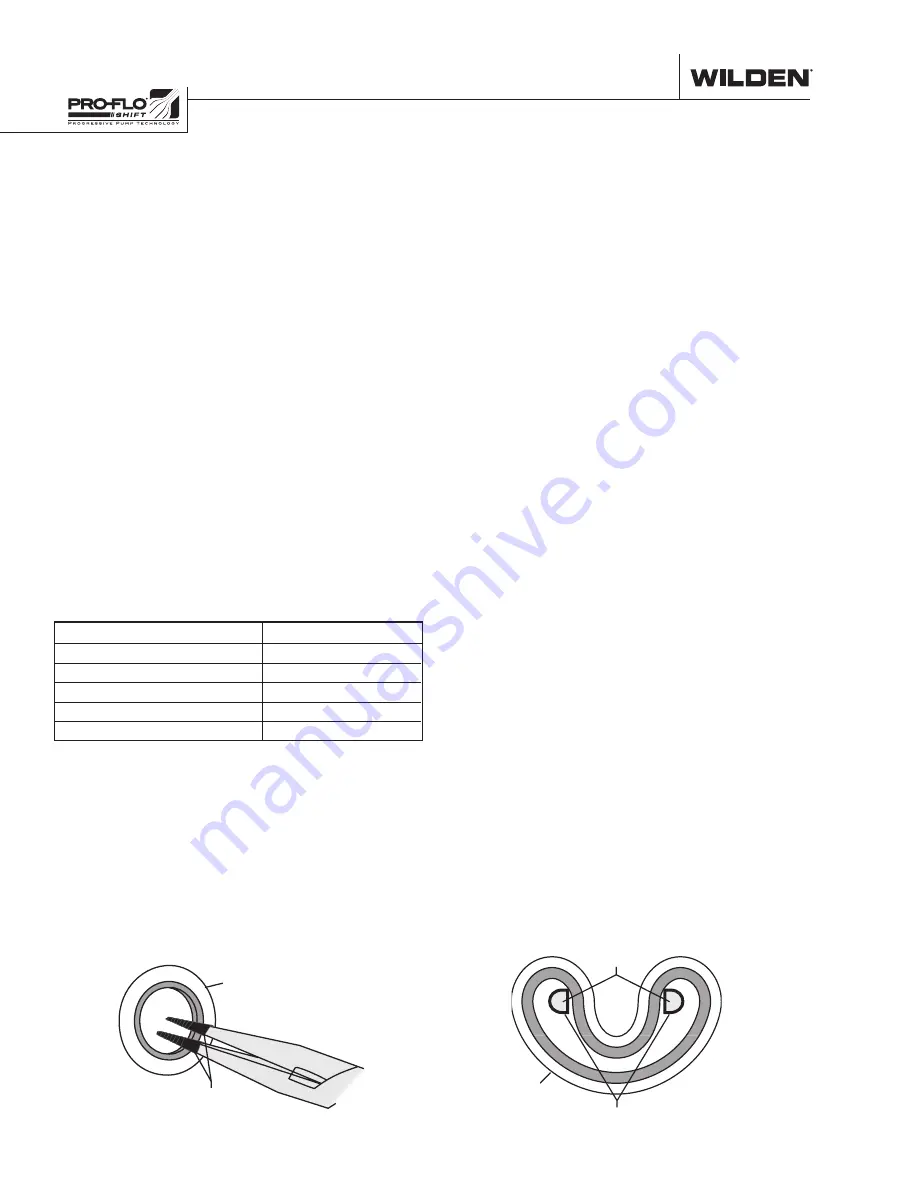
WILDEN PUMP & ENGINEERING, LLC
18
WIL-11560-E-07
REASSEMBLY:
Upon performing applicable maintenance to the air
distribution system, the pump can now be reassembled.
Please refer to the disassembly instructions for photos
and parts placement. To reassemble the pump, follow
the disassembly instructions in reverse order. The air
distribution system needs to be assembled first, then
the diaphragms and finally the wetted path. Please find
the applicable torque specifications on this page. The
following tips will assist in the assembly process.
• Lubricate air valve bore, center section shaft and pilot
spool bore with NLGI grade 2 white EP bearing grease
or equivalent.
• Clean the inside of the center section shaft bore to
ensure no damage is done to new shaft seals.
• A small amount of NLGI grade 2 white EP bearing
grease can be applied to the muffler and air valve
gaskets to locate gaskets during assembly.
• Make sure that the exhaust port on the muffler plate
is centered between the two exhaust ports on the
center section.
• Stainless steel bolts should be lubed to reduce the
possibility of seizing during tightening.
SHAFT SEAL INSTALLATION:
PRE-INSTALLATION
• Once all of the old seals have been removed, the
inside of the bushing should be cleaned to ensure no
debris is left that may cause premature damage to the
new seals.
INSTALLATION
The following tools can be used to aid in the installation
of the new seals:
Needle-Nose Pliers
Phillips Screwdriver
Electrical Tape
• Wrap electrical tape around each leg of the needle-
nose pliers (heat shrink tubing may also be used). This
is done to prevent damaging the inside surface of the
new seal.
• With a new seal in hand, place the two legs of the
needle-nose pliers inside the seal ring. (See Figure A.)
• Open the pliers as wide as the seal diameter will allow,
then with two fingers pull down on the top portion of
the seal to form a kidney shape. (See Figure B.)
• Lightly clamp the pliers together to hold the seal into
the kidney shape. Be sure to pull the seal into as tight
of a kidney shape as possible, this will allow the seal to
travel down the bushing bore easier.
• With the seal clamped in the pliers, insert the seal into
the bushing bore and position the bottom of the seal
into the correct groove. Once the bottom of the seal is
seated in the groove, release the clamp pressure on the
pliers. This will allow the seal to partially snap back to
its original shape.
• After the pliers are removed, you will notice a slight
bump in the seal shape. Before the seal can be properly
resized, the bump in the seal should be removed as
much as possible. This can be done with either the
Phillips screwdriver or your finger. With either the side
of the screwdriver or your finger, apply light pressure
to the peak of the bump. This pressure will cause the
bump to be almost completely eliminated.
• Lubricate the edge of the shaft with NLGI grade 2 white
EP bearing grease.
• Slowly insert the center shaft with a rotating motion.
This will complete the resizing of the seal.
• Perform these steps for the remaining seals.
Figure A
SHAFT SEAL
TAPE
Figure B
SHAFT SEAL
TAPEAV
NEEDLE-NOSE
PLIERS
PRO-FLO
®
SHIFT MAXIMUM TORQUE
SPECIFICATIONS
Description of Part
Torque
Air Valve
11.3 N•m (100 in-lb)
Dial Set Screw
11.3 N•m (100 in-lb)
Outer Pistons, All diaphragms
47.1 N•m (30 ft-lb)
Top and Bottom Manifold
8.5 N•m (75 in-lb)
Liquid Chamber to Center Section
8.5 N•m (75 in-lb)
R E A S S E M B L Y H I N T S & T I P S
Содержание Wilden PS220 Series
Страница 1: ...EOM Engineering Operation Maintenance wildenpump com Where Innovation Flows PS220 PS230 FIT Metal Pump...
Страница 21: ...N O T E S...
Страница 25: ...N O T E S...
Страница 26: ...N O T E S...