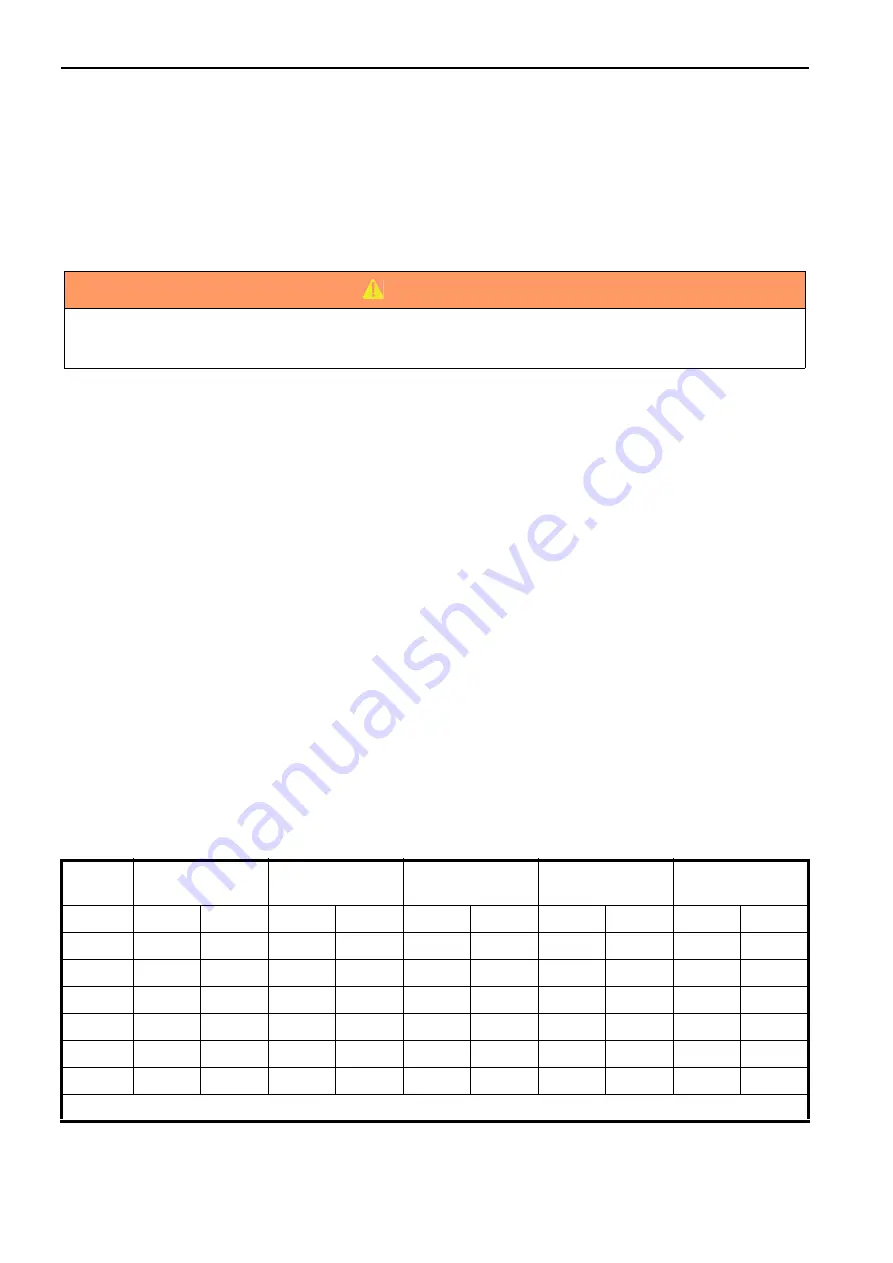
en-44
6 OPERATION
6.2
OPERATOR PRESENCE AND SAFETY INTERLOCK SYSTEM _________________
1.
The Operator Presence And Safety Interlock System will not allow the engine to start unless the
operator is sitting in the seat, the parking brake is engaged, the cutter switch is disengaged and the
traction pedal is in neutral. The system stops the engine if the operator leaves the seat with the cutters
engaged.
2.
Do each of the tests as shown below, to make sure that the Operator Presence And Safety Interlock
Systems operates correctly. If any of the tests fail, stop the test and have the system inspected and
repaired.
•
The engine will start in test 1;
•
The engine does start during tests 2 to 5.
•
The engine continues to run during test 6.
3.
Refer to the chart below for each test and follow the check (
) sign across the chart. Turn off the engine
between each test.
Test 1: Shows the normal start procedure. The operator must be in the driver seat and the cutter switch
disengaged the park brake switch on and the traction pedal in the neutral position. The engine must
start correctly.
Test 2: The engine must not start if the cutter switch is engaged.
Test 3: The engine must not start if the park brake is off.
Test 4: The engine will not start if the operator is not in the seat.
Test 5: The traction pedal is not in neutral.
Test 6: Start the engine with the normal procedure, then turn mower engagement device on and move your
weight from the seat.
WARNING
Do not operate the equipment with the operator presence and safety interlock system disengaged or
when the equipment has defects. do not disconnect or bypass any switch.
Test
Operator in the
seat
Parking Brake
Switch
Cutter Switch
Traction Pedal
In Neutral
Engine Starts
Yes
No
On
Off
On
Off
Yes
No
Yes
No
1
2
3
4
5
6
Remove your weight from the seat. The cutting units must not rotate after seven (7) seconds
Содержание RMP655
Страница 8: ...en 8 2 INTRODUCTION NOTES...
Страница 20: ...en 20 5 CONTROLS 6 2 6 8 9 11 6 3 6 4 6 6 5 1 OPERATOR WORKSTATION __________________________________________...
Страница 42: ...en 42 5 CONTROLS NOTES...
Страница 55: ...en 55 OPERATION 6 NOTES...
Страница 65: ...en 65 ADJUSTMENTS 7 NOTES...
Страница 67: ...en 67 MAINTENANCE AND LUBRICATION 8 F F D D D D F F F F F F B B A A A A E E F F F F F F E E...
Страница 86: ...en 86 8 MAINTENANCE AND LUBRICATION Cutting Unit Mounting D Bearing Housings E Rolls F F D E F D F E...
Страница 87: ...en 87 MAINTENANCE AND LUBRICATION 8 NOTES...
Страница 97: ...en 97 QUALITY OF CUT 10 NOTES...
Страница 100: ...en 100 11 FUSES RELAYS AND CONTROLLER 1 3 4 1 2 3 4 5 6 1 2 3 4 5 6 1 2 3 4 5 6 5 1 5 2 R1 R2 R3 R4 R5 2 1 2 3 4 5 6...
Страница 102: ...en 102 11 FUSES RELAYS AND CONTROLLER NOTES...
Страница 105: ...en 105 SPECIFICATIONS 12 A G F B H C K D E J...
Страница 115: ...en 115 SPECIFICATIONS 12 NOTES...
Страница 117: ......