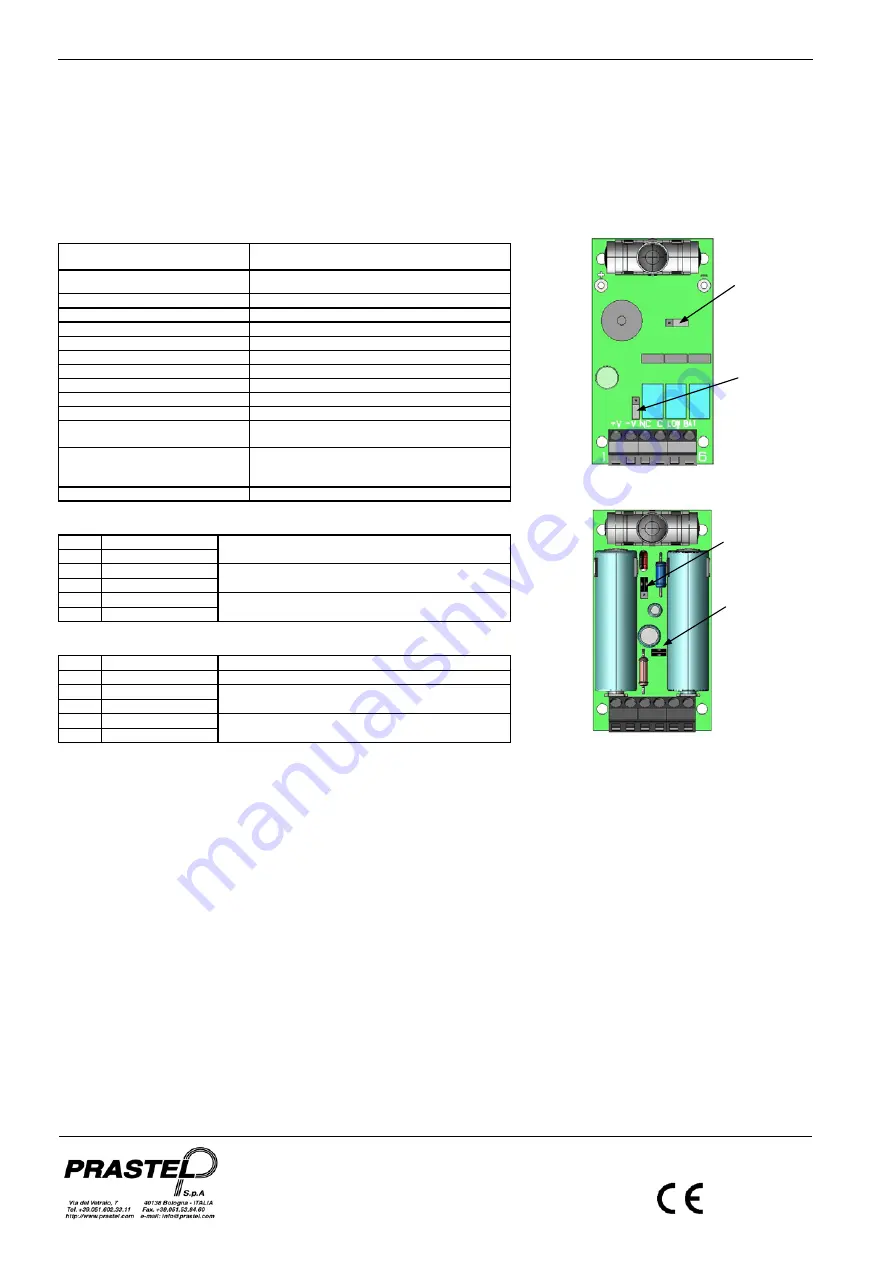
FT25BS2-R
ENGLISH
ISFT25BS2REU_07_07.doc
1. General
Description
The FT25B photocells are fitted with a transmitter that can be powered by two 3V6 2.7Ah lithium Thionyl chloride batteries or with an external 12/24V
AC/DC power supply, selectable with a jumper.
The optical unit (emitter diode + lens) of the transmitter and of the receiver can be oriented in three different directions so it can be adapted to
different installation situations.
The photocell has two terminals for the connection of a free contact of an external safety device (safety edge) and two terminals for the connection of
a resistive edge. The photocell is particularly suited for use on sliding gates, mounted on the mobile part it can be connected to a wire or resistive
safety edge, without having to lay cables or use re-wind cables.
The battery life-span is more than 15 months.
In compliance with European reference standards (Electromagnetic Compatibility 89/336/CEE).
2.
Main technical features
Power supply Transmitter
2 3V6 2.7Ah Lithium Thionyl chloride batteries
Alternatively 12 - 24 V AC/DC
Power supply Receiver
12 -24 V AC/DC
Consumption Transmitter
< 500 µA
Consumption Receiver
30 mA
Container ABS
Dimensions/weight
110 x 50 x 25 mm 200g
Protection rating
IP 45
Infra-red wavelength
950 nm
Relay contact range
0.5 A @ 24 V AC/DC
Infra-red beam range
25 m nominal (8 m outdoor )
Operating temperature
-20 +55° C
Intervention time with triggering of
photocell beam
< 40 ms
Intervention time with triggering of
safety edge connected to terminal
strip
< 60 ms
Reset time
< 150 ms
3.
Receiver terminal strip
1
+V
2
- V
Power supply 12 - 24 V AC/DC
3
N.C./N.O.
4
C
Relay contact normally open or closed depending on
NO/NC selection jumper
5
LOW BAT
6
LOW BAT
Flat battery Normally open contact
4.
Transmitter terminal strip
1
+12 - +24 V AC/DC
Power supply 12 - 24 V AC/DC
2
0 V
Common power supply
3
EDGE
4
EDGE
Terminal for safety edge free contact
(j
ump if not used)
5
EDGE 8K2
6
EDGE 8K2
Terminal for 8K2 resistive edge
(DON’T j
ump if not used)
5. Installation
-
Fix the photocell using the supplied drilling template (fig. 2)
-
Make connections as indicated in the previous paragraphs and
select the transmitter power supply with the specific jumper (J1,
Fig. 1B):
POSITION A: external power supply 12-24 V AC/DC
POSITION B: battery powered
-
Select the same operating frequency on the receiver and on
the transmitter with the specific jumpers (J2, fig 1A & 1B):
Frequency 1: Jumper disabled
Frequency 2: Jumper enabled
-
Connect to the specific terminal strip (terminals 3 & 4, Fig. 1B)
the safety edge or external safety device contact to the
transmitter.
If this option is not used, jump terminals 3 and
4.
-
Connect to the specific terminal strip (terminals 5 & 6, Fig. 1B)
the contacts of the 8K2 resistive edge external to the
transmitter.
If this option is not used, do NOT jump
terminals 5 and 6.
-
Select on the receiver the logic of the NO or NC output contact
with jumper J3.
-
Position on the transmitter the probe in the position from the
three possibilities most suitable to the alignment.
-
Align the beam to the receiver by adjusting the specific fixing
screws “A” (fig. 2) supplied, both on the receiver and the
transmitter.
-
With a voltmeter, measure the tension value on the receiver
test-point. (Fig. 2). This value varies according to various
parameters, among which the distance between the photocells.
The higher the tension value on the test-point the better is the
alignment. The ideal measure should be between 0.5 and 0.6
VDC.
-
Check that the interruption of the infra-red beam causes the
opening of the normally closed contact of the relay on the
receiver and the lighting up of the red LED.
6.
Flat battery signal
The flat battery situation is signalled optically by the transmitter to
the receiver.
The receiver closes the free LOW BAT contact available in the
terminal strip and activates an intermittent buzzer.
The flat battery indication is given one week before the battery is
completely flat.
Once the batteries have been replaced, switch the receiver OFF
then back ON to deactivate the LOWBAT contact and the buzzer.
However, this will happen automatically after 15 minutes.
J1: Power supply
selection
Fig. 1B
(TX)
B
A
J2: Frequency
Selection
1 2 3 4 5 6
Fig. 1A
(RX.)
J2: Frequency
Selection
J3: NO/NC
contact selection
1 2 3 4 5 6
Содержание FT25B Series
Страница 4: ...TEST POINT 0 5 0 6 VDC TX RX TX ...