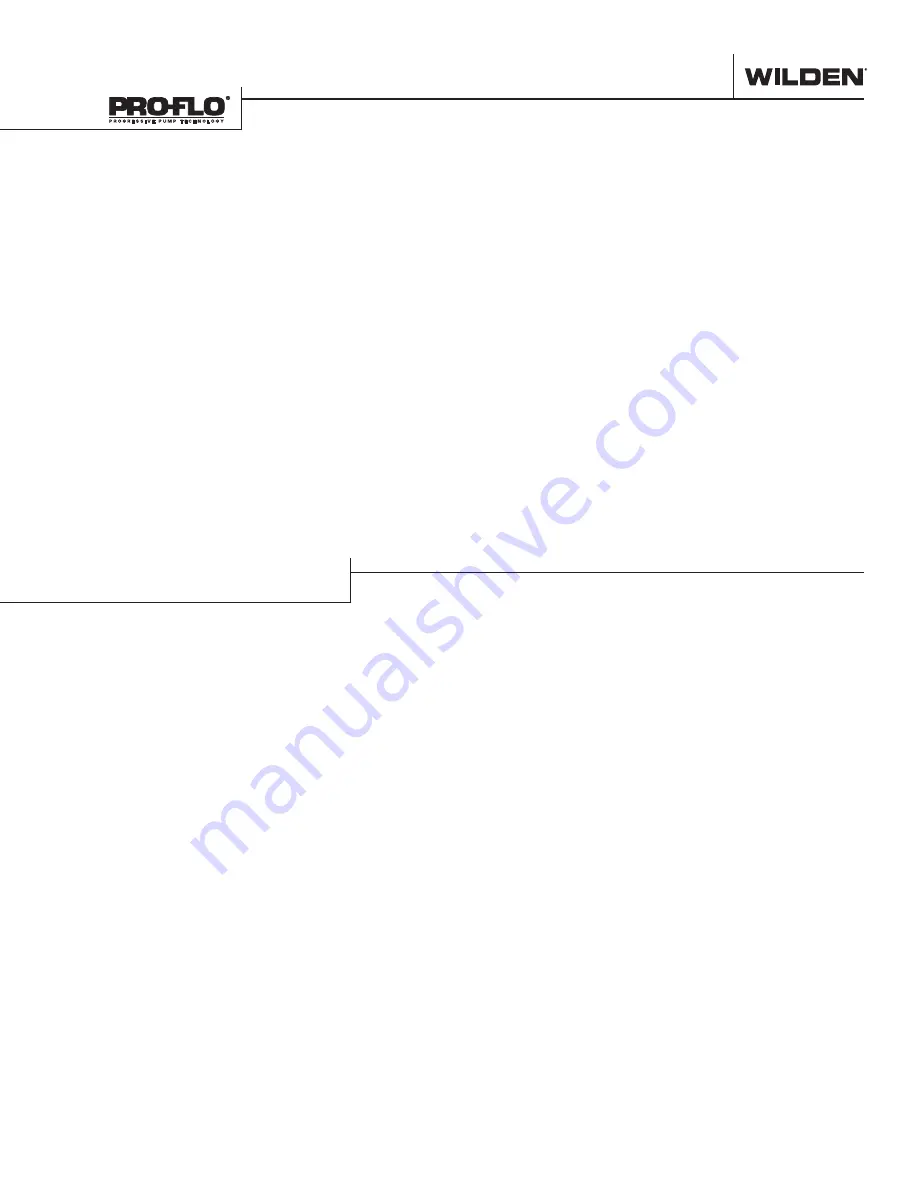
WIL-11160-E-09
9
WILDEN PUMP & ENGINEERING, LLC
OPERATION: The P1500 is pre-lubricated, and does not
require in-line lubrication . Additional lubrication will not
damage the pump, however if the pump is heavily lubri-
cated by an external source, the internal lubrication may
be flushed out . If the pump is then moved to a non-
lubricated location, it may need to be dis assembled and
re-lubricated as described in the DISASSEMBLY / REAS-
SEMBLY INSTRUCTIONS .
Pump discharge rate can be controlled by limiting the
volume and/or pressure of the air supply to the pump
(preferred method) . An air regulator is used to regulate
air pressure . A needle valve is used to regulate volume .
Pump discharge rate can also be controlled by throttling
the pump discharge by partially closing a valve in the
discharge line of the pump . This action increases friction
loss which reduces flow rate . This is useful when the
need exists to control the pump from a remote location .
When the pump discharge pressure equals or exceeds
the air supply pressure, the pump will stop; no bypass
or pressure relief valve is needed, and pump damage
will not occur . The pump has reached a “deadhead”
situation and can be restarted by reducing the fluid
discharge pressure or increasing the air inlet pressure .
The Wilden P1500 pump runs solely on compressed air
and does not generate heat, therefore your process fluid
temperature will not be affected .
MAINTENANCE AND INSPECTIONS: Since each appli-
cation is unique, maintenance schedules may be differ-
ent for every pump . Frequency of use, line pressure,
viscosity and abrasiveness of process fluid all affect
the parts life of a Wilden pump . Periodic inspections
have been found to offer the best means for preventing
unscheduled pump downtime . Personnel familiar with
the pump’s construction and service should be informed
of any abnormalities that are detected during operation .
RECORDS: When service is required, a record should be
made of all necessary repairs and replacements . Over
a period of time, such records can become a valuable
tool for predicting and preventing future maintenance
problems and unscheduled downtime . In addition, accu-
rate records make it possible to identify pumps that are
poorly suited to their applications .
Pump will not run or runs slowly.
1 . Ensure that the air inlet pressure is at least 0 .4 bar (5
psig) above startup pressure and that the differential
pressure (the difference between air inlet and liquid
discharge pressures) is not less than 0 .7 bar (10 psig) .
2 . Check air inlet filter for debris (see SUGGESTED
INSTALLATION) .
3 . Check for extreme air leakage (blow by) that would
indicate worn seals/bores in the air valve, pilot spool,
main shaft .
4 . Disassemble pump and check for obstructions in the
air passageways or objects that would obstruct the
movement of internal parts .
5 . Check for sticking ball check valves . If material being
pumped is not compatible with pump elastomers,
swelling may occur . Replace ball check valves and
seals with proper elastomers . Also, as the check
valve balls wear out, they become smaller and can
become stuck in the seats . In this case, replace balls
and seats .
6 . Check for broken inner piston that will cause the air
valve spool to be unable to shift .
7 . Remove plug from pilot spool exhaust .
Pump runs but little or no product flows.
1 . Check for pump cavitation; slow pump speed down
to allow thick material to flow into liquid chambers .
2 . Verify that vacuum required to lift liquid is not greater
than the vapor pressure of the material being pumped
(cavitation) .
3 . Check for sticking ball check valves . If material being
pumped is not compatible with pump elastomers,
swelling may occur . Replace ball check valves and
seals with proper elastomers . Also, as the check
valve balls wear out, they become smaller and can
become stuck in the seats . In this case, replace balls
and seats .
Pump air valve freezes.
1 . Check for excessive moisture in compressed
air . Either install a dryer or hot air generator for
compressed air . Alternatively, a coalescing filter may
be used to remove the water from the compressed
air in some applications .
Air bubbles in pump discharge.
1 . Check for ruptured diaphragm .
2 . Check tightness of outer pistons (refer to Section 8C) .
3 . Check tightness of wetted path fasteners and integ-
rity of o-rings and seals, especially at intake mani-
fold .
4 . Ensure pipe connections are airtight .
Product comes out air exhaust.
1 . Check for diaphragm rupture .
2. Check tightness of outer pistons to shaft.
S U G G E S T E D O P E R A T I O N & M A I N T E N A N C E
T R O U B L E S H O O T I N G