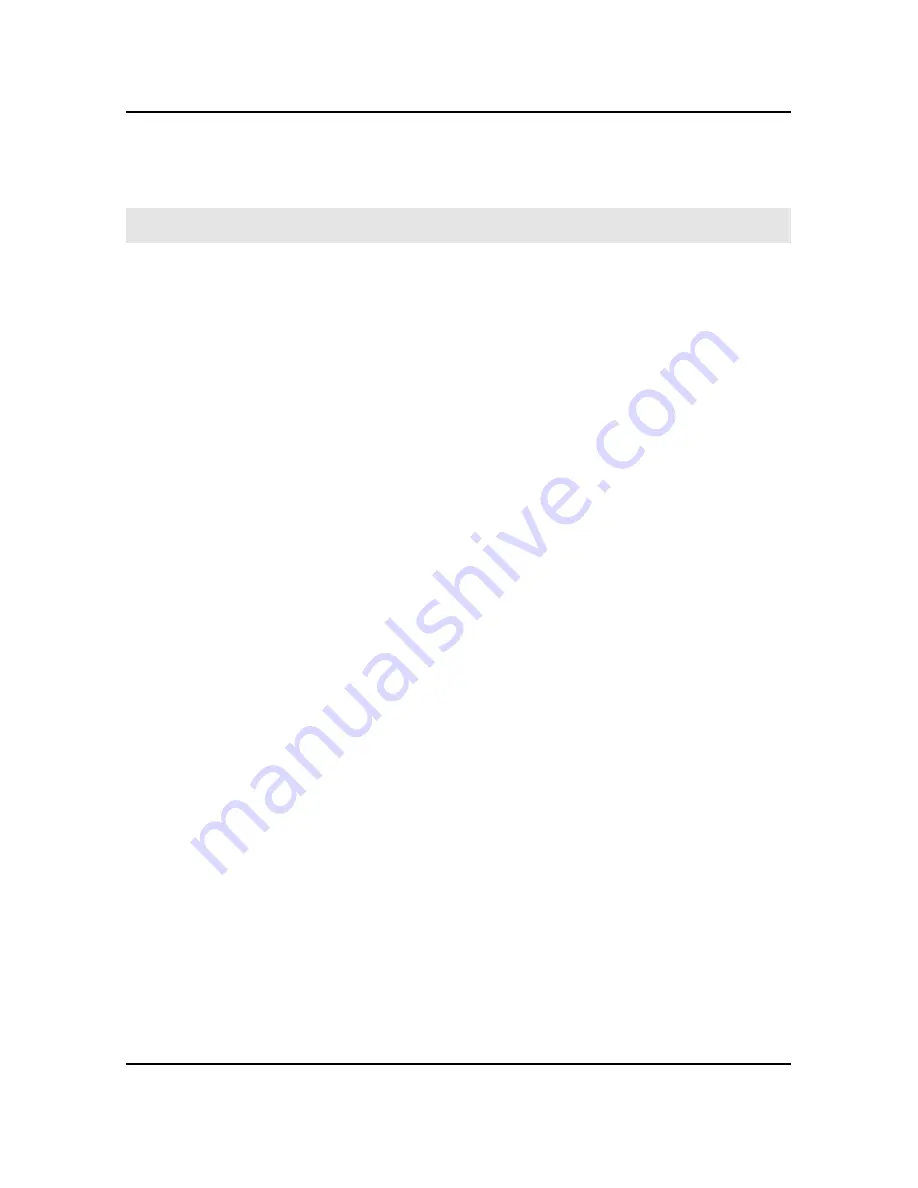
96-14B / Page 2/18
GENERAL WELDING PROCEDURE
Warning:
Park vehicle safely, apply parking brake, stop engine and set battery master switch(es) to the
OFF
position prior to working on the vehicle.
1. Welding must be done only by a qualified and experienced person.
2. Always wear the appropriate safety equipment.
3. Weld in clean and well-ventilated area, and always have an appropriate fire extinguisher within your
reach.
4. The following precautions should be taken to protect the electronic control components :
•
Cut off battery power (battery master switch) from battery compartment.
•
Disconnect wiring harness connectors from ECM (Electronic Control Module). The ECM is mounted
on the starter side of the engine.
•
For vehicles equipped with an automatic transmission, disconnect wiring harness connectors from
ECU (Electronic Control Unit). The ECU is located in rear electrical compartment.
•
For vehicles equipped with ABS (Anti-Brake System), disconnect wiring harness connectors from
ABS Electronic Control Unit. The ABS Electronic Control Unit is located in the front service
compartment.
•
Do not connect welding cables to electronic control components.
5. Thoroughly clean area where welding has to be made.
6. Perform welding.
7. Because of material thickness, it is recommended to use a semi-automatic electric arc welding:
•
GMAW (Gaz Metal-Arc Welding) process;
•
welding wire conforming to AWS (American Welding Standards) A5.9 specifications;
•
308L type welding wire with 0.035" diameter (0,9 mm);
•
voltage: 18 volts to 22 volts;
•
current: 225 amperes to 250 amperes;
•
gas used: T90-H (90% helium, 7,5% argon, 2,5% CO
2
).
If necessary, with lots of precaution to avoid perforation material, it is possible, but not recommended, to
use a conventional electric arc welding machine, in accordance with the following specifications:
•
SMAW (Shield Metal-Arc Welding) process;
•
welding rod conforming to AWS (American Welding Standards) A5.9 specifications;
•
308L-16 type welding rod 3/16" in diameter (2,4 mm);
•
current: 80 amperes to 85 amperes.
9. Allow welding to cool, then remove slag.
10. Reconnect ECM, ECU and ABS electronic control unit mentioned in step 5.
Содержание PNEUMATIC SYSTEM IMPROVEMENT
Страница 10: ...96 14B Page 10 18 FIGURE 2 PNEUMATIC DIAGRAM REFERENCE DIAGRAM D140196 12095 ...
Страница 11: ...96 14B Page 11 18 FIGURE 3 PNEUMATIC SYSTEM REFERENCE DIAGRAM D140204 12096 ...
Страница 12: ...96 14B Page 12 18 FIGURE 4 PNEUMATIC SYSTEM REFERENCE DIAGRAM D140131 12097 ...
Страница 16: ...96 14B Page 16 18 FIGURE 9 FRONT ELECTRICAL COMPARTMENT 06187 ...
Страница 18: ...96 14B Page 18 18 FIGURE 10 REAR ELECTRICAL COMPARTMENT 06188 ...