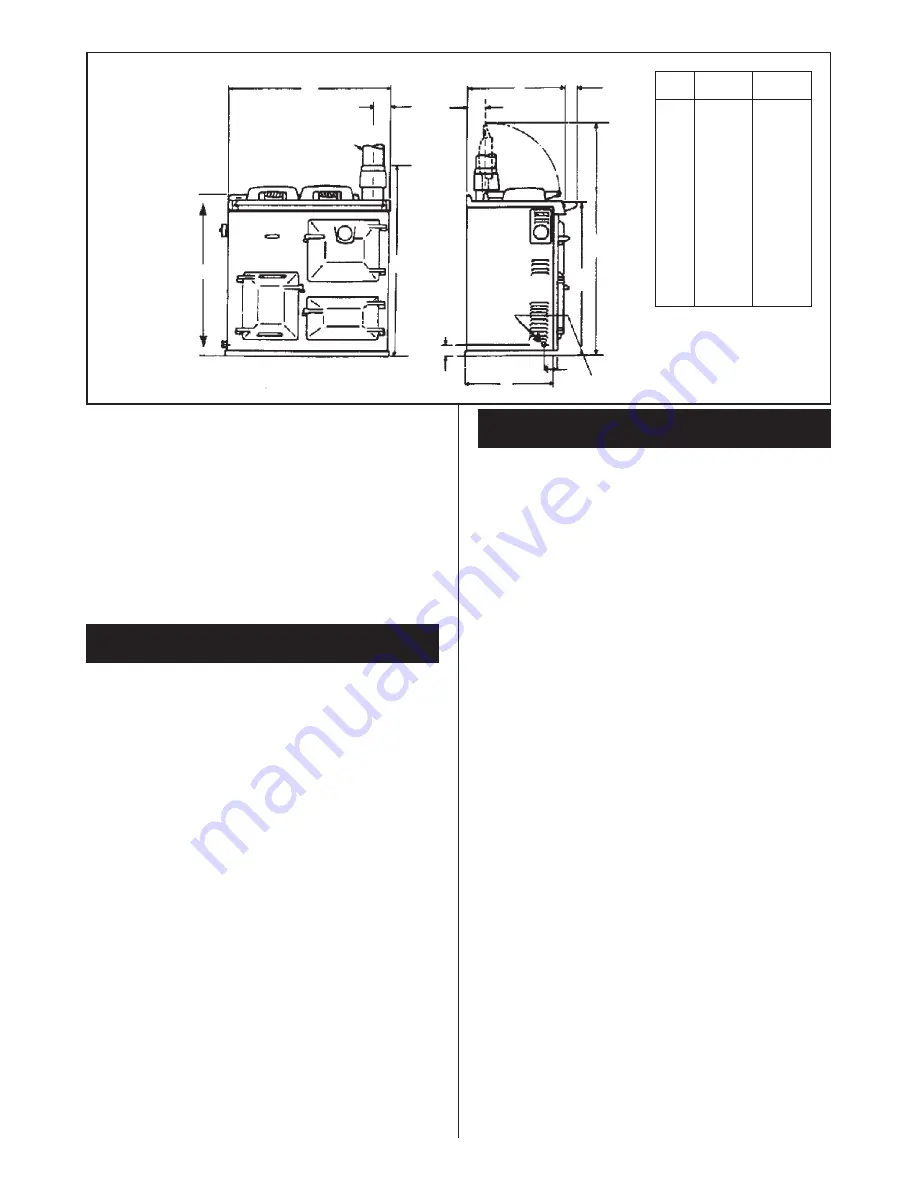
Appliance
The appliance must be installed on a solid level floor or
base of incombustible material which is capable of
supporting the total weight.
Location
The location chosen for the appliance must permit
installation and the provision of a satisfactory flue and an
adequate air supply. The location must also provide
adequate space for servicing and air circulation around
the appliance. See Section - Installation of Appliance -
General.
Meters
A gas meter is connected to the service pipe by the local
Gas Region or a local Gas Region Contractor. An existing
meter should be checked, preferably by the Gas Region,
to ensure that the meter is adequate to deal with the total
rate of gas supply required.
Installation Gas Pipes
Installation pipes should be fitted in accordance with local
gas fitting regulations. Pipework from the meter to the
appliance must be of adequate size. Do not use pipes of
a smaller size than the appliance gas connection. The
complete installation must be tested for soundness and
purged.
Detailed recommendations for fluing are given in Fluing
and Ventilation Standards.
The following notes are intended to give general
guidance:
The cross-section area of the flue serving the cooker must
not be less than the area of the flue outlet of the cooker,
and at least 3m high from the floor level.
If flue pipe is to be used it must not be less than 130mm
internal diameter.
Flue pipes and fittings should be constructed from one of
the following materials.
Material
Protective Finish
Mild Steel 1.6mm
None
Mild Steel 0.8mm over 100mm to 200mm dia. Z275 Zinc coated (AS 1397)
Mild Steel 0.8mm over 100mm to 200mm dia. Aluminised 122g/m
2
Mild Steel 0.8mm over 100mm to 200mm dia. Aluminised zinc coated
(AS 1397)
Stainless Steel 0.7mm over 100mm to 200mm dia.
430 & 300 Series grades
Fibre Cement light grade (asbestos free)
Autoclaved
Fibre Cement Heavy grade (asbestos free)
Autoclaved
Bricks (clay bldg) cement or lime mortar joints
Unprotected
Bricks
Parged with water and acid-
proof cement mix
Bricks
Inside face lined with acid-
resisting tiles embedded
in acid-resisting jointing
materials.
Precast concrete bricks or blocks
Unprotected
Flue bricks (see definition)
Nil or glazed internally
Firebricks, set in fireclay
None
Twin wall flue, AGA approved
The flue should terminate in accordance with the relevant
recommendations given in Fluing and Ventilation
Standards.
The flue pipe shall be terminated with an approved cowl
except where the authority specifically agrees otherwise.
The outlet of natural draught flue or chimney shall be so
located in relation to neighbouring constructions that wind
from any direction will not create downdraught in the flue.
FLUE SYSTEM
2
GAS SUPPLY
Fig. 1
A
B
M
J
F
G
D
C
L
E
K
H
4” (100mm DIA C.I. FLUE
GAS CONNECTION
mm
ins
A
840
33
B
848
33
5
/
16
C
820
32
1
/
4
D
1245
49
E
457
18
F
510
20
G
65
2
5
/
8
H
95
3
3
/
4
J
95
3
3
/
4
K
45
1
3
/
4
L
55
2
1
/
4
M
995
39
1
/
4
Содержание 200G/L Gas Fired Cooker
Страница 12: ...12 FAULT FINDING...
Страница 13: ...FAULT FINDING 13...
Страница 14: ...14...
Страница 15: ...15...