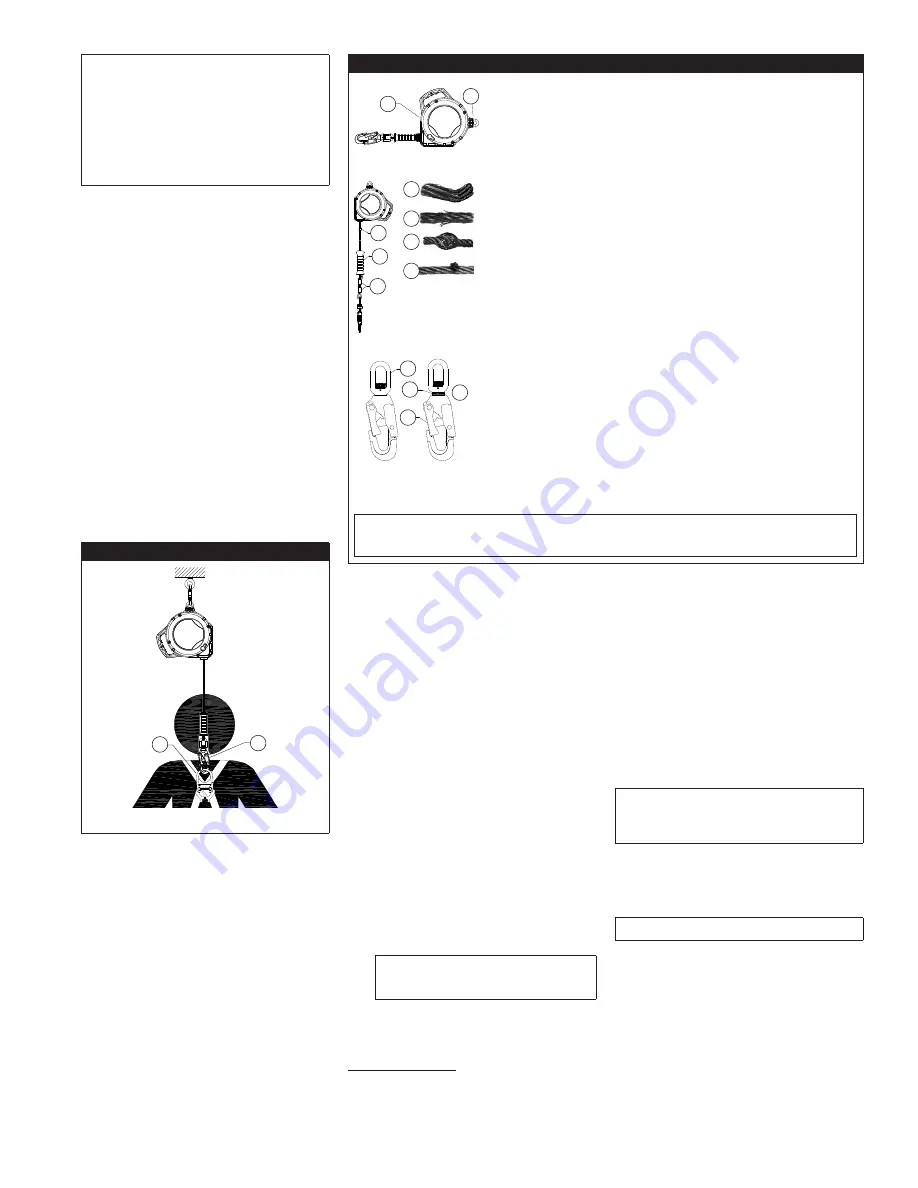
3
WARNING:
Do not alter or intentionally
misuse this equipment. Consult Capital Safety
when using this equipment in combination with
components or subsystems other than those
described in this manual. Some subsystem and
component combinations may interfere with the
operation of this equipment. Use caution when
using this equipment around moving machinery,
electrical hazards, chemical hazards, and sharp
edges. Do not loop the lifeline around small
structural members.
Prior to Each Use
: Inspect the Rebel
SRL per the Inspection List (Table 1). Do
not use the SRL if inspection reveals an
unsafe condition.
After a Fall:
Any equipment subjected
to the forces of arresting a fall or
exhibiting damage consistent with
the effect of fall arrest forces (see
Table 1) must be removed from service
immediately and sent to an authorized
service center for repair.
Making Connections:
After securing
the SRL to a rigid anchorage point (see
Installation
), attach the Snaphook end of
the SRL Lifeline to the dorsal D-ring on
the Full Body Harness (see Figure 5).
In situations where it is necessary to use
a front D-ring attachment point, such as
working on a fixed ladder, a Full Body
Harness with a Chest D-ring must be
used. (Refer to OSHA requirements.)
Figure 5 - Use
A
B
A
Dorsal D-Ring
B
Lifeline Snaphook
Use:
While attached to the SRL, the
worker is free to move about within
recommended working areas at normal
speeds. The lifeline should extend
smoothly and retract without hesitation.
If a slack line condition is created in
normal use the unit should be returned
to an Capital Safety for service. Should
a fall occur, the SRL will lock and arrest
the fall. Upon rescue, remove the
SRL from use. Inspect as described in
Table 1. When working with the SRL,
allow the lifeline to recoil back into the
device under control. A short Tag Line
may be required to extend or retract
the lifeline during connection and
disconnection. Allowing the lifeline to be
fully extended for long periods of time
may cause premature weakening of the
retraction spring.
INSPeCTION
To ensure safe, efficient operation, the
Rebel SRL must be inspected per the
procedures in Table 1 at the following
frequencies:
Before Each Use:
•
OSHA 1910.66,
OSHA 1926.502 ANSI Z359.1,
and CSA Z259.2.2) require an
inspection of the SRL and associated
equipment before each use. See
Table 1 for inspection procedures.
Annual Inspection:
•
ANSI Z359.1
requires a formal inspection of
the SRL by a competent person
2
other than the user. More frequent
inspections by a competent person
may be required based on the
nature and severity of workplace
conditions affecting the equipment
and the modes of use and exposure
time of the equipment. See sections
Table 1 for inspection guidelines.
Record results in the
Inspection &
Maintenance Log
on the back cover
of this instruction.
NOTe:
In Canada, CSA requires servicing
of SRLs within two year of the date of
manufacture and annual inspection thereafter.
After a Fall:
•
The SRL should be
removed from service and returned
to an authorized service center for
inspection and repair.
2 COMPETENT PERSON: One who is capable of
identifying existing and predictable hazards in the sur-
roundings or working conditions which are unsanitary,
hazardous, or dangerous to employees, and who has
authorization to take prompt corrective measures to
eliminate them.
MAINTeNANCe & SeRvICe
Periodically clean the exterior of the SRL
using water and a mild soap solution.
Position the SRL so excess water can
drain out. Clean labels as required.
Clean Lifeline with water and mild soap
solution. Rinse and thoroughly air dry.
Do not force dry with heat. An excessive
buildup of dirt, paint, etc. may prevent
the Lifeline from fully retracting back
into the housing causing a potential free
fall hazard. Replace Lifeline if excessive
buildup is present.
NOTe:
If the Lifeline contacts acids, remove the
SRL from service and wash with water and a mild
soap solution. Inspect SRL before returning it to
service.
Additional maintenance and servicing
procedures must be completed by
an authorized service center. Do not
attempt to disassemble the SRL.
NOTe:
Do not lubricate any parts in the SRL.
STORAGe
Store the SRL in a cool, dry, clean
environment out of direct sunlight. Avoid
areas where chemical vapors may exist.
Thoroughly inspect the SRL after any
period of extended storage.
Table 1 - Inspection Procedures
SRL
A
B
Inspect the SRL for loose bolts and bent or damaged parts.
•
Inspect the Housing (A) for distortion, cracks, or other damage.
•
Inspect the Swivel Eye (B) for cracks or damage and verify that it swivels freely.
•
Ensure the SRL locks up when the Lifeline is jerked sharply. Lockup should be
•
positive with no slipping.
Inspect the entire unit for signs of corrosion.
•
verify that all labels are present and are fully legible (see
•
Labels
).
Lifeline
A
F
G
B
C
D
E
verify that the Lifeline pulls out and retracts fully without hesitation or slack in
•
the line.
Inspect the Reserve Lifeline payout. If a fall has been arrested with most of the
•
lifeline out, the Reserve Lifeline may have been deployed. Pull the Lifeline out of
the SRL until it stops. If a red band (A) is visible, the Reserve Lifeline has been
spent and the SRL must be serviced by and authorized service center before
reuse.
Inspect the entire Lifeline Cable for cuts, kinks (B), broken wires (C), bird-caging
•
(D), welding splatter (E), corrosion, chemical contact areas, or severely abraded
areas.
Slide the Cable Bumper (F) up and inspect the ferrules (G) for cracks or damage
•
and the cable for corrosion or broken wires.
Snaphook
B
D
A
C
Inspect the Snaphook for signs of damage or corrosion.
•
verify that the Gate (A) opens and closes correctly and the Swivel (B) rotates
•
freely.
Inspect the Snaphook Impact indicator. If the Snaphook is in
•
‘Indicated Mode’
(C); as indicated by an exposed red band (D), the SRL has been subjected to an
impact load and should be removed for service by an authorized service center.
Do not attempt to reset the Impact Indicator.
Connectors & Full Body
Harness
Inspect Anchorage Connectors for damage, corrosion, and proper working
•
condition.
Inspect the Full Body Harness per the manufacturer’s instructions.
•
AfTeR INSPeCTION: Record Inspection results in the Inspection & Maintenance Log (see back cover). If
inspection reveals an unsafe or defective condition, remove from service immediately and contact an
authorized service center for repair.