than those recommended
in this instruction manual, or recommended by our Company may present
a risk of personal injury or damage to the machine and invalidation of the
warranty.
32. Have your machine repaired by a qualified person
• This machine complies with the relevant safety rules and standards
appropriate to its type when used in accordance with these instructions
and with all of the standard safety guards and equipment in place. Only
qualified persons using original spare parts should carry out repairs.
Failure to do this may result in considerable danger to the user and
invalidation of warranty.
33. Caution! Motor may become hot during use
• It is normal for motors on some machines to become hot to the touch
during use. Avoid touching the motor directly when in use.