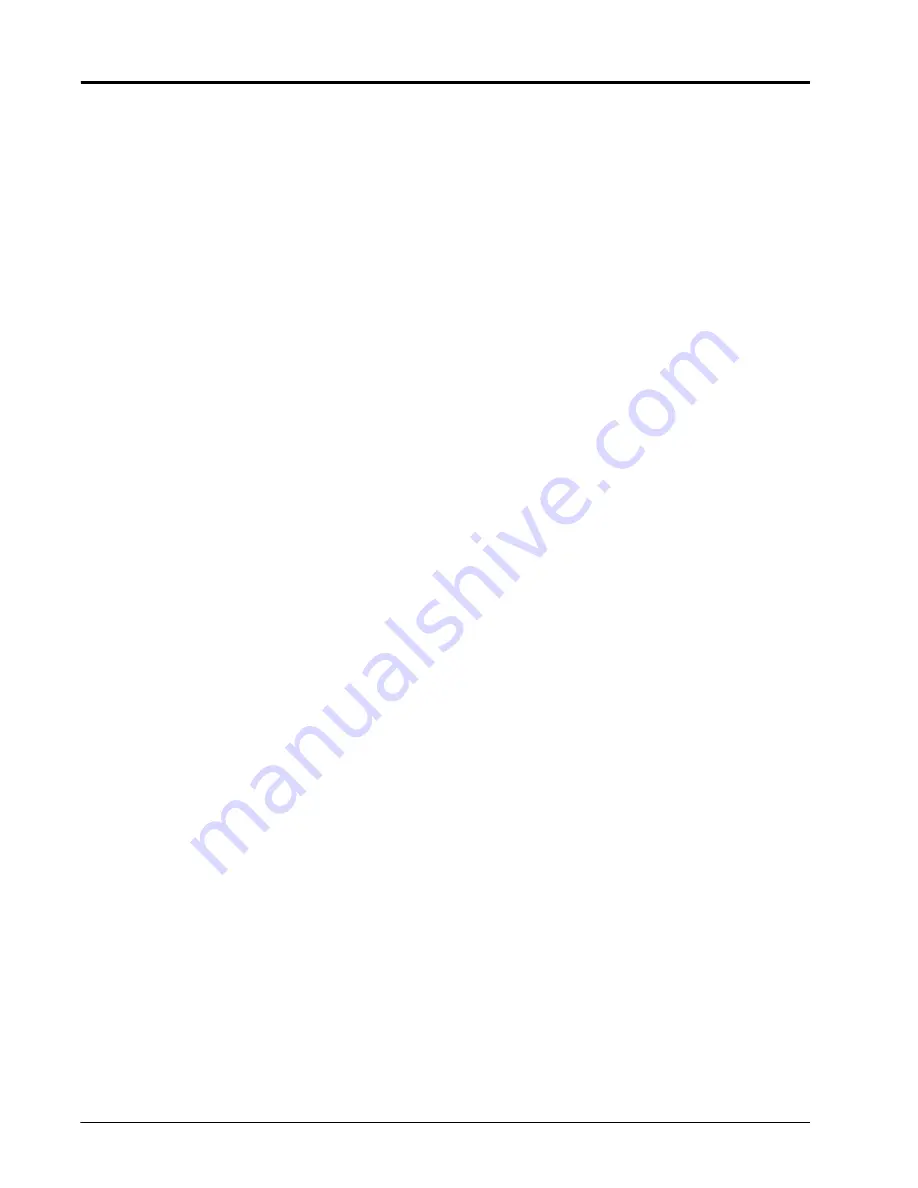
CHAPTER 1
4
Force Evo Injection System Installation Manual
•
Protect harnessing from sharp bends, twisting, or flexing over short distances and normal
implement operation.
•
Connectors and splices should not be located at bending points or in harness sections that move.
•
Ensure sufficient length for free movement of the implement during normal operation and prevent
pulling, pinching, catching, or rubbing, especially in articulation and pivot points. Clamp harnessing
securely to force controlled movement of the harness.
•
Avoid abrasive surfaces and sharp edges such as sheared or flame cut corners, fastener threads or
cap screw heads, hose clamp ends, etc.
• Do not connect, affix, or allow harnessing to come into contact with components with high vibration forces, hot
surfaces, or components carrying hot fluids beyond the temperature rating of harness components.
•
Harnessing should be protected or shielded if routing requires the hose to be exposed to
conditions beyond harnessing component specifications.
• Avoid routing harnesses in areas where damage may occur due to build up of material (e.g. dirt, mud, snow,
ice, etc.).
• Avoid routing harnesses in areas where the operator or service personnel might step or use as a grab bar.
IMPORTANT:
Avoid applying direct spray or pressure washing of electrical components and connections. High pressure
streams and sprays can penetrate seals, cause corrosion, or otherwise damage electrical components.
When performing maintenance:
• Inspect electrical components and connectors for corrosion, damaged pins or housings, etc. Repair or replace
components or harnessing as necessary.
• Ensure connectors are kept clean and dry. Apply dielectric grease to the sealing surfaces of all connections
exposed to moisture, dirt, debris, and other contaminates. Repair or replace harnessing as necessary.
• Clean electrical components with pressurized air, aerosol electrical cleaning agent, or low pressure rinse.
• Remove visible surface water from electrical components and connections using pressurized air or an aerosol
cleaning agent. Allow components to dry thoroughly before reconnecting cables.
Содержание Force Evo
Страница 1: ...Copyright 2019 Force Evo Injection System Installation Manual 016 0171 724 Rev A 12 20 E36393 ...
Страница 4: ...Table of Contents ii Force Evo Injection System Installation Manual ...
Страница 10: ...CHAPTER 2 6 Force Evo Injection System Installation Manual ...
Страница 22: ...CHAPTER 4 18 Force Evo Injection System Installation Manual ...
Страница 30: ...CHAPTER 5 26 Force Evo Injection System Installation Manual ...