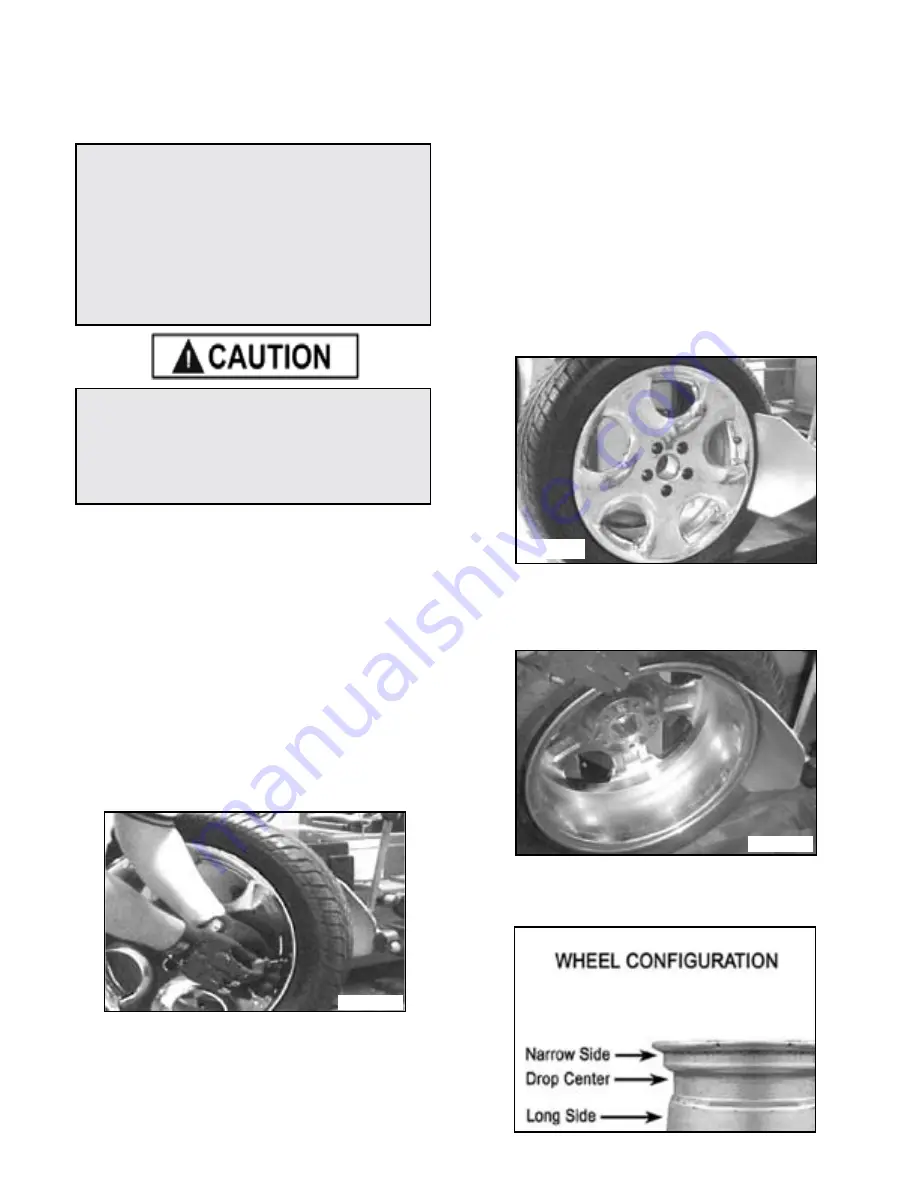
18
SECTION 11
OPERATING INSTRUCTIONS
BEAD LOOSENING AND DEMOUNTING
u
Remember to remove all weights from both sides of
the wheel. Weights left on the back side of the wheel may
cause the wheel to be clamped un-level. This may result in
the combination mount/demount head contacting the rim
causing scratches. On alloy wheels, always rotate the
wheel one turn after setting the head to insure proper wheel
chucking.
u
Always review nicks and scratches with owners of
expensive wheel and tire combinations prior to servicing.
u
Review the performance wheel section of this manual
prior to servicing performance tire/wheel combinations.
1. Deflate tire completely by removing the valve core from
the valve stem. (See Fig. 11.1).
2. The clamps on the table top may extend beyond the
table top itself. To avoid damaging the clamps and/or
wheel, move the clamps to their full inward position before
positioning a tire for bead loosening.
3. Always loosen the bead on the narrow side of the wheels
drop center first. (See Page 19 for better description of the
drop center.)
4. Use extra care in positioning the bead breaker shoe on
larger wheels/tires, and on alloy wheels. Make sure the
shoe rests next to but not on the rim, and not on the tire
sidewall.
5. Pull the bead breaker shoe away from the machine and
roll the wheel into position. The valve stem should be in the
2 o’clock position.
6. Position the bead breaker shoe against the tire next to,
but not on, the rim. Press the breaker pedal to actuate the
shoe and loosen the bead. It may be necessary to loosen
the bead in multiple locations around the tire.
(See Fig. 11.2)
7. Turn wheel around and repeat procedure on the other
side of the wheel. This should be the long side of the drop
center. It will be easier to clamp the wheel to the table top if
the lower bead is loosened last. (See Fig. 11.3)
8. Determine the mounting side of the wheel. The
mounting side is the narrow side of the drop center. The tire
is removed for clarity. (See Fig. 11.4)
The unit must be properly operated and
maintained to help avoid accidents that could
damage the unit and injure the operator or
bystanders. This section of the Operating
Instructions manual review basic operations
and use of controls. These instructions should
be reviewed with all employees before they are
allowed to work with the machine.
Keep these instructions near the machine for
easy reference.
CAUTION!
This machine may operate differently from
machines you have previously operated.
Practice with a regular steel wheel and tire
combination to familiarize yourself with the
machine’s operation and function.
Fig. 11.1
Fig. 11.2
Fig. 11.3
Fig. 11.4