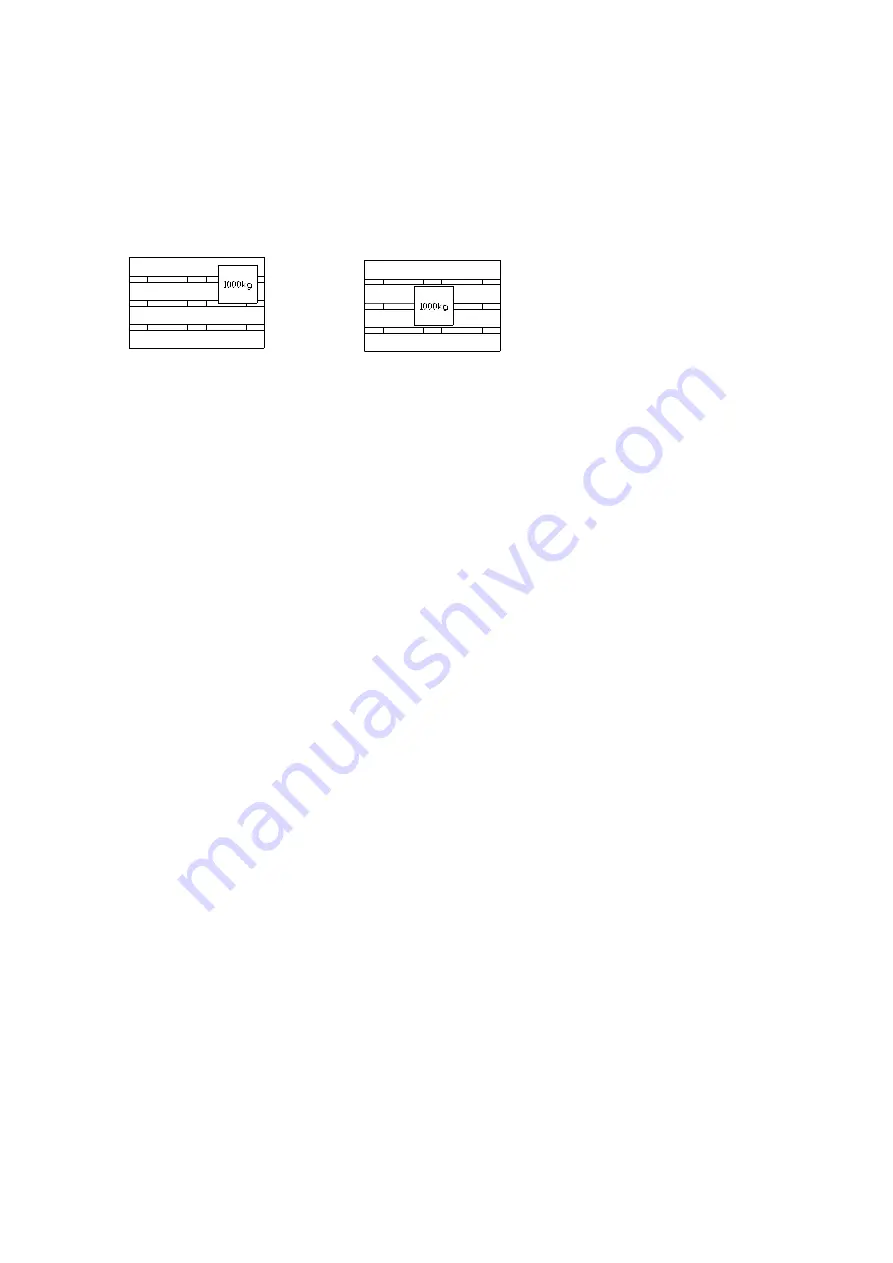
3
The most accurate weighing result is obtained when the centre of gravity of the load
is placed between the forks. With a non-centric loading, the forks will tordate and
bend. This may result in a higher inaccuracy. With legal for trade versions, the level
control will switch off the indicator with a non-centric loading or a tilted position of
more than 2 degrees (- - - - in display)
Non-optimal placement of the load
Optimal placement of the load
If of a system has fork length > 1200 mm, the load should be divided over the forks.
Bended forks shoes will occur by point loads > 500 kg and will need to be repaired
(no warranty)
Temperature range: between -10 and +40°C the maximum inaccuracy is 0.1% of the
weighed load. Outside this range inaccuracies up to 0.3% may occur.
Fast temperature changes must be avoided because it can cause condensation in
the electronics. During acclimatisation the weighing system must be switched off.
3. MAINTENANCE
From time to time, every weighing system has to be calibrated. Yearly maintenance
of the weighing system is recommended. We strongly recommend that approved
weighing systems should be calibrated yearly, by a certified institution.
Maintenance guidelines for a standard electric pallet truck also apply to the
mechanical parts of the mobile weighing system. From experience we know that the
integrated weighing system still functions when the mechanical parts are damaged
by overloading.
Main guidelines:
- The electronics may only be cleaned with a moist cloth. Chemical cleansers and
high pressure cleansing will cause damage.
- Gathering dirt between the parts of the system can negatively influence the
accuracy. Therefore, the system should be checked and cleaned regularly. Do not
use high pressure cleansing.
- Only specialists may undertake any welding. This is to avoid damage to
electronics and load cells.