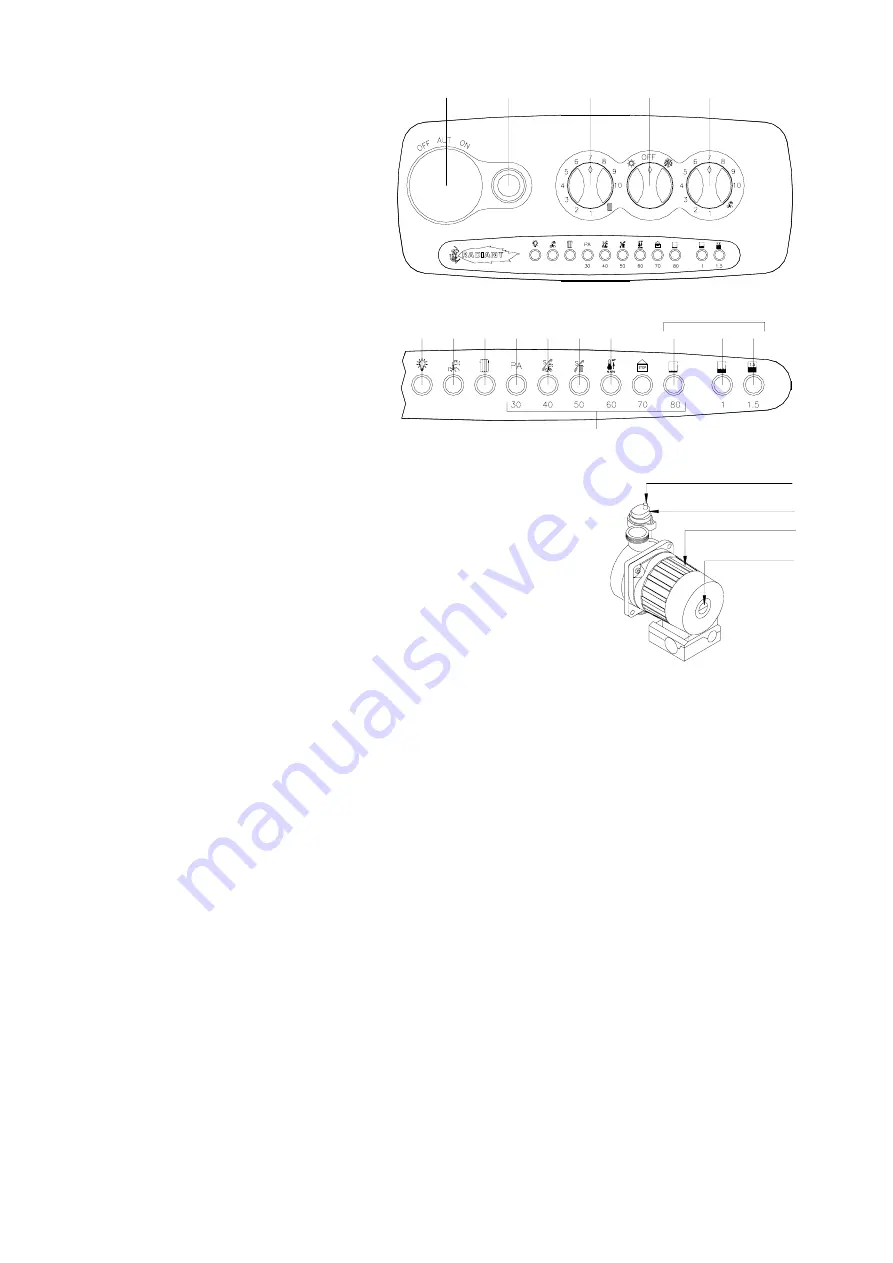
Installation Manual
Floor standing storage boiler – Cod. 99949NA – November 2002
10
PUMP CAP
CIRCULATING PUMP
AIR VENT VALVE CAP
AIR VENT VALVE
CONTROL PANEL
LEGEND
(see fig. 1)
1.
SUMMER-WINTER ON-OFF SWITCH
2.
LOCK-OUT INDICATOR
3.
HEATING TEMPERATURE ADJUSTMENT KNOB
4.
WATER TEMPERATURE ADJUSTMENT KNOB
5.
SPACE FOR ADDING AN OPTIONAL TIMER
SELF- DIAGNOSTIC
LEGEND (see fig. 2)
6.
OPERATING/ POWER INDICATOR
7.
DOMESTIC HOT WATER OPERATION
8.
HEATING OPERATION
9.
FLASHING LIGHT DENOTING AIR PRESSURE SWITCH
FAILURE
10.
FLASHING LIGHT DENOTING DOMESTIC WATER
SENSOR FAILURE
11.
FLASHING LIGHT DENOTING HEATING SENSOR
FAILURE
12.
FLASHING LIGHT DENOTING 90° C MAX
TEMPERATURE SENSOR FAILURE
13.
FLASHING LIGHT DENOTING LACK OF WATER IN
SYSTEM
14.
WATER PRESSURE LEVEL 1 BAR
15.
WATER PRESSURE LEVEL 1.5 BAR
16.
ELECTRONIC TEMPERATURE INDICATOR
STARTING UP THE BOILER
After connecting up the water supply, before starting up the boiler, carry out the
following procedures:
Preliminary procedure
•
Do as follows:
•
make sure the power supply for the boiler is the same as that stated on the plate
(230V - 50Hz) and that the live, neutral and earth connections have been
properly connected;
•
make sure the type of gas being supplied is the same as the type for which the
boiler has been tested and approved (see plate data);
•
make sure the unit is properly earthed;
•
make sure there are no flammable liquids or materials in the immediate vicinity of the boiler;
•
make sure that any shut-off valves in the heating circuit are open;
•
open the gas cock and check the gas seals, making sure the counter shows no sign of leaks; in any case, double check by
using a soapy solution and eliminate all eventual leaks. The checking procedure for the gas burner attachment is carried out
with the boiler working;
•
make sure the electrical mains switch is OFF;
•
remove the front cover by pulling it forwards;
•
undo the side screws and rotate the panel downwards
Filling the system
After making sure the gas cock is closed, fill the heating system as follows;
•
fill the system until a pressure of 1.5 bar has been reached (light no. 15 ON; see fig. 2) and then close the tap on the filling
loop;
•
make sure the cap on the auto air vent valve is slightly loose to allow air to escape from the system (see fig. 1);
•
undo the cap on the circulation pump to eliminate any eventual air locks (see fig. 1). It is a good idea to purge all radiators of
air at this point too;
•
before starting up the boiler the water pressure must be checked again; if this is seen to be below 0.5 bar (light no. 13
flashes; see fig. 2), bring it back up to 1.5 bar (light no. 15 ON; see fig. 2) and close the tap on the filling loop
•
switch on the electrical power supply to the boiler;
•
turn selector switch 1 to the WINTER position (see fig. 1), after a few seconds the pump will come into action;
•
once the boiler is working, if any noises are heard in the system, repeat the above air purging procedures until there is no air
left in the system;
•
check there are no obstructions in the exhaust duct;
2
3
1
4
6
7
8
9
10
11
12
ELECTRONIC WATER
PRESSURE GAUGE
SELF-DIAGNOSTIC
5
13
14
15
16
Fig. 1
Fig. 1
Fig. 2