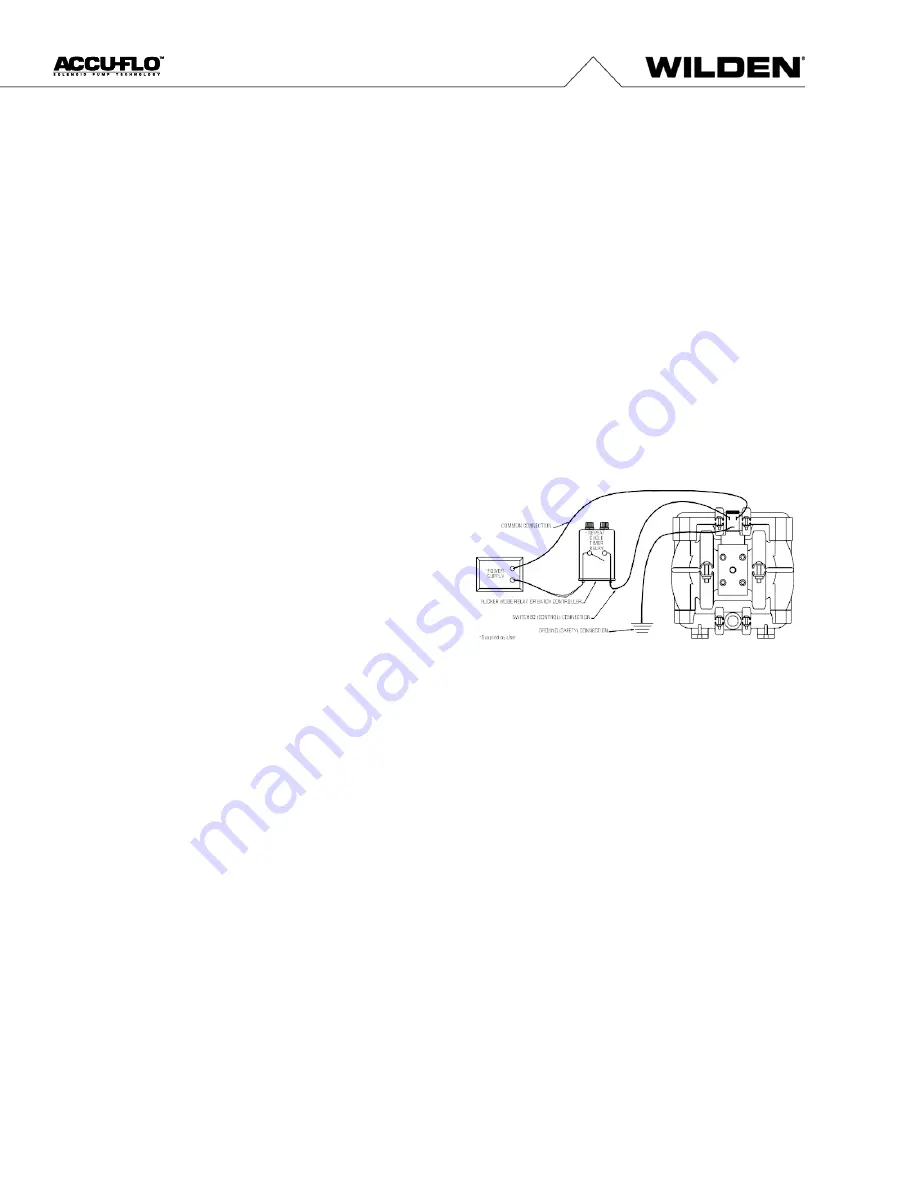
WIL-11060-E-03
Wilden
®
12
Suggested Installation, Operation, Maintenance and Troubleshooting
Operating Principles Behind Accu-Flo™ Pumps
Operation
The A200P is pre-lubricated, and does not require in-line lubrication.
Additional lubrication will not damage the pump, however if the
pump is heavily lubricated by an external source, the pump’s
internal lubrication may be washed away. If the pump is then moved
to a non-lubricated location, it may need to be disassembled and re-
lubricated as described in the ASSEMBLY/DISASSEMBLY
INSTRUCTIONS.
Pump discharge rate can be controlled by limiting the solenoid, the
volume, and/or pressure of the air supply to the pump. A regulator is
used to control air pressure while a needle valve is used to control
volume. Pump discharge rate can also be controlled by throttling
the pump discharge by partially closing a valve in the discharge line
of the pump. This action increases friction loss which reduces flow
rate. (See Section 5.) This is useful when the need exists to control
the pump from a remote location. When the pump discharge
pressure equals or exceeds the air supply pressure, the pump will
stop; no bypass or pressure relief valve is needed, and pump
damage will not occur. The pump has reached a “deadhead”
situation and can be restarted by reducing the fluid discharge
pressure or increasing the air inlet pressure. The Wilden A200P
pump runs solely on compressed air and does not generate heat,
therefore your process fluid temperature will not be affected.
Maintenance and Inspections
Since each application is unique, maintenance schedules may be
different for every pump. Frequency of use, line pressure, viscosity
and abrasiveness of process fluid all affect the parts life of a Wilden
pump. Periodic inspections have been found to offer the best means
for preventing unscheduled pump downtime. Personnel familiar with
the pump’s construction and service should be informed of any
abnormalities that are detected during operation.
Records
When service is required, a record should be made of all necessary
repairs and replacements. Over a period of time, such records can
become a valuable tool for predicting and preventing future
maintenance problems and unscheduled downtime. In addition,
accurate records make it possible to identify pumps that are poorly
suited to their applications.
Suggested Operation & Maintenance
Operation
The pump will not shift reliably unless the minimum supply
pressure is provided. For the A200P the minimum supply
pressure for reliable operation is 2.7 bar (40 psig).
The solenoid operated pump is permanently lubricated during
assembly, and requires no additional lubrication under normal
operation. If the unit runs under extreme conditions (continuous
operation at high speeds), it may be necessary to relubricate
the center block with a buna-n compatible white bearing grease
every 50 mil- lion cycles. Continuous lubrication with a
compatible oil is not harmful, and will provide longer seal life,
but it may flush all grease out of the unit.
A red button on the side of the air valve is a manual override;
when actuated it will shift the valve as if an electric current had
actuated the solenoid.
Records
When service is required, a record should be made of all
necessary repairs and replacements. Over a period of time,
such records can become a valuable.
tool for predicting and preventing future maintenance problems and
unscheduled downtime. In addition, accurate records make it
possible to identify pumps that are poorly suited to their applications.
Maintenance and Inspections
Since each application is unique, maintenance schedules may be
different for every pump. Frequency of use, line pressure, viscosity and
abrasiveness of process fluid all effect the parts life of a Wilden pump.
Periodic inspections have been found to offer the best means for
preventing unscheduled pump downtime. Personnel familiar with the
pump’s construction and service should be informed of any
abnormalities that are detected during operation. Internal maintenance
is not recommended for Accu-Flo™ solenoid air valves. When worn or
damaged, a new air valve body, coil or terminal connector must be
purchased. Please consult Section 8 for part numbers.