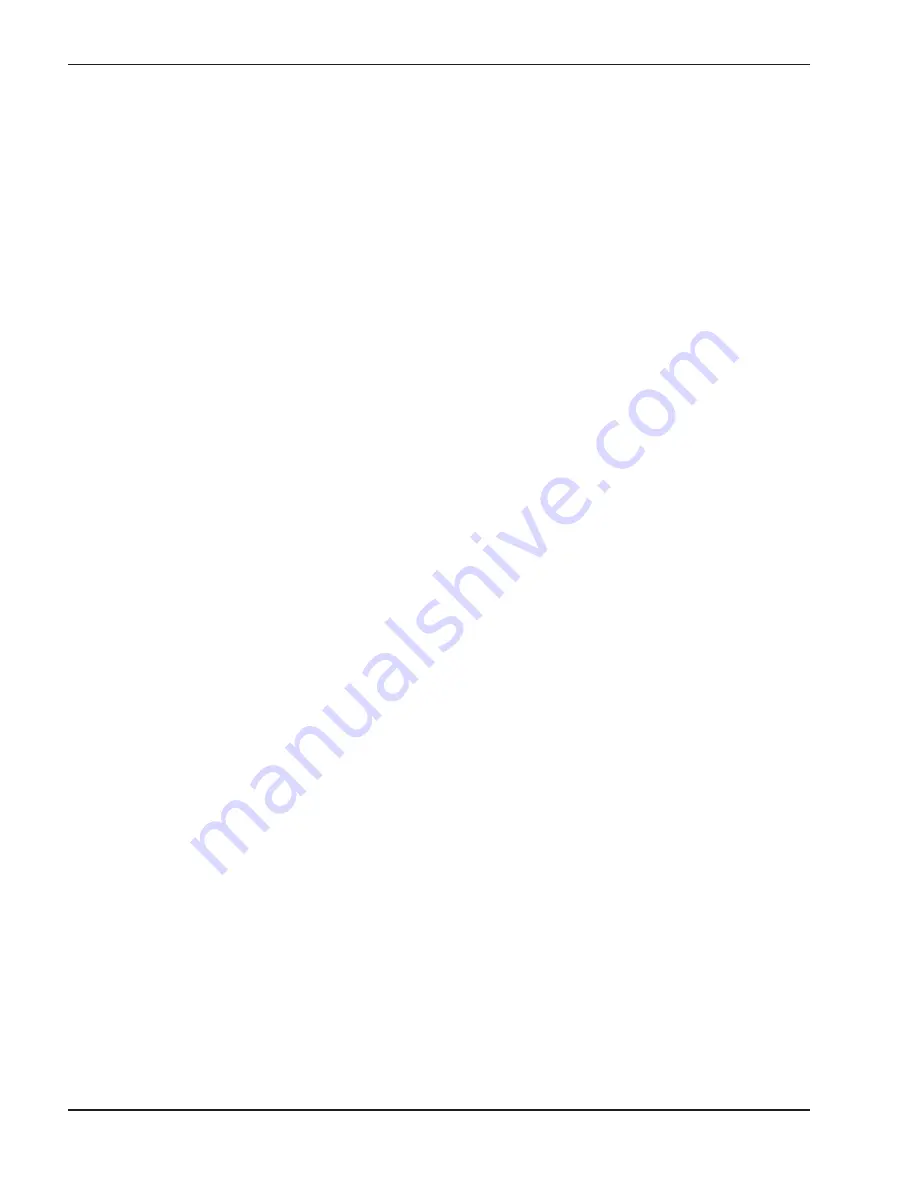
50
Follow-Up
Safety checks must be recorded as performed.
Turn heater on. After main burner ignition:
1. Check manometer for proper readings.
2. Cycle heater several times and re-check readings.
3. Remove all manometers and replace caps and
screws.
4. Check for gas leaks one more time.
Leak Test Procedure: Dual-Seat Gas
Valve
Proper leak testing requires three pressure test points
in the gas train. Remove the upper front panel and
swing the front J-box out of the way to access the gas
valve for this test. Refer to fig. 47.
Test point A is a bleedle valve located upstream of the
combination gas valve on the supply manifold.
Test point B is a bleedle valve located between the two
automatic gas valve seats.
Test point C is a bleedle valve located downstream of
both automatic gas valve seats and upstream of the
manual valve.
These tests are to be conducted with the electrical
power to the heater turned OFF.
1. Manually close the downstream leak test valve.
2. Open the bleedle valve at test point A and connect
a manometer to it. Verify that there is gas pressure
and that it is within the proper range (NOTE: must
not exceed 14.0 in. WC).
3. Open test point B and connect a rubber tube to it.
Connect the other end of the tube to a manometer
and look for a build-up of pressure. Increasing
pressure indicates a leaking gas valve which must
be replaced.
4. Next, close the upstream manual gas valve (field
supplied) and remove the manometers from the
bleedle valves in test point A and test point B.
Connect a rubber tube from the test point A blee-
dle valve to the test point B bleedle valve and
open the upstream manual gas valve. Make sure
that test point A & B bleedle valves have been
opened so as to allow gas to flow. This will bring
gas pressure to the second valve seat.
5. Open the bleedle valve at test point C and connect
a second rubber tube to it. Connect the other end
of the tube to a manometer and look for a build-up
of pressure. Increasing pressure indicates a leak-
ing gas valve which must be replaced.
6. Remove rubber tube and manometers. Close
each bleedle valve as the tubes are removed.
7. After no leakage has been verified at all valve
seats and test valve, open downstream leak test
valve and restore electrical power to the heater.
Safety Inspection
1. Check all thermostats and high limit settings.
2. During the following safety checks leave manome-
ters hooked up, check and record.
3. If other gas-fired appliances in the room are on the
same gas main, check all pressures on the
XTherm with all other equipment running.
4. Check thermostats for ON-OFF operation.
5. Check high limits for ON-OFF operation.
6. While in operation, check flow switch operation.
7. Check the low gas pressure switch (if provided).
(For proper adjustment, use the attached
manometers, if available, to set pressure. The
scales on the switch are approximate only.) Low
gas pressure switch (if provided) must be set at
3.0 in. WC for natural gas and propane gas.
8. Make sure that the high gas pressure switch is set
to 3.0 in. WC for both natural gas and propane
gas.
Finishing
1. Record all data on the “Start-up Checklist” located
at the back of this manual.
2. Disconnect the manometers and reconnect the
cap on the fan pressure tee and reinsert the seal-
ing screws into the bleedle valves.
3. Start-up is complete and the heater should be
Содержание Xtherm 1005A
Страница 2: ...2 ...
Страница 46: ...46 WIRING DIAGRAM Models 1005A 2005A ...
Страница 60: ...60 ...
Страница 64: ...64 www raypak com Raypak Inc 2151 Eastman Avenue Oxnard CA 93030 805 278 5300 Fax 805 278 5468 Litho in U S A ...