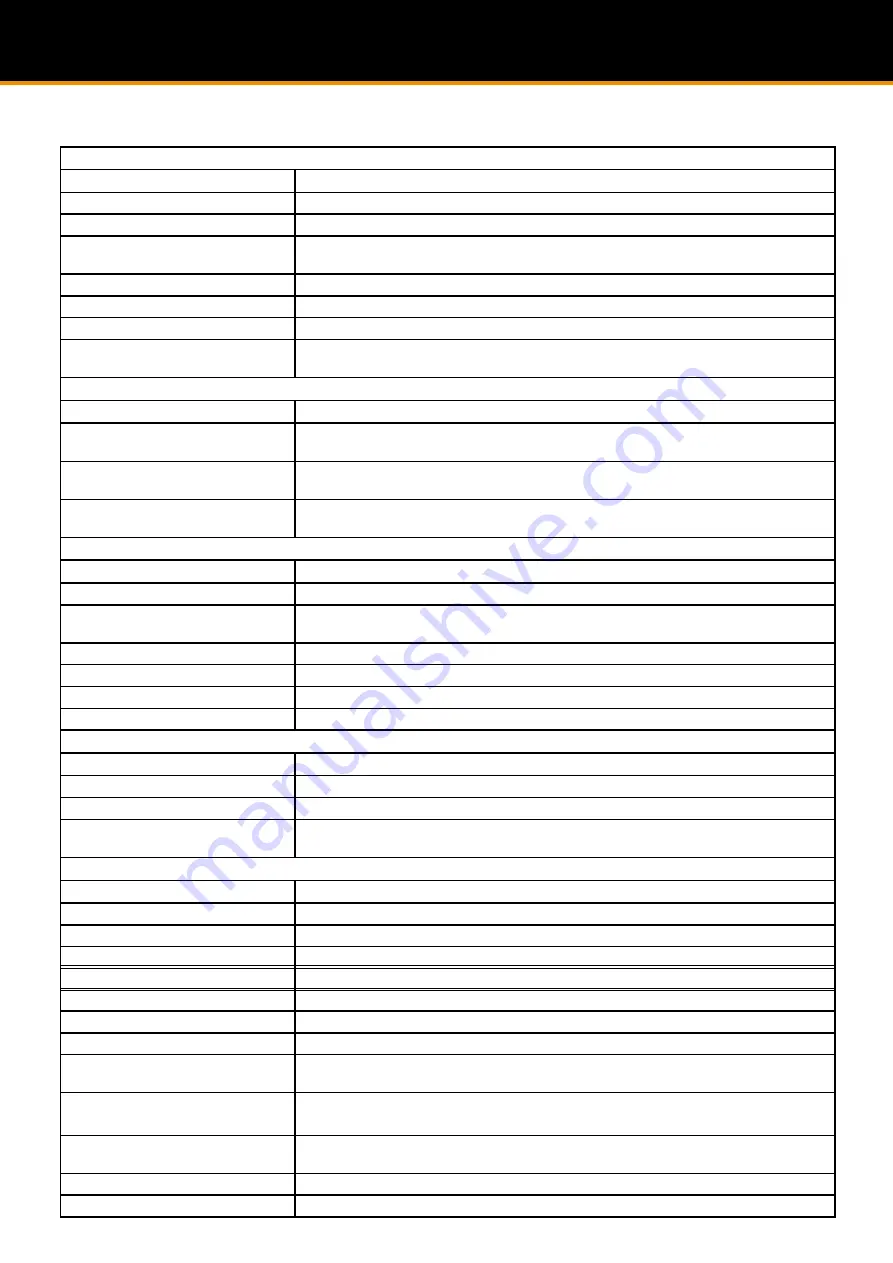
23
1: Tungsten burning away quickly
Possible Reason
Suggested Remedy
Incorrect Gas
Check that pure Argon is being used
No gas
Check the gas cylinder contains gas and is connected and the torch gas valve is open
Inadequate gas flow
Check the gas is connected, check hoses, gas valve and torch are not restricted. Set
the gas flow between 10 - 15 l/min flow rate
Back cap not fitted correctly
Make sure the torch back cap is fitted so that the o-ring is inside the torch body
Torch connected to DC +
Connect the torch to the DC- output terminal
Incorrect tungsten being used
Check and change the tungsten type if necessary
Tungsten being oxidised after weld
is finished
Keep shielding gas flowing 10–15 seconds after arc stoppage. 1 second for each 10
amps of weld current.
2: Contaminated tungsten
Possible Reason
Suggested Remedy
Touching tungsten into the weld
pool
Keep tungsten from contacting weld puddle. Raise the torch so that the tungsten is off of
the work piece 2 - 5mm
Touching the filler wire to the tung
-
sten
Keep the filler wire from touching the tungsten during welding, feed the filler wire into the
leading edge of the weld pool in front of the tungsten
Tungsten melting into the weld pool
Check that correct type of tungsten is being used. Too much current for the tungsten
size so reduce the amps or change to a larger tungsten
3: Porosity - poor weld appearance and colour
Possible Reason
Suggested Remedy
Incorrect Gas
Check that pure Argon is being used
Inadequate gas flow / gas leaks
Check the gas is connected, check hoses, gas valve and torch are not restricted. Set the
gas flow between 10 - 15 l/min flow rate. Check hoses and fittings for holes, leaks etc.,
Moisture on the base metal
Remove all moisture from base metal before welding
Contaminated base metal
Remove materials like paint, grease, oil, and dirt, including mill scale from base metal
Contaminated filler wire
Remove all grease, oil, or moisture from filler metal.
Incorrect filler wire
Check the filler wire and change if necessary
4: Yellowish residue / smoke on the alumina nozzle & discoloured tungsten
Possible Reason
Suggested Remedy
Incorrect Gas
Use pure Argon gas
Inadequate gas flow
Set the gas flow between 10 - 15 l/min flow rate
Alumina gas nozzle too small for size
of tungsten being used
Increase the size of the alumina gas nozzle
5: Unstable Arc during DC welding
Possible Reason
Suggested Remedy
Torch connected to DC +
Connect the torch to the DC- output terminal
Contaminated base metal
Remove materials like paint, grease, oil, and dirt, including mill scale from base metal.
Tungsten is contaminated
Remove 10mm of contaminated tungsten and re grind the tungsten
Arc length too long
Lower torch so that the tungsten is off of the work piece 2 - 5mm
The following chart addresses some of the common problems of DC TIG welding. In all cases of equipment malfunction, the
manufacturer’s recommendations should be strictly adhered to and followed.
TIG WELDING TROUBLE SHOOTING
7: Arc wanders during DC welding
Possible Reason
Suggested Remedy
Poor gas flow
Check and set the gas flow between 10 - 15 l/min flow rate
Incorrect arc length
Lower torch so that the tungsten is off of the work piece 2 - 5mm
Tungsten incorrect or in poor condi-
tion
Check that correct type of tungsten is being used. Remove 10mm from the weld end of
the tungsten and re sharpen the tungsten
Poorly prepared tungsten
Grind marks should run lengthwise with tungsten, not circular. Use proper grinding
method and wheel.
Contaminated base metal
Remove contaminating materials like paint, grease, oil, and dirt, including mill scale from
base metal.
Contaminated filler wire
Remove all grease, oil, or moisture from filler metal.
Incorrect filler wire
Check the filler wire and change if necessary
Содержание Xcel-Arc ARC160
Страница 28: ...28 New Zealand Limited RazorWeld RazorCut ...