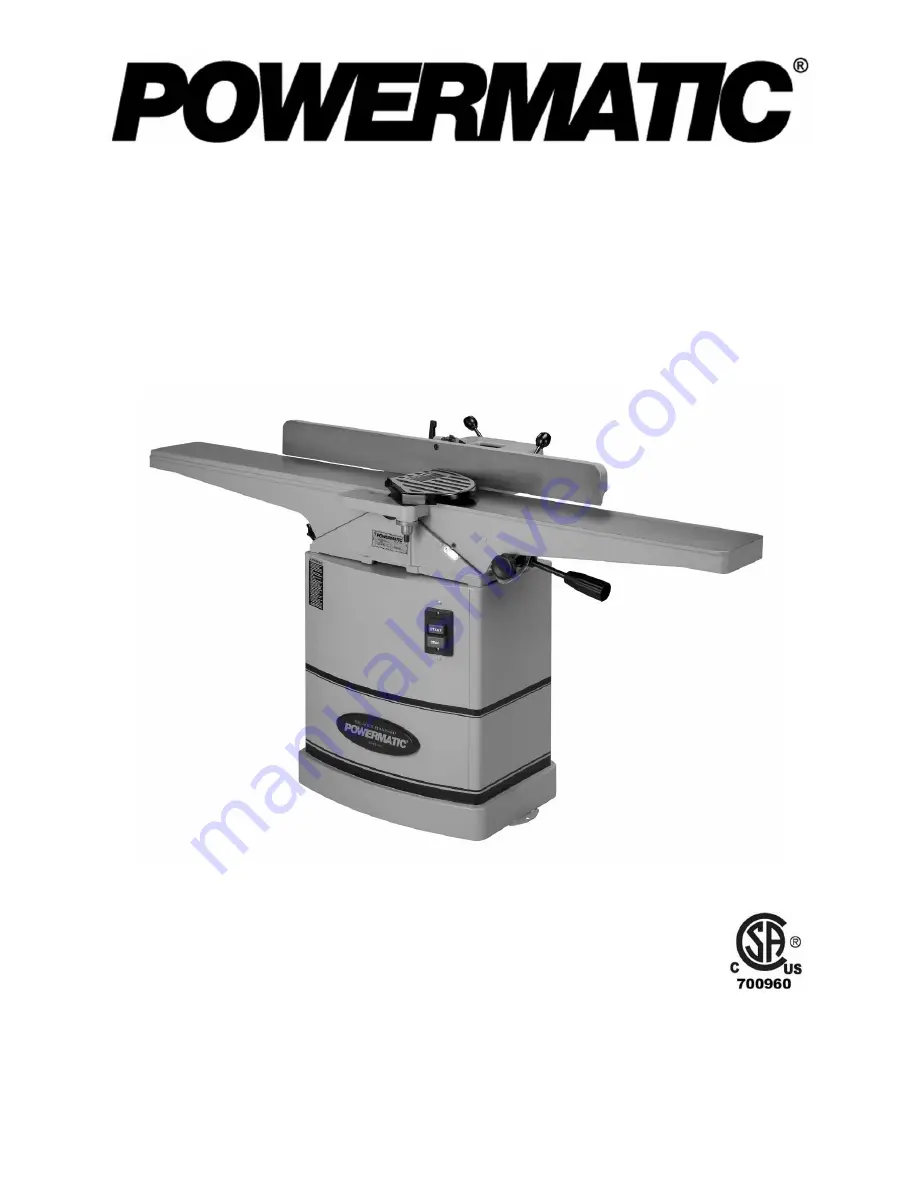
Operating Instructions and Parts Manual
6-inch Woodworking Jointer
Models 54A and 54HH
54A (1791279DXK) serial # 8040543557 and up
54HH (1791317K) serial # 8010540313 and up
WMH TOOL GROUP, Inc.
2420 Vantage Drive
Elgin, Illinois 60123
Part No. M-1791279DX
Ph.: 800-274-6848
Revision C 06/08
www.powermatic.com
Copyright © 2008 WMH Tool Group, Inc.
Содержание 54A
Страница 31: ...31 Stand Assembly All Models POWERMATIC ...
Страница 38: ...38 Wiring Diagram Serial 05060540313 and higher ...
Страница 39: ...39 ...