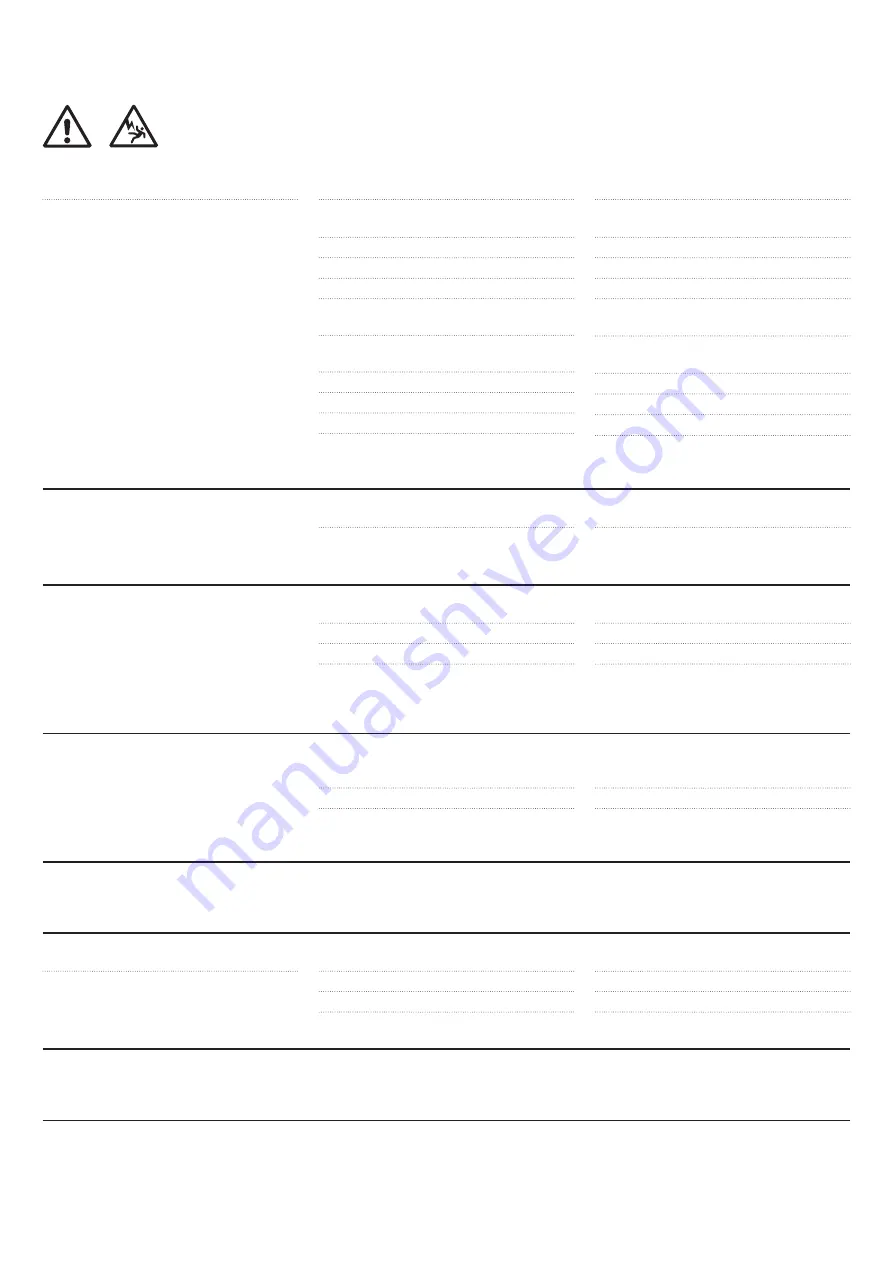
29
15. Troubleshooting
Warning: For your own safety, always turn off and unplug
the machine before carrying out any troubleshooting.
i
Kg
i
Kg
Problem
Cause
Solution
Tailstock moves when applying pressure
1. Excessive pressure is being applied by the
tailstock to the workpiece.
2. Tailstock is not secured in place.
3. Lathe bed and tailstock mating surfaces
are dirty.
1. Apply only sufficient force with the tailstock to
hold the timber securely between centres.
2. Tighten tailstock locking lever.
3. Remove and clean the tailstock and lathe bed.
Spindle stalls or will not turn.
1. Excessive depth of cut.
2. Loose or broken belt.
3. Worn spindle bearings.
4. Indexing lock is engaged.
1. Reduce cutting depth.
2. Adjust belt tension or replace drive belt.
3. Replace bearings.
4. Disengage the indexing lock and check the
spindle pulley for damage and replace
if necessary.
Motor overheats.
1. Motor overloaded.
2. Motor not cooling sufficiently.
1. Reduce load on the motor.
2. Clean the motor to increase airflow or reduce
operational periods.
Tailstock or tool rest holder will not lock in place
securely.
1. The clamp is set incorrectly.
1. Adjust the clamp as shown in the
Maintenance
chapter of the manual.
Turning tool digs into the timber or grabs it.
1. The turning tool is blunt.
2. The tool rest is set to low.
3. The tool rest is too far from the timber.
4. The wrong turning tool is being used.
1. Sharpen the turning tool.
2. Set the tool rest to the correct height.
3. Move the tool rest closer to the timber.
4. Use the correct turning tool.
Digital speed readout does not work.
1. Faulty speed readout.
1. Contact customer services in your country
for advice.
Excessive motor noise.
1. Faulty motor.
2. Pulley blind set screw is loose.
1. Replace motor.
2. Tighten blind set screw.
Machine will not start, develop full power
or stalls.
1. Machine not plugged in.
2. Low voltage.
3. Loose connection.
4. Circuit overloaded with electrical appliances.
5. Circuit too long or undersized wires.
6. Circuit breaker does not have
sufficient capacity.
7. Drive belt tension too high.
8. Extension cord is too long.
9. Worn motor.
10. Motor not cooling sufficiently.
1. Plug the machine in.
2. Check power supply to the machine.
3. Check all external connections.
4. Decrease the load on the circuit.
5. Reduce the length of the wire or use a suitable
diameter of cable.
6. Have a qualified electrician install proper sized
circuit breaker.
7. Reduce belt tension.
8. Reduce the length of the extension cord.
9. Replace motor.
10. Clean the motor to increase airflow or reduce
operational periods.
Содержание Coronet Envoy
Страница 37: ...37 ...