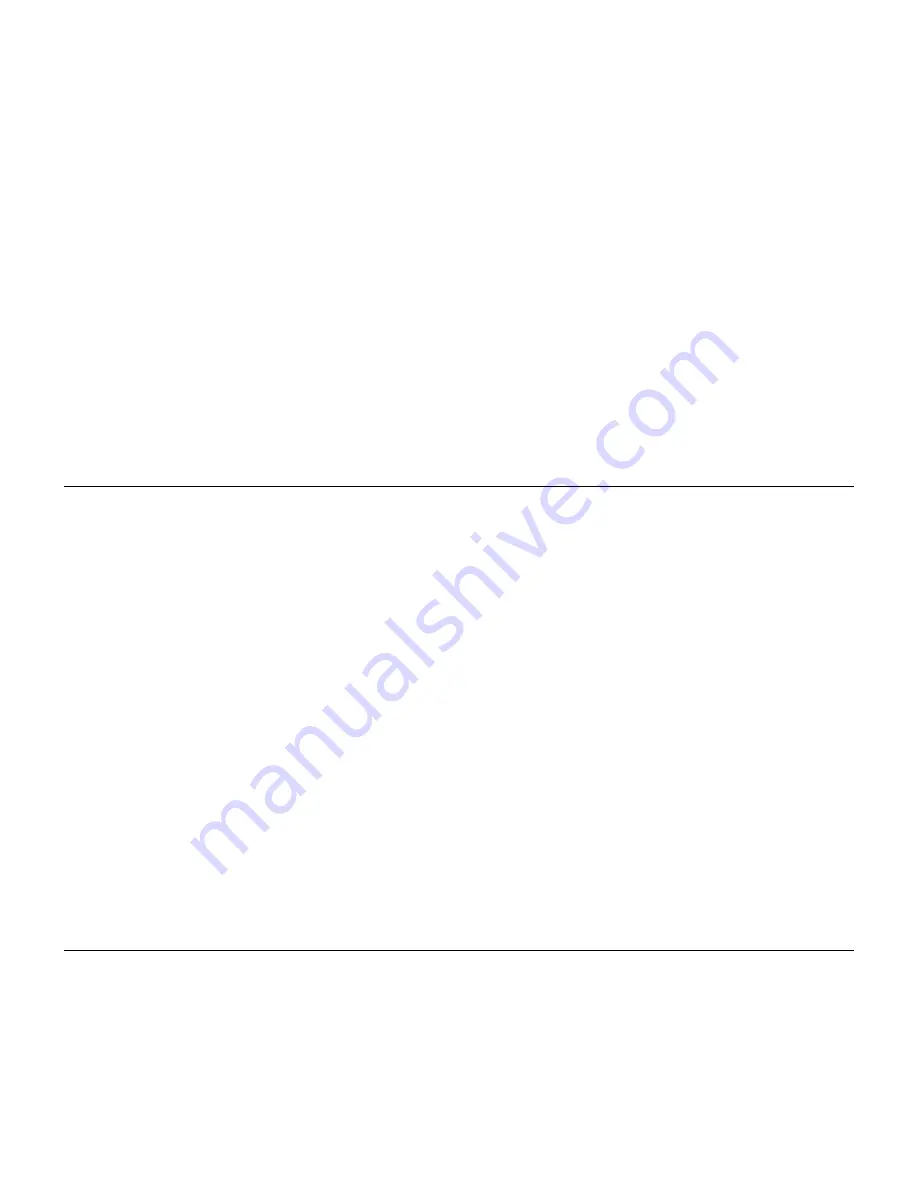
10 Servicing & Cleaning - Page 13
Refer to the separate boiler instructions supplied with the boiler for cleaning the boiler.
To ensure continued efficient operation of the appliance, it is recommended that it is checked and cleaned as necessary at
regular intervals. The frequency of servicing will depend upon the particular installation conditions and usage but in general
once per year should be adequate. It is the law that any service work must be carried out by a competent person such as
British Gas or other C.O.R.G.I. registered personnel.
The following aspects of the fire and installation should be examined and rectified as necessary.
1.
Run the fire and check the operation of its controls and observe the flame picture.
2.
Remove dust and debris from the burner, lint trap, A.S.D and fire interior.
3.
Examine the burner injector and ensure it is clear and undamaged.
4.
Carry out a spillage test, see Section 7, Page 10.
The fire data badge is located at the bottom left hand side of the convector box. The badge will be visible after removal of
the plinth. On completion of the service run the boiler and fire and ensure that they operate correctly.
WARNING:
Before commencing work, turn the fire off and set the boiler switch to off.
Isolate the electricity supply to the boiler and allow the fire and boiler to cool.
IMPORTANT:
Always test for gas soundness after completing any servicing of gas carrying components
and carry out functional checks of controls.
10.1
Remove the Fire
a)
Perform General Access - See 11.1, Page 14.
b)
Remove the screws securing the convector box to the outer metal surround and remove the convector box.
10.2
Inspect & Clean Components
a)
Carefully brush off any dust or deposits from all the ceramic pieces. Examine all the ceramics and replace any that are
broken.
b)
Remove and inspect the Burner Injector - See 11.3, Page 16. Clean by blowing through or washing. Do NOT clear the
injector with a pin or wire.
c)
Check the condition of the Atmospheric Sensing Device, remove any deposits from the thermocouple tip using a fine
wire brush.
d)
Check the condition of the self adhesive foam strips, replace if necessary.
e)
Wipe any deposits from the stainless steel firebox inner using a damp cloth.
10.3
Re-fit the Fire
a)
Re-fit the convector box and secure to the outer metal surround using the screws previously removed.
b)
Re-fit the burner tray and secure to the convector box using the wing nuts previously removed.
c)
Re-connect the gas supply, open the gas fire isolation tap and test for gas soundness.
d)
Re-fit the vermiculite and ceramics as shown in the instruction sheet titled "Fitting the Firebed Components" (Part No.
966/9350/3) that was supplied with the ceramic packs.
e)
Light the fire, test all joints around the fire for gas soundness, check the control tap operation and test for spillage
(Section 7, Page 10).
f)
Clean the outer case of the fire as described in the Instructions for Use.
Содержание Illusion
Страница 7: ...Installation Page 7 ...
Страница 8: ...Installation Page 8 ...