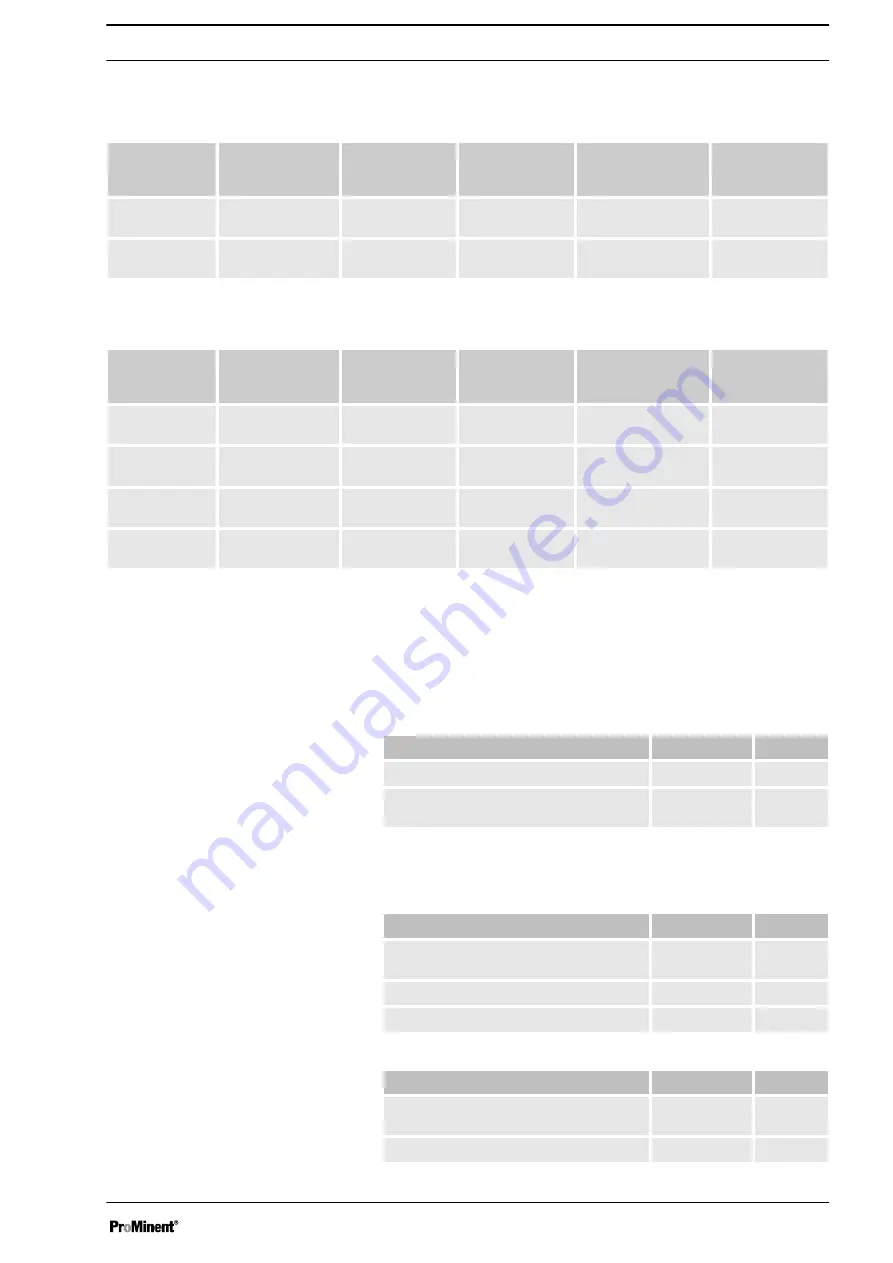
14.3 Wetted materials
DN 25 ball valve
Material version Liquid end, suc‐
tion/pressure con‐
nector
Seals*
Valve balls
Valve seats
Integral relief
valve
PVT
PVDF
PTFE
Glass
PTFE
PVDF / FPM or
EPDM
SST
Stainless steel
1.4581
PTFE
Stainless steel
1.4401
PTFE
Stainless steel /
FPM or EPDM
DN 32 plate valves
Material version Liquid end, suc‐
tion/pressure con‐
nector
Seals*
Valve plates /
valve springs
Valve seats
Integral relief
valve
PPT
PP
PTFE
Ceramic / hast. C
+ CTFE**
PTFE
PVDF / FPM or
EPDM
PCT
PVC
PTFE
Ceramic / hast. C
+ CTFE**
PTFE
PVDF / FPM or
EPDM
PVT
PVDF
PTFE
Ceramic / hast. C
+ CTFE**
PTFE
PVDF / FPM or
EPDM
SST
Stainless steel
1.4581
PTFE
Stainless steel
1.4404 / Hast. C
PTFE
Stainless steel /
FPM or EPDM
* Metering diaphragm is PTFE coated
** The valve spring is coated with CTFE (resistance similar to PTFE)
14.4 Ambient conditions
14.4.1 Ambient temperatures
Data
Value Unit
Storage and transport temperature
-10 ... +50 °C
Ambient temperature in operation (drive +
motor):
-10 ... +45 °C
14.4.2 Media temperatures
Data
Value Unit
Max. temperature long-term at max. oper‐
ating pressure
60 °C
Max. temperature for 15 min at max. 2 bar
100 °C
Minimum temperature
-10 °C
Data
Value Unit
Max. temperature long-term at max. oper‐
ating pressure
45 °C
Max. temperature for 15 min at max. 2 bar
60 °C
Pump, compl.
PP liquid end
PC liquid end
Technical data
47
Содержание 040830 SST
Страница 54: ...Dimensional drawings 54...
Страница 55: ...Dimensional drawings 55...
Страница 56: ...Dimensional drawings 56...
Страница 57: ...Dimensional drawings 57...