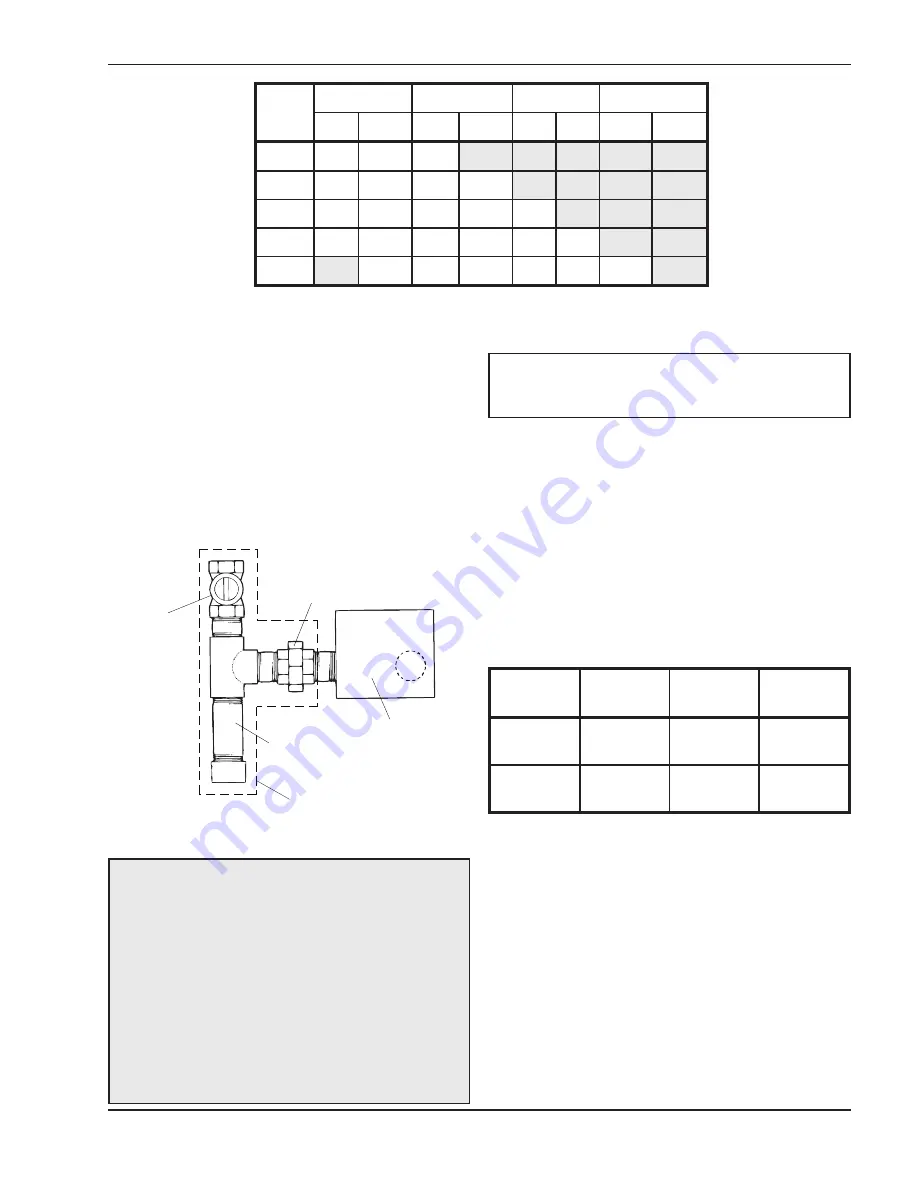
Gas Supply Connections
The inlet gas connection of the boiler gas valve is 1/2".
Provide an adequate gas piping supply line no smaller
than 1/2", according to Table H above.
Gas piping must have a sediment trap ahead of the
boiler gas controls, and a manual shut-off valve locat-
ed outside the jacket. All gas piping should be tested
after installation in accordance with local codes.
Model
No.
1/2 in. Pipe
3/4 in. Pipe
1 in. Pipe
1 1/4 in. Pipe
Nat.
Pro.
Nat.
Pro.
Nat. Pro.
Nat.
Pro.
0042
125
350
500
0066
60
160
175
460
0090
30
80
125
300
400
0135
15
40
60
150
200
450
0180
20
35
90
115
300
425
Table H: Maximum Equivalent Pipe Length (Feet)
Sediment Trap
(min. length 3”)
Union
Manual
Valve
Gas Valve
Must be supplied
by installer
Fig. 14: Sediment Trap
CAUTION:
The boiler and its manual shut-off valve
must be disconnected from the gas supply during
any pressure testing of that system at test pressures
in excess of 1/2 psi (3.45 kPa). Dissipate test
pressure in the gas supply line before reconnecting
the boiler and its manual shut-off valve to gas supply
line. FAILURE TO FOLLOW THIS PROCEDURE
MAY DAMAGE THE GAS VALVE. OVER
PRESSURED GAS VALVES ARE NOT COVERED
BY WARRANTY. The boiler and its gas connections
shall be leak tested before placing the appliance in
operation. Use soapy water for leak test. DO NOT
use open flame.
NOTE:
Do not use teflon tape on gas line pipe
thread. A flexible sealant suitable for use with Natural
and Propane gases is recommended.
These boilers are also certified to operate on propane
gas, when equipped with the combination gas valve
and orifices (pilot and main burners) sized for propane
gas.
Gas Pressure
The gas valve is provided with pressure taps to meas-
ure gas pressure upstream of the gas valve and
downstream which is the same as the manifold pres-
sure.
Water Connections & System
Piping
The pipe size for water connections is shown on page
6. Typical piping systems are shown on page 17.
This boiler is supplied with a circulator and built-in
bypass as standard to ensure the required minimum
water flow in the boiler. The bypass on models H-0135
and H-0180 is provided with an adjustable valve that is
factory-set in the full open position. The handle is
Gas Type
Inches
WC Min.
Inches
WC Max.
Regulator
Setting
Natural
7.0
10.5
3.5
Propane
12.0
13.0
11.0
Table I: Minimum and Maximum Gas Pressure
15
Содержание 0042B
Страница 14: ...VENT DAMPER 14 ...
Страница 19: ...Fig 17 Multiple Zones with Circulators Fig 18 Multiple Zones with Circulators and Indirect DHW Tank 19 ...
Страница 20: ...Wiring Diagrams 20 ...
Страница 21: ...21 ...
Страница 24: ...Fig 23 Power Vent System with Zone Valve Taco 24 ...
Страница 25: ...25 Fig 23 Power Vent System with Zone Valve Honeywell ...
Страница 36: ...36 www raypak com Raypak Inc 2151 Eastman Avenue Oxnard CA 93030 805 278 5300 Fax 805 278 5468 Litho in U S A ...